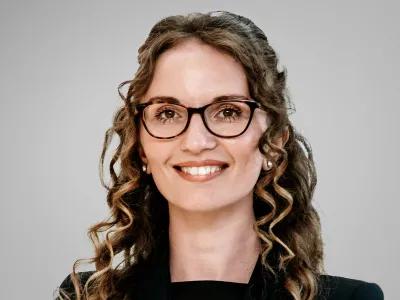
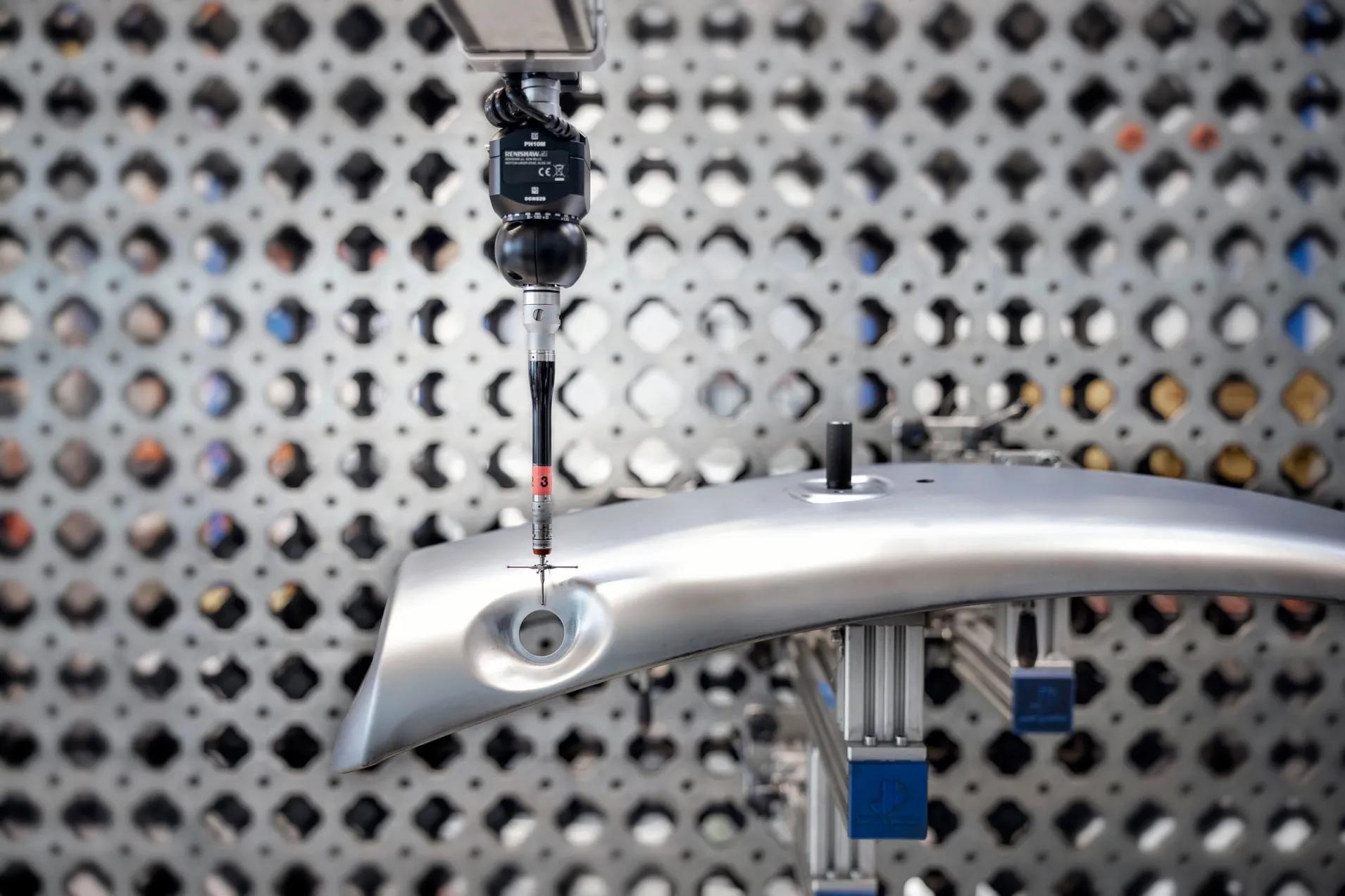
Certificates
With a comprehensive level of service, we deliver the components and systems just-in-time or just-in-sequence – upon request also in a vehicle-related manner (one-set flow) – directly to the assembly line of our customers.
Our production system is geared towards the usual high number of variants and batch size of one associated with commercial vehicles together with the restriction of short throughput times and a desired delivery performance of 100%. In this connection, we constantly monitor the entire supply chain by means of our ERP system in order to have the required direct material available at the required point in time.
Our range of services covers the following:
- Individually coordinated logistics concepts
- Just-in-time or just-in-sequence deliveries
- Vehicle-related deliveries (one-set flow)
- Deliveries starting at a quantity of 1+x
- Customs declaration and clearing
HÖRMANN Automotive supports value-based transparency and performance as well as a structured way of working so that we can focus on the requirements of the automotive and commercial vehicle industries with the highest quality standards while complying with the occupational safety and environmental management systems.
We see change as an opportunity! We are pro-actively tackling the requirements being placed on our business model by changing markets, volatile customer requirements, numerous product changes, complex customer products with numerous variants as well as climate change. We face up to the changes promptly and continuously optimise our processes to achieve new target states.
Due to decoupled shifts with a demand-oriented end of shift as well as quality-conscious, well-trained and flexibly deployable employees, it can always be ensured that the product quantities demanded by the customer are available as per the delivery date. All our processes have the required contingency plans in order to be in the position to deliver at all times. This equally applies to our IT systems. Customer release orders are received via our SAP system and accordingly forwarded to all suppliers.
To fulfil our social responsibility, we undertake to protect the environment through a circular economy, starting with the selection of the resources up to a recycling-compatible product concept. We also communicate this onto our partners. It is similarly our goal to design the workplaces of our employees so that they are safe and attractive via the minimal use of hazardous materials and reduced exposure to hazards and to safeguard them in the long term.
For all products and services, the work to various different quality standards ensures a globally recognised and certified as well as sustainable quality and reliability that is checked and guaranteed via regular shopfloor visits and audits as well as constant further development. In this way, we continuously create added value for our customers.
Our environmental management system is certified to various different standards. We strive for continuous improvement and further development. The environmental management system is continuously re-evaluated and we are always on the lookout for new ways to further conserve resources and protect the environment.
In accordance with the operational quality, occupational safety and health management systems, we actively approach our employees and involve them in our decision-making. We take our social responsibility as a company very seriously. This is why sustainability and the protection of the environment play an important role in our corporate philosophy. As a result, we use energy and resources in a responsible and efficient manner.
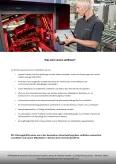
Leitlinien
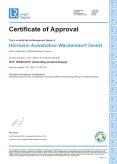
IATF 16949:2016
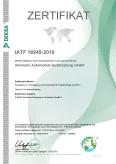
IATF 16949:2016

IATF 16949:2016
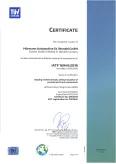
IATF 16949:2016
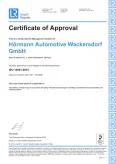
ISO 14001:2015
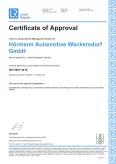
ISO 9001:2015
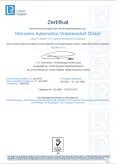
ISO 9001:2015
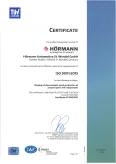
ISO 9001:2015
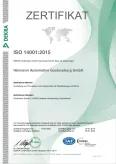
ISO 14001:2015
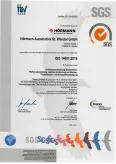
ISO 14001:2015
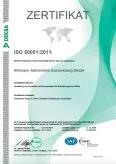
ISO 50001:2011
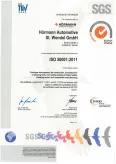
ISO 50001:2011
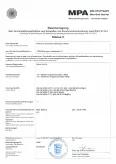
DIN V 4113-3:2011
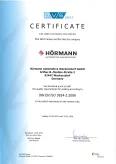
DIN EN ISO 3834-2:2006
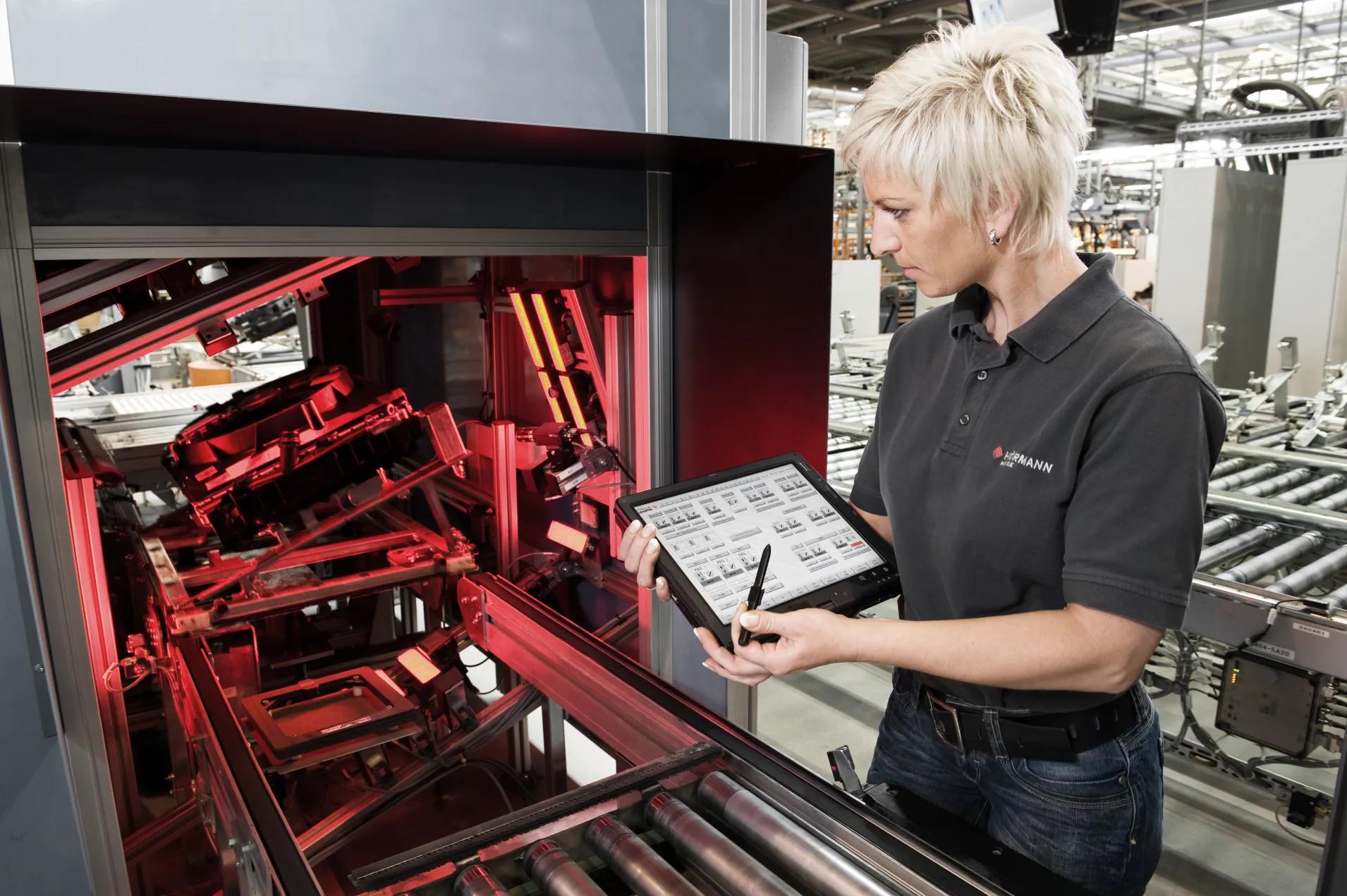
References for E-Mobility
The electrification of the drive world is continuing unabated – whether as hybrid or fully electric. The electric drive is no longer just for passenger car traffic: Hybrid and electric buses also are winning over admirers with less noise and lower consumption. Commercial vehicles can thus drive into city centres in spite of environmental zones and night-time noise restrictions.
HÖRMANN Automotive sees itself as a competent supplier and contact for the following topics:
- Charging infrastructure
- Micromobility
- Innovative battery carrier concepts
To be able to support the trend topic of “e-mobility” to the maximum, the infrastructure is key as the system can only function with this. HÖRMANN Automotive is positioning itself as a neutral industrialiser and assembly service provider for charging stations, for example. The plant in Wackersdorf current offers the D Module (production quality assurance certificate).
The discussions about climate protection and the change in the automotive sector are also resulting in new players in the market. HÖRMANN Automotive defines micromobility as small electric vehicles for urban life and the last mile. In this connection, new automotive OEMs and products such as the e-scooter are appearing on the market. HÖRMANN Automotive is also present here as a neutral industrialiser & assembly service provider. The plant in Wackersdorf is using its experience of recent years here and is implementing quality standards for the customers.
Our focus lies in particular on the innovative battery concepts. The chassis for light commercial vehicles (LCV) in the “Last Mile” area of HÖRMANN Automotive is characterised by a bionic lightweight design approach that can be seen both in the topology and in the component design. The non-linear chassis topology facilitates systemic protection of the energy storage units in the chassis and thus reduces the weight and costs for the accommodation and protection of the batteries. The non-linear longitudinal members are made in turn from steel multi-chamber profiles that are designed specifically for the absorption of impact energy in the case of a side crash. The underlying, innovative production technology allows a high number of variants in the profile configuration without additional tooling costs and is thus able to cover a high number of vehicle variants with regard to the wheelbase and battery dimensions. The vehicle is equipped with wheel hub direct drives and thus has a reduced entrance height and at the same time maximises the potential loading volume of the body.
In this connection, HÖRMANN Automotive sees itself as a system partner of customers – from the development to the production of innovative thick plate concepts, welded components, fine sheets for body parts to the assembly of mechanical and mechatronic assemblies. We orientate all processes to customer requests and adapt them accordingly. Thanks to the cooperation in what are known as ecosystems with established system suppliers as well as start-ups, highly innovative solutions are developed for the electromobility of the future.
Customers
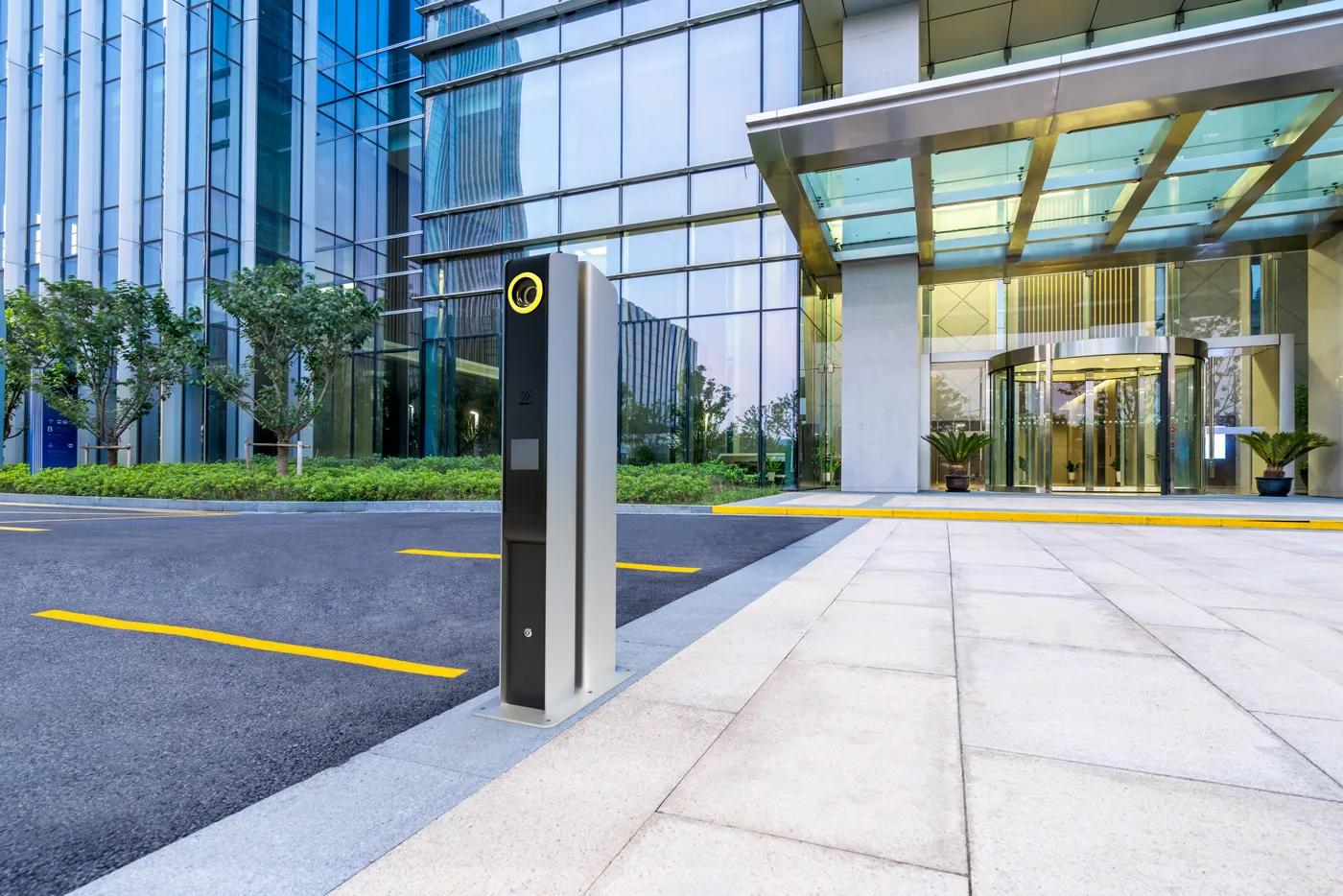
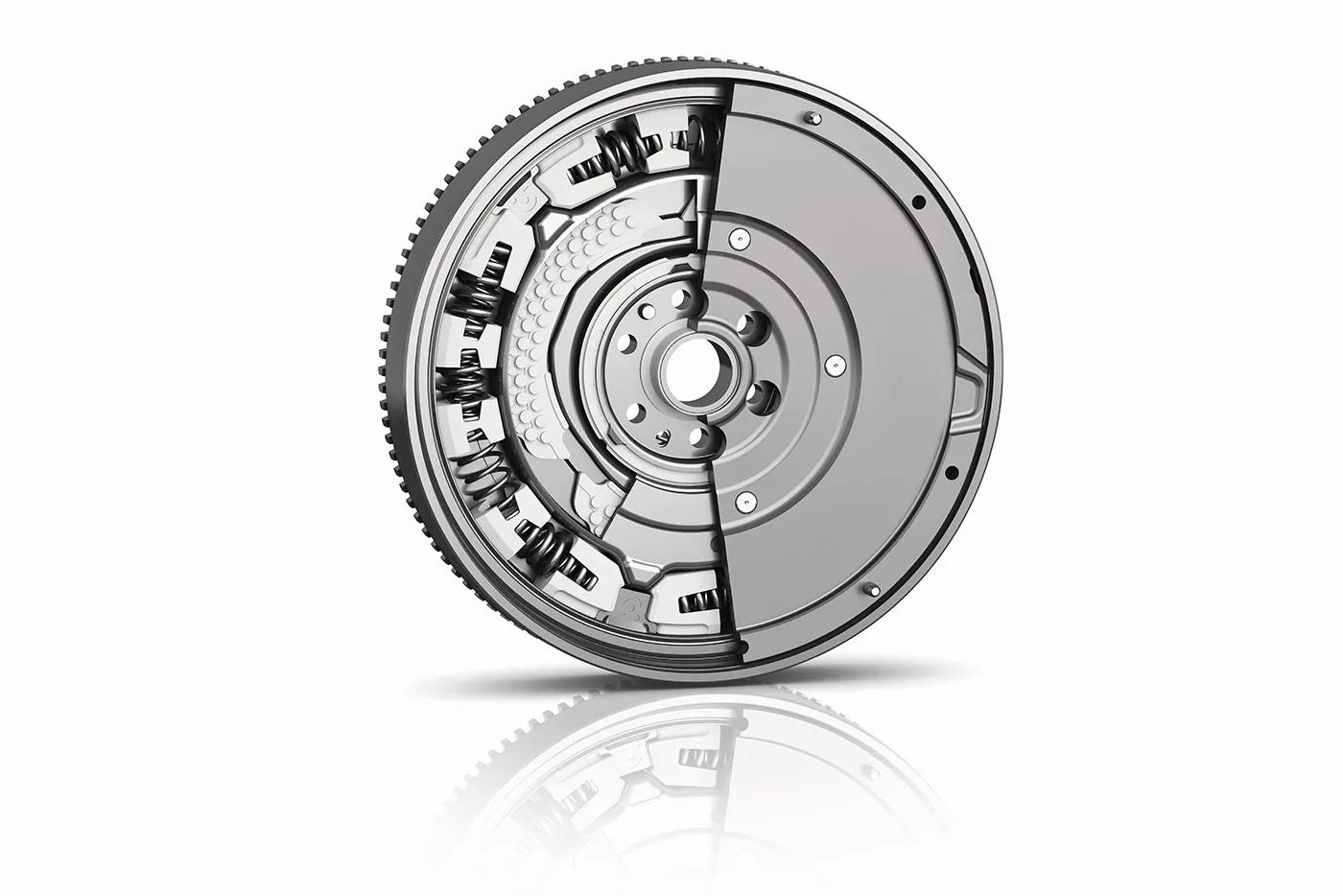
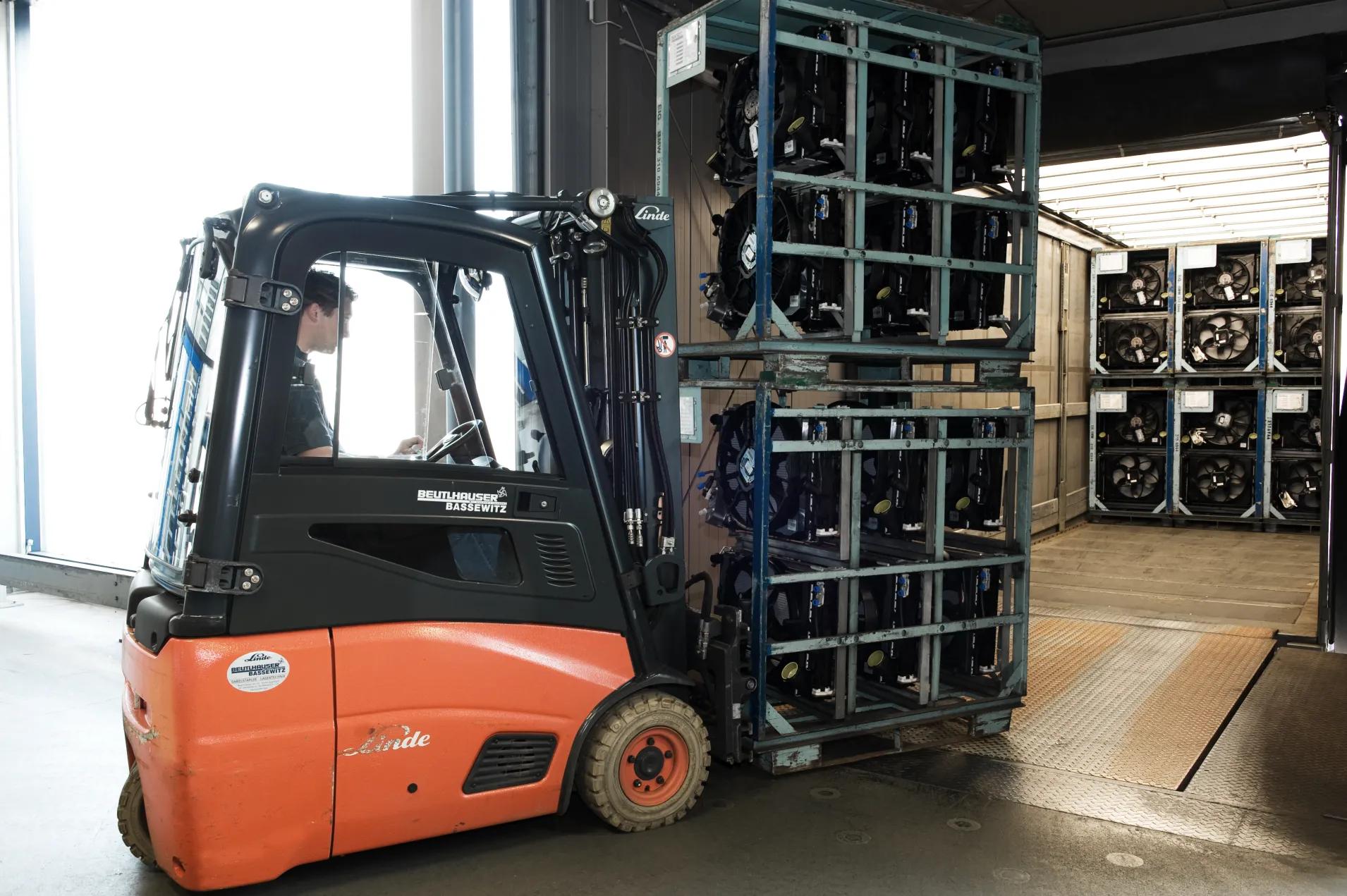
References for Forklift Trucks
Goods go nowhere without it – the forklift truck! The scopes of application of this means of transport are diverse. They are used in retail and in industry as well as in logistics centres. The range of products on offer is accordingly wide. It extends from manually operated pallet lift trucks to forklifts with electric motors, gas or diesel engines to heavy-duty lift trucks with a load-carrying capacity of 50 tonnes.
What do we produce for the forklift truck sector?
HÖRMANN Automotive delivers welded assemblies in low, medium and high volumes. We advise our customers already in the offer process in order to achieve the best result for the final customer together. A wide range of simultaneous engineering instruments is available to us, with the help of which the development times can be minimised and the quality of the components can be influenced as early as in the product creation process.
The single part production (2D/3D lasering, nibbling, edging, rolling, bending, forming, deep-drawing) upstream of the welding process as well as the production and procurement of the required jigs and fixtures are part of the range of services provided by HÖRMANN Automotive. Our expertise when it comes to manual and semi-automated welding processes and the mastering of fully automated production in the high-volume sector are clear proof of our extensive range of services in the welded assembly sector. If required, we also deliver painted assemblies and systems JIT/JIS directly to the assembly line of our customers.
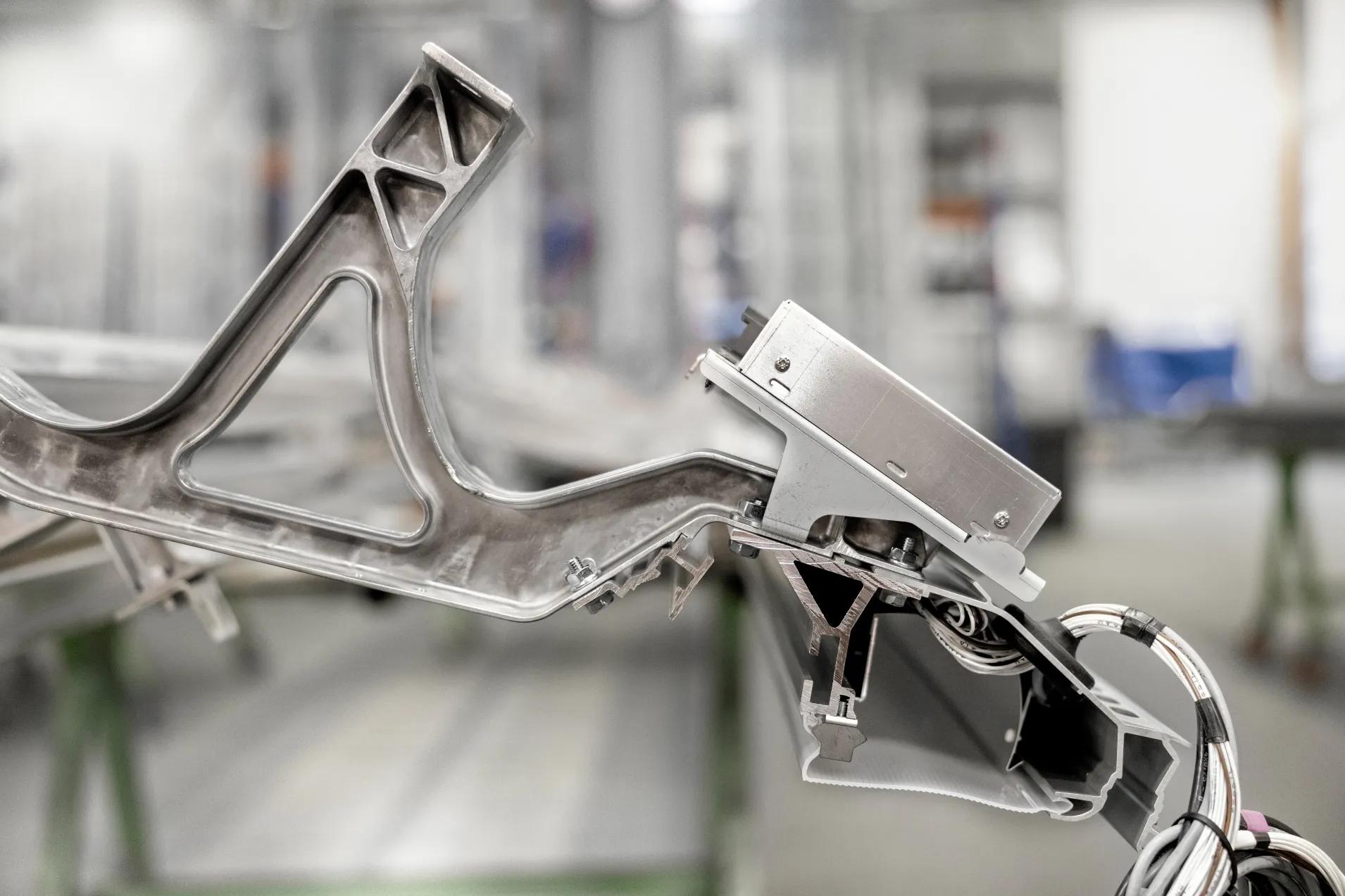
References for Buses
Goods go nowhere without it – the forklift truck! The scopes of application of this means of transport are diverse. They are used in retail and in industry as well as in logistics centres. The range of products on offer is accordingly wide. It extends from manually operated pallet lift trucks to forklifts with electric motors, gas or diesel engines to heavy-duty lift trucks with a load-carrying capacity of 50 tonnes.
What do we produce for the forklift truck sector?
HÖRMANN Automotive delivers welded assemblies in low, medium and high volumes. We advise our customers already in the offer process in order to achieve the best result for the final customer together. A wide range of simultaneous engineering instruments is available to us, with the help of which the development times can be minimised and the quality of the components can be influenced as early as in the product creation process.
The single part production (2D/3D lasering, nibbling, edging, rolling, bending, forming, deep-drawing) upstream of the welding process as well as the production and procurement of the required jigs and fixtures are part of the range of services provided by HÖRMANN Automotive. Our expertise when it comes to manual and semi-automated welding processes and the mastering of fully automated production in the high-volume sector are clear proof of our extensive range of services in the welded assembly sector. If required, we also deliver painted assemblies and systems JIT/JIS directly to the assembly line of our customers.
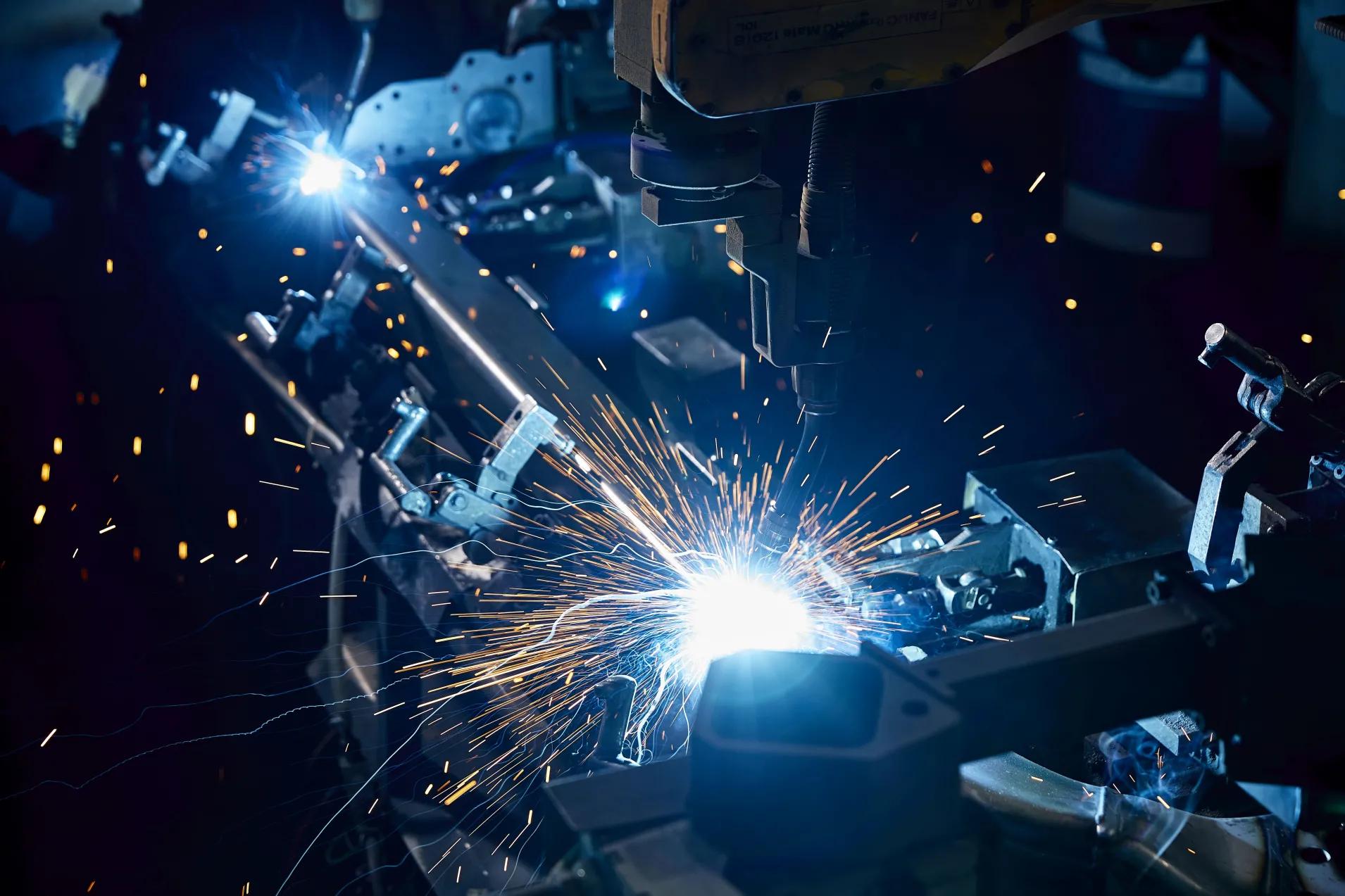
References for Construction Machinery
The German construction machinery industry encompasses mining, construction and construction material machinery. It is used for construction projects, the transport of auxiliary construction materials and the processing of construction materials. The range here extends from diggers to conveyors to fixed-location equipment. With approximately 32%, earthmoving equipment is one of the most important machinery categories in the overall sector turnover. This includes hydraulic excavators.
What do we produce for the construction machinery sector?
HÖRMANN Automotive produces hydraulic tanks of up to 1,600 l as an integral part of the equipment system including the colour scheme and JIT/JIS delivery. These complex and sophisticated systems are often subject to very high technical requirements.
We are known at our customers in the sector for fully assembled, ready-to-install systems – produced in low volumes with a very high number of production variants. HÖRMANN Automotive is equipped for the customer needs, which often come in at short notice, and has aligned the procurement logistics and production processes to reflect this. Our competent and flexible employees make a huge contribution here.
It is important to us to know the qualitative, technical and time-related challenges of our customers in order to fulfil the expectations as a recognised system supplier with this knowledge. For our customers, we are an innovative, competitive and reliable supplier that helps shape their success on a partnership basis.
Customers
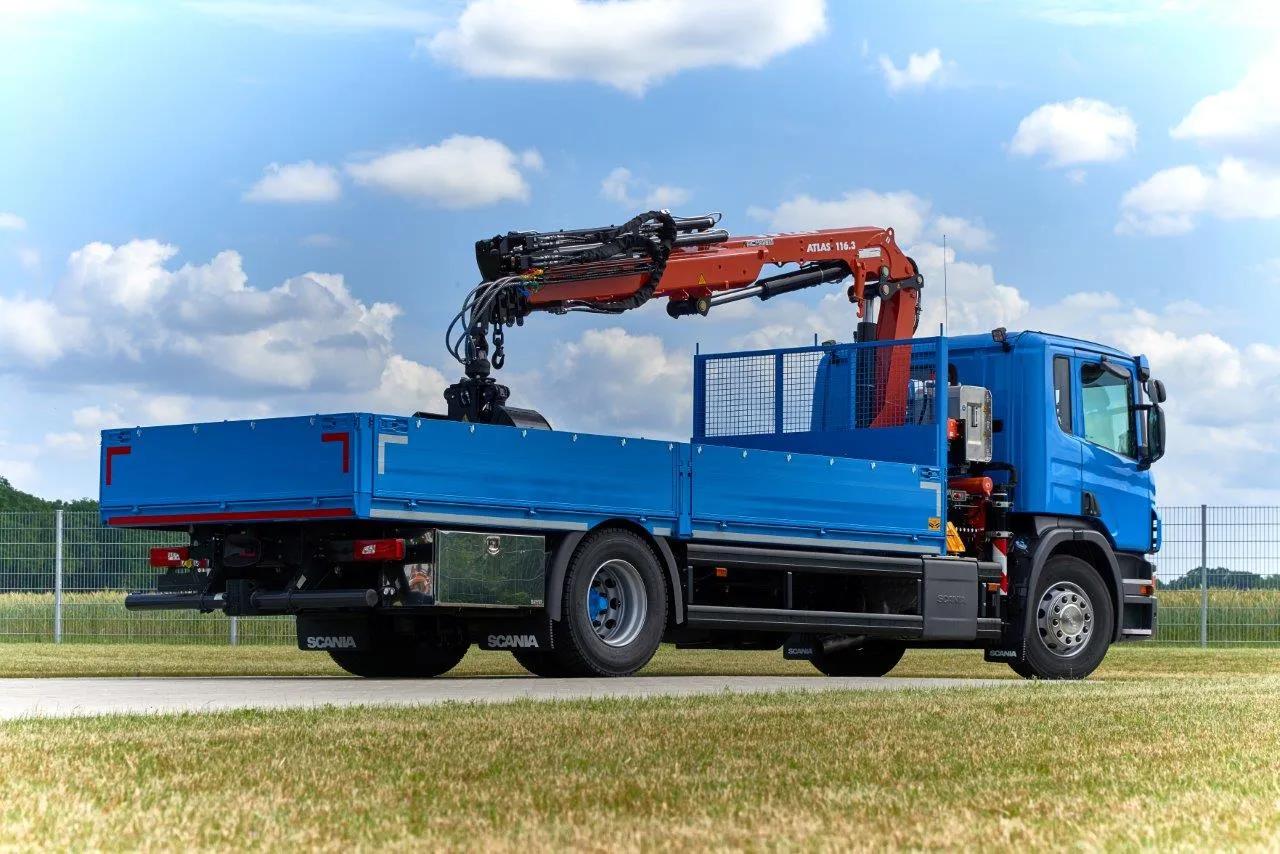
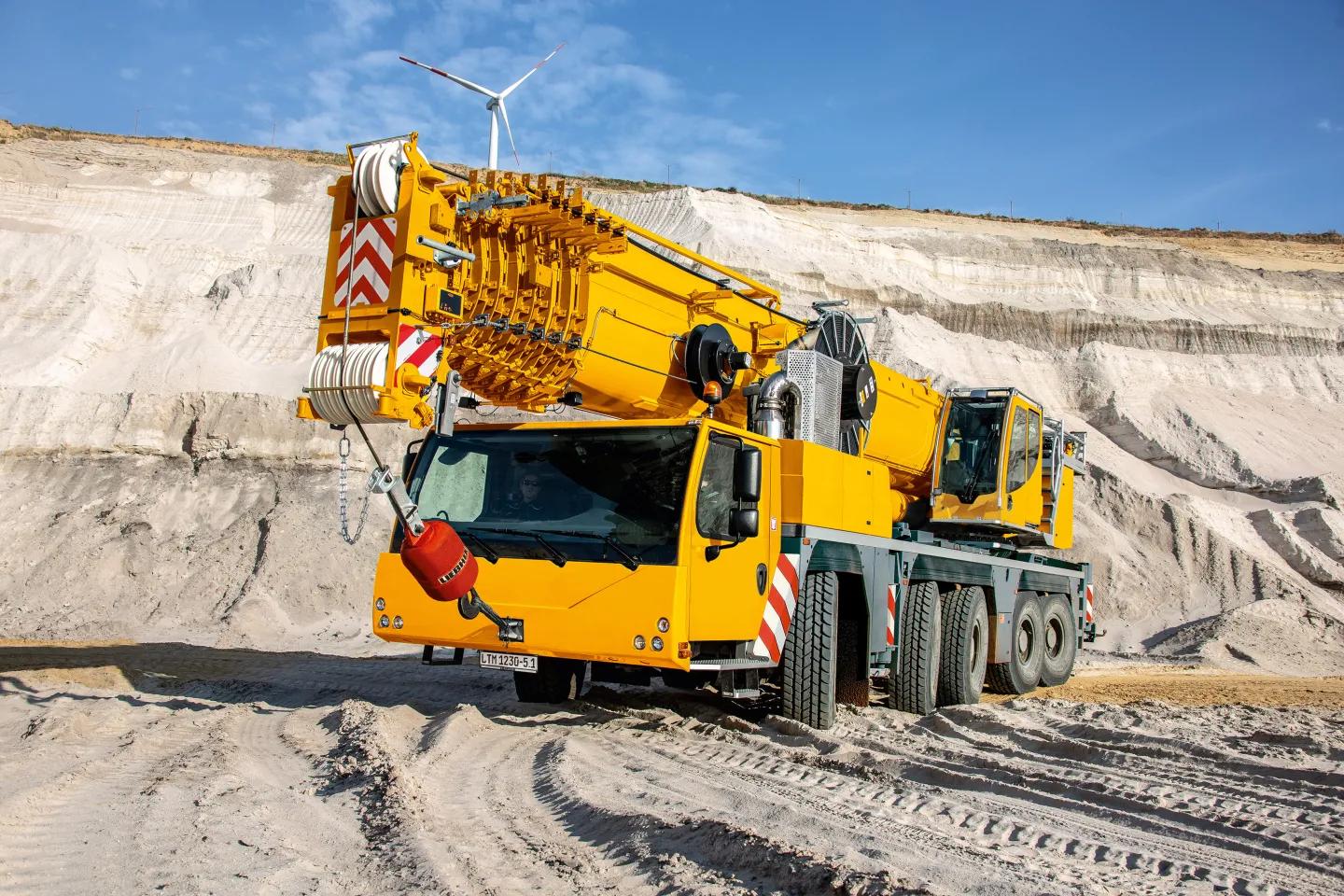
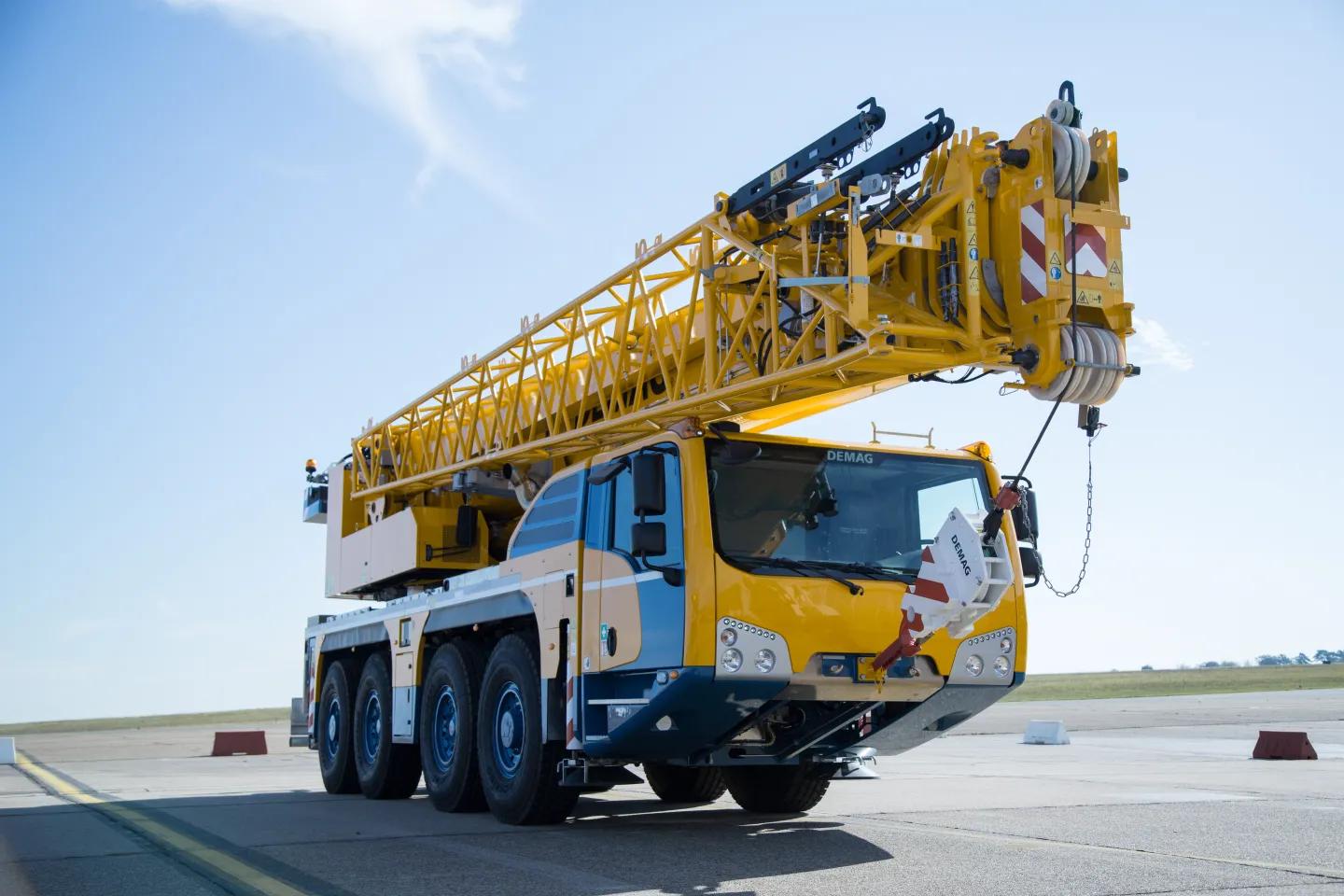
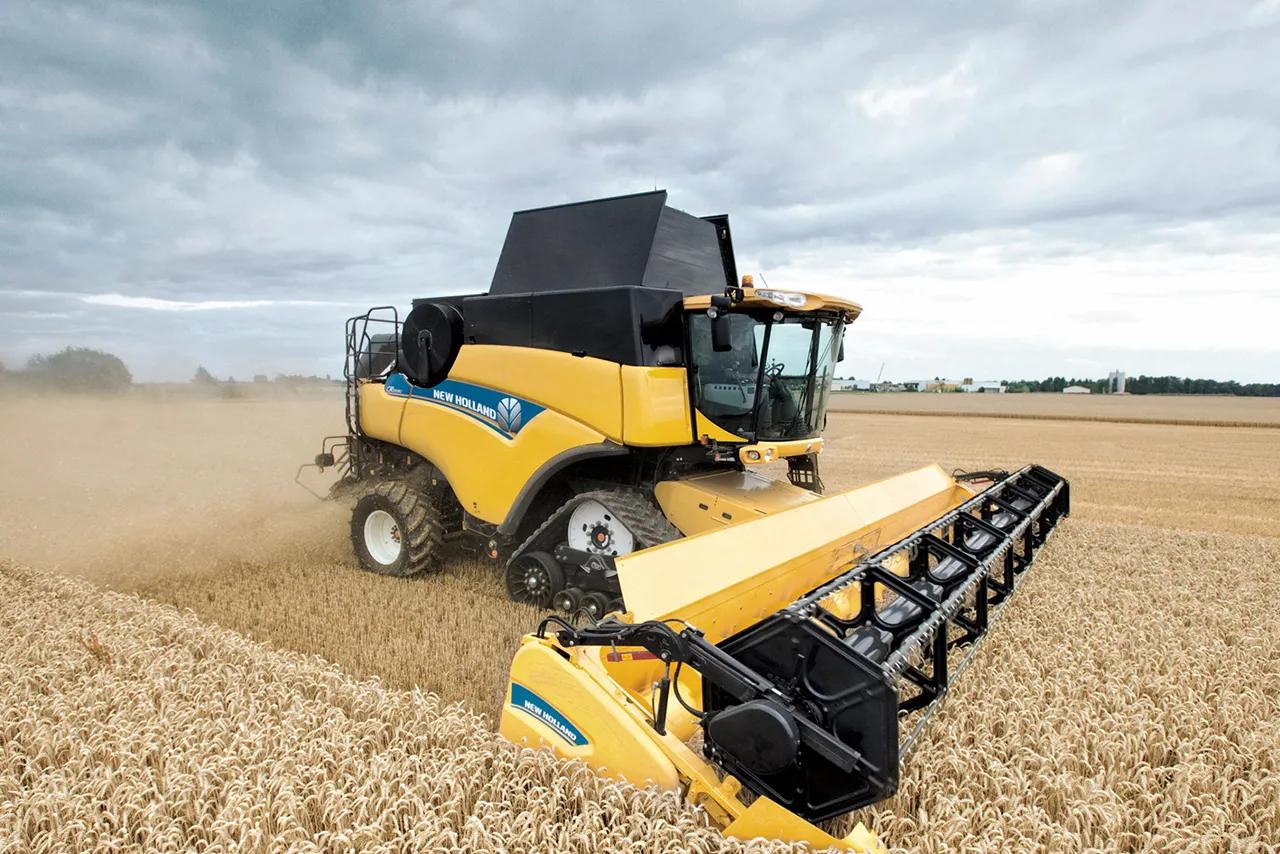
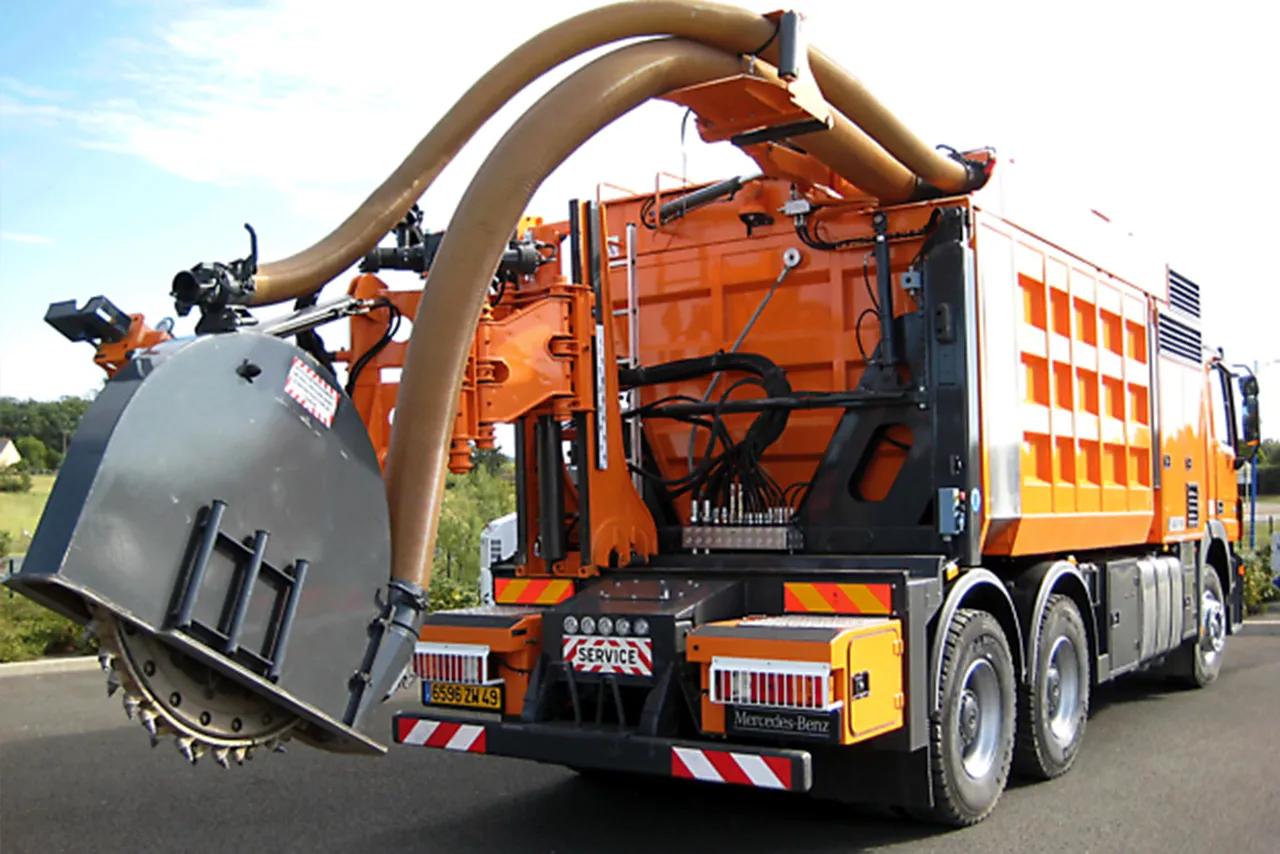
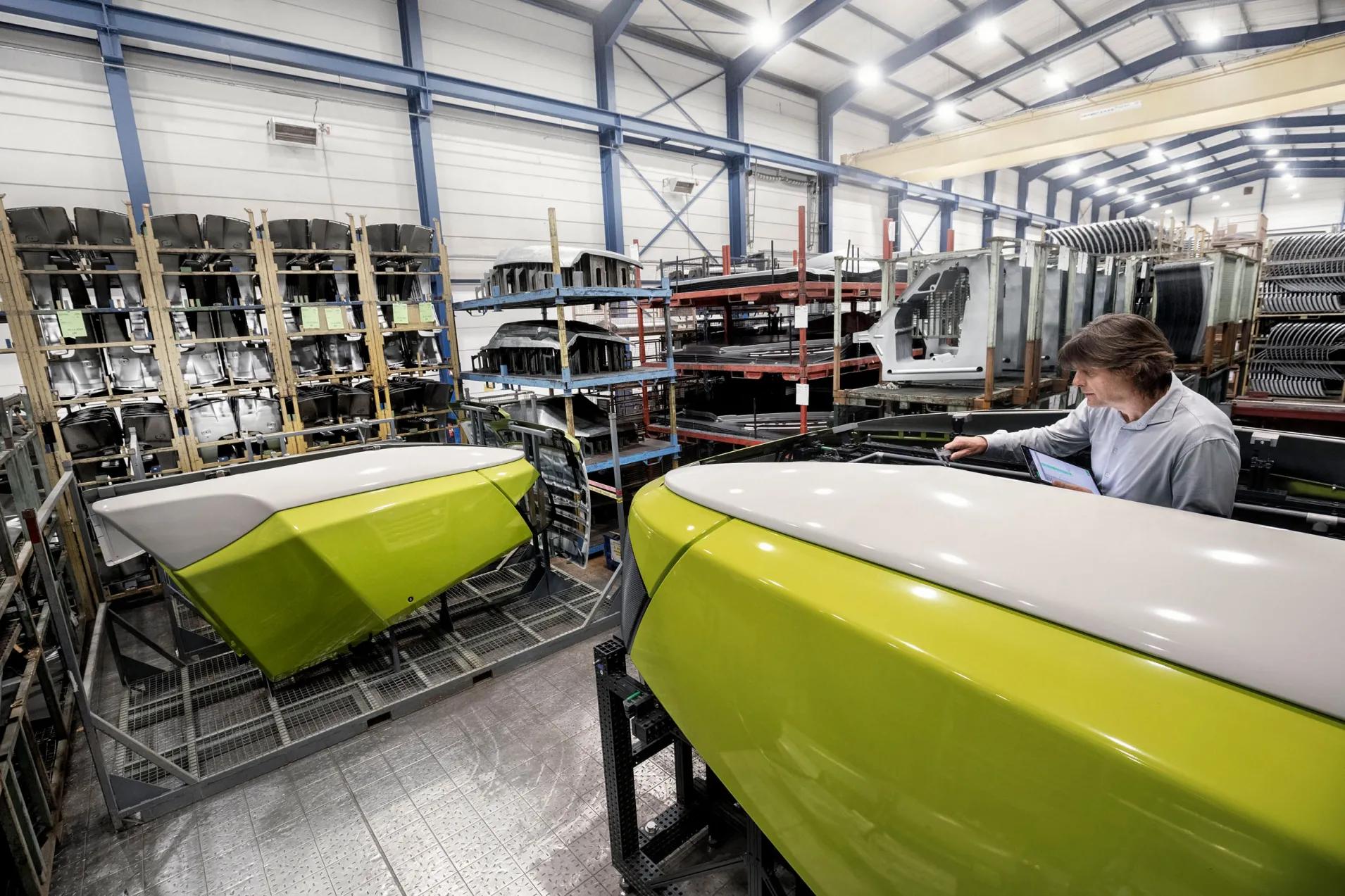
References for Agricultural Machinery
The German agricultural machinery industry is one of the ten largest special sectors in mechanical engineering. Due to its high level of innovation and production quality, it also has an excellent competitive position internationally. The industrial sector has undergone a period of stable further development in recent years – in spite of crisis situations abroad. Almost every eighth employee in Germany is active in the agricultural and food industries.
What do we produce for the agricultural machinery sector?
HÖRMANN Automotive produces large panel systems, fuel and hydraulic tanks, chassis, press-hardened wear and welded assemblies as well as single parts made from steel and aluminium for the agricultural machinery industry. High flexibility in production with demand- and process-oriented working stock procurement and production technology are the key to success here. The “Off-Road” business segment is characterised in general by low-volume demands and seasonal delivery orders from our customers.
All processes at HÖRMANN Automotive are focused on the products of our customers. For the projects, we implement the development, sales, project management, quality planning and advanced production planning in the product creation process in a demand-based manner. Customers can rely here on our many years of in-depth experience in the following production processes: Deep drawing, folding, 2D/3D lasering, welding, adhesive bonding and other joining methods as well as colour schemes and logistics with JIT/JIS delivery. Renowned brands such as Claas have put their trust in us and our expertise for many years.
»Our aspiration is excellence in development, production and logistics. With our many years of expertise and our passion, we design products for the agricultural machinery industry that combine all the advantages of design and function.«
Jürgen Schmidt-Nicola, Head of Off-Road Sales – Agricultural Machinery Division
Customers
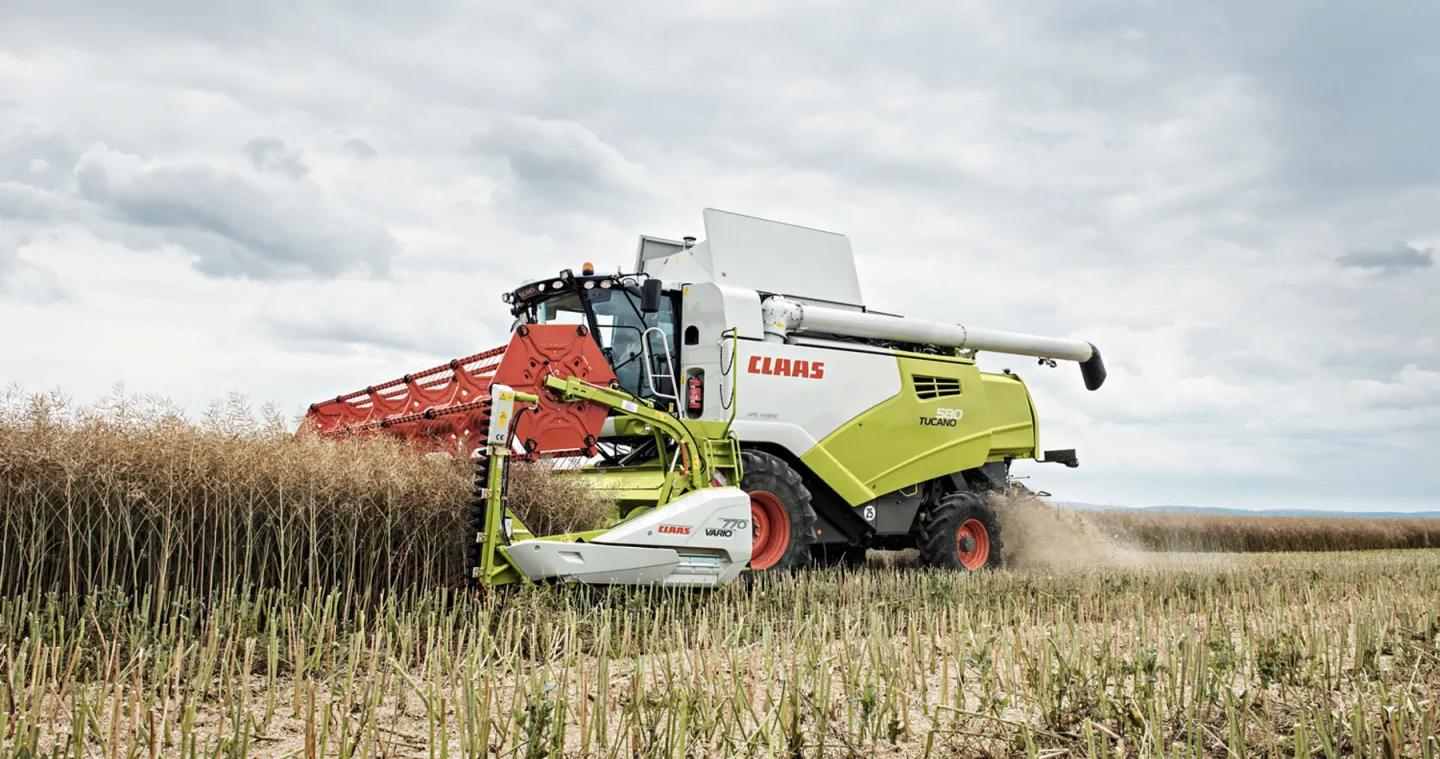
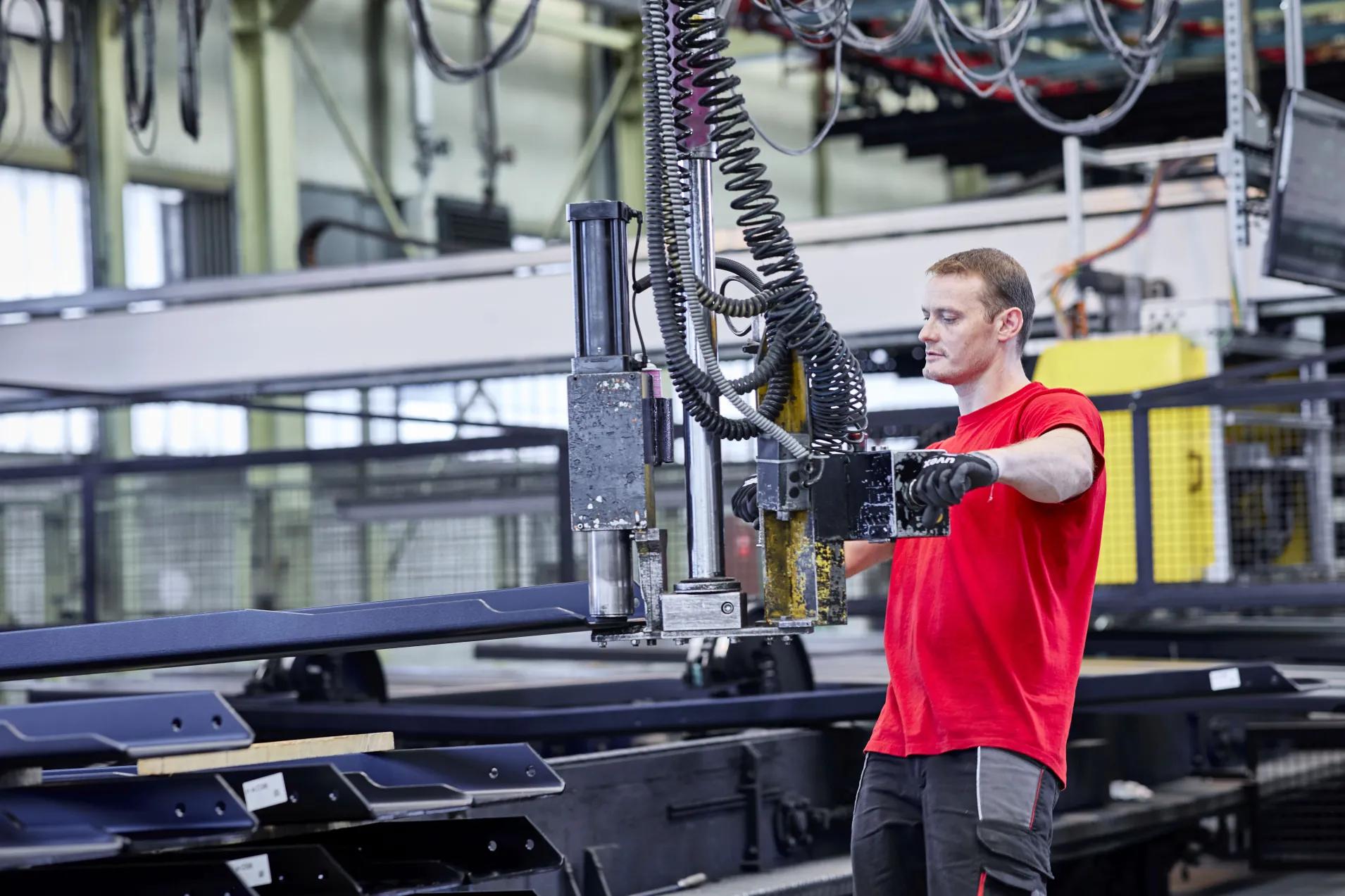
References for Commercial Vehicles
Light- and heavy-duty commercial vehicles still bear the brunt of the work related to the constantly increasing freight transport in Europe and will in the future still play an indispensable role. In Europe, the commercial vehicle industry within the automotive industry is still often overshadowed by the passenger car manufacturers. However, the overall economic importance of the sector is huge and the industrial sector is already a driver of new technologies and innovations today.
The sector is faced with challenging tasks like never before: Payload optimisation, specific sector solutions, fuel efficiency, the associated target of CO2 reduction and sophisticated safety systems as well as the lowest possible emissions mean our customers are confronted with huge challenges.
What do we produce for the commercial vehicle sector?
HÖRMANN Automotive sees itself as a forming specialist and manufacturer of metallic components and systems for the commercial vehicle industry. We produce chassis parts such as longitudinal frame members and detachable frame components as well as large thin-sheet components made from steel and aluminium at our locations in Germany and Eastern Europe. We are also specialised in the forming of pipes and media-conducting lines.
The production-related specialisation in commercial vehicles allows us to drive forward innovations in a targeted manner to satisfy the growing requirements of our customers. This is achieved via further technological development in a broad partner network and also by close cooperation with our internal vehicle development. As a full-service system provider, we thus cover the entire value-added chain from development to production to logistics and service. The focus here is always on the product requirements of our customers, for whom we create individual solutions.
»A decisive change lies ahead for the commercial vehicle industry. This is why we are deliberately exploring new ways in which we can flexibly adapt our products and services to the changed requirements of our customers and the market.«
Christian Petters, Head of Development and Sales – Commercial Vehicles Division
Customers
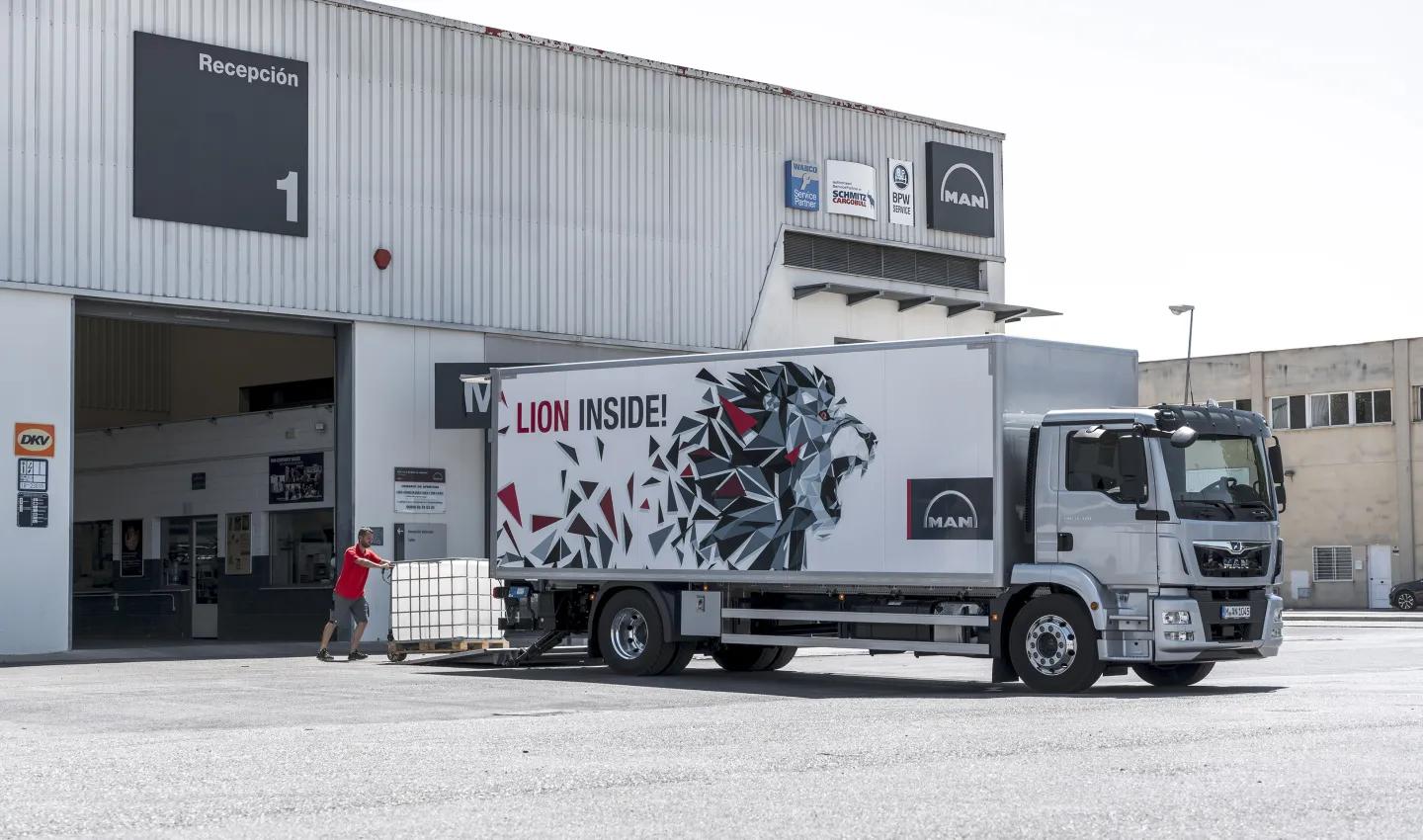
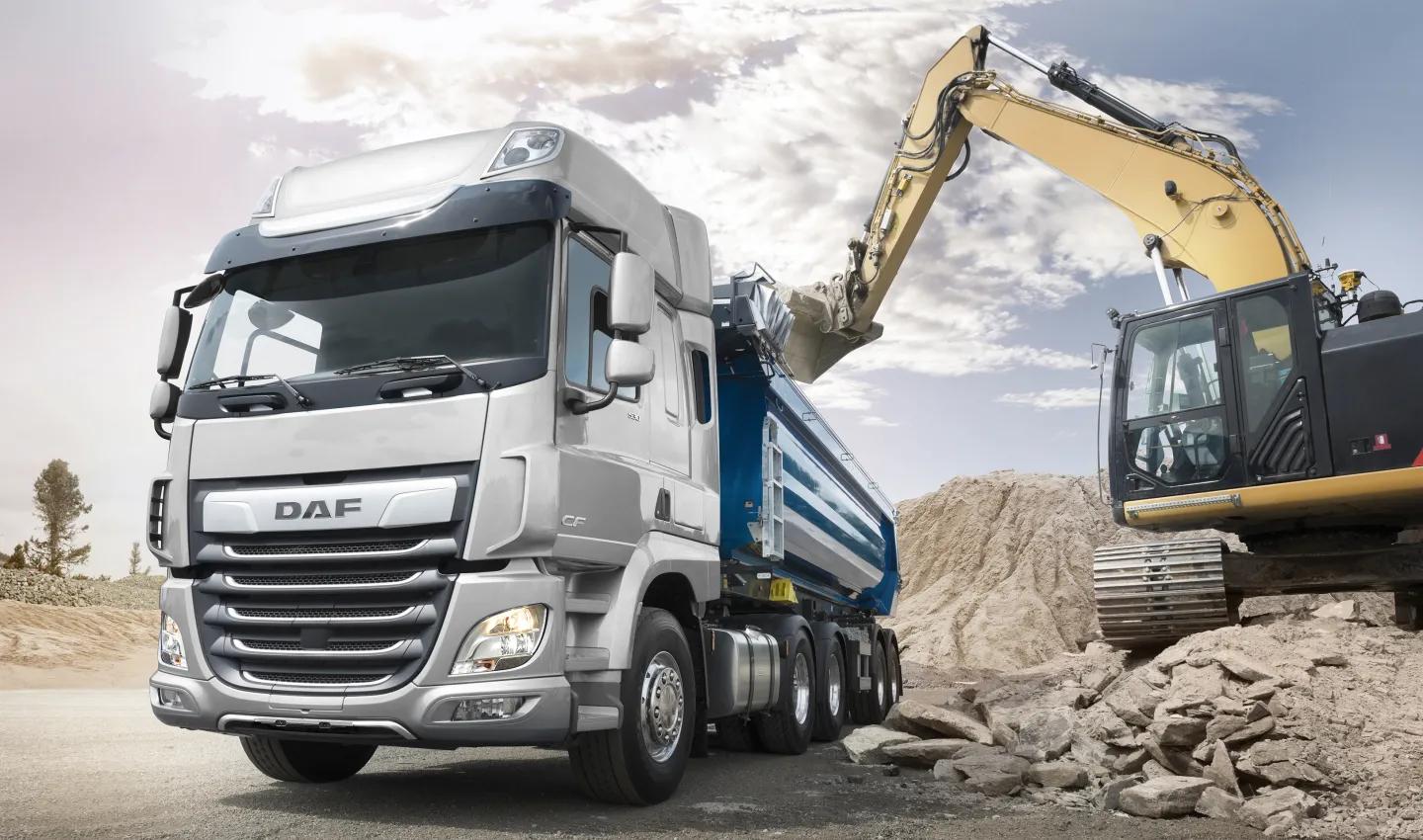
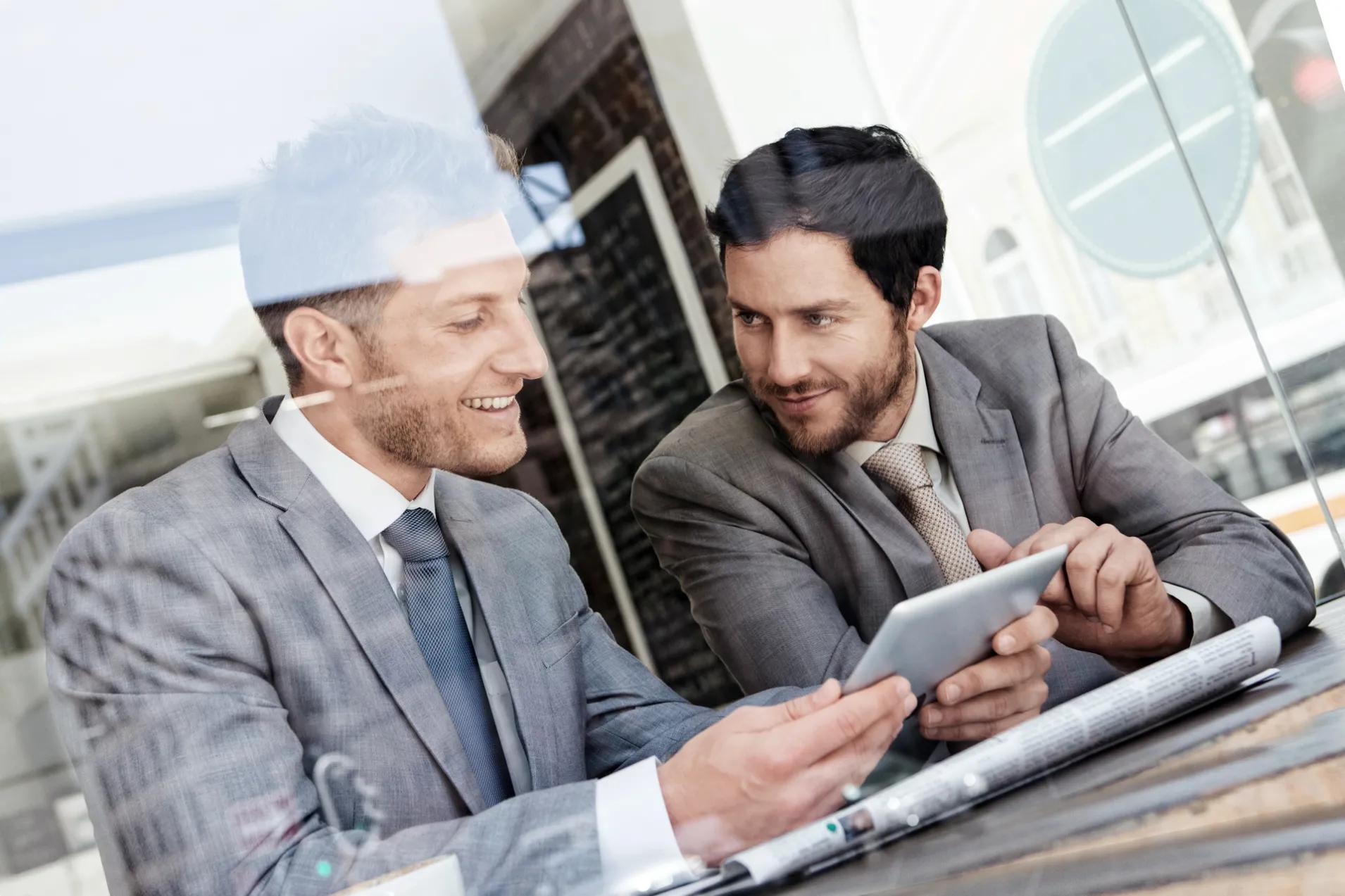
Contact for the Press
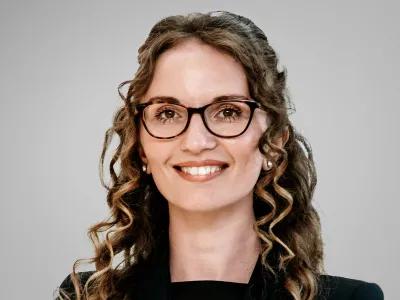
Search
No search results
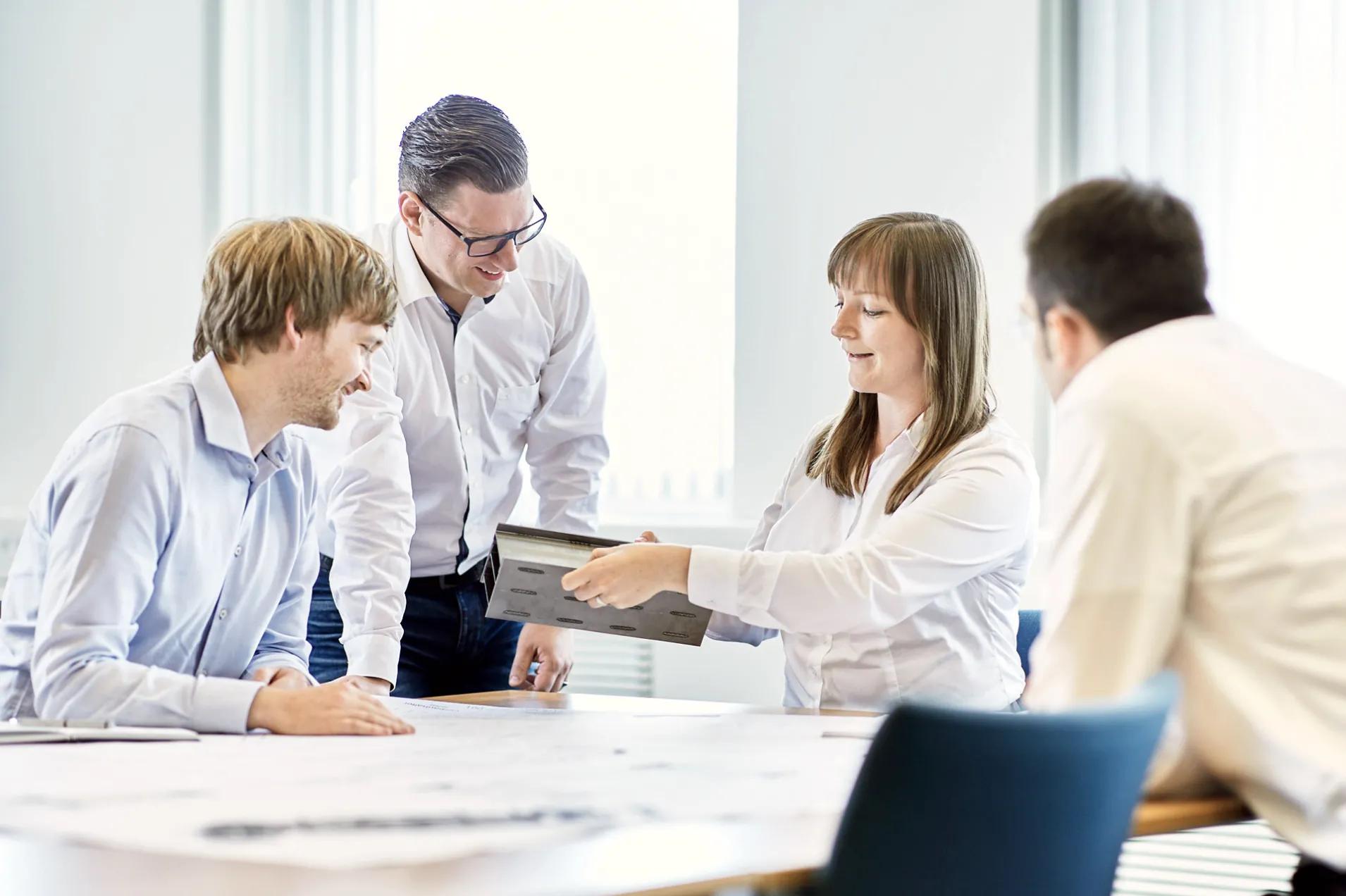
Privacy policy
Thank you for your interest in HÖRMANN Automotive GmbH. Data protection is of a particularly high priority for the company.
You can use the website without providing any personal data. If a data subject wishes to make use of our services via the website, it may be necessary to process personal data. If the processing of personal data is necessary and there is no legal basis for such processing, we always obtain the consent of the data subject.
The processing of personal data (e.g. name, address, e-mail address or telephone number of a data subject) is always carried out in accordance with the General Data Protection Regulation (GDPR) and in compliance with the country-specific data protection regulations applicable to us, in particular the Federal Data Protection Act.
With the following data protection declaration, we would like to inform the public about the type, scope and purpose of the personal data collected, used and processed by us. This privacy policy also informs data subjects about their rights.
As the controller, we have implemented numerous technical and organizational measures to ensure the most complete protection of personal data processed through the website.
Data transmissions over the Internet can, however, generally contain security gaps. It is therefore not possible to guarantee one hundred percent protection. Therefore, any data subject may, of course, also provide the company with personal data by alternative means, e.g. by telephone.
1. Definitions
This data protection declaration is based on the terms used by the European legislator for the adoption of the GDPR. The privacy policy should be both easy to read and easy to understand for everyone. To ensure this, the terms used are explained first. Among other things, these definitions are used in this privacy policy:
- "personal data" means any information relating to an identified or identifiable natural person (hereinafter "data subject"); an identifiable natural person is one who can be identified, directly or indirectly, in particular by reference to an identifier such as a name, an identification number, location data, an online identifier or to one or more factors specific to the physical, physiological, genetic, mental, economic, cultural or social identity of that natural person;
- "data subject" means any identified or identifiable natural person whose personal data are processed by the controller.
- "processing" means any operation or set of operations which is performed on personal data or on sets of personal data, whether or not by automated means, such as collection, recording, organization, structuring, storage, adaptation or alteration, retrieval, consultation, use, disclosure by transmission, dissemination or otherwise making available, alignment or combination, restriction, erasure or destruction;
- "restriction of processing" means the marking of stored personal data with the aim of limiting their processing in the future;
- "profiling" means any form of automated processing of personal data consisting of the use of personal data to evaluate certain personal aspects relating to a natural person, in particular to analyze or predict aspects concerning that natural person's performance at work, economic situation, health, personal preferences, interests, reliability, behavior, location or movements;
- "controller" means the natural or legal person, public authority, agency or other body which, alone or jointly with others, determines the purposes and means of the processing of personal data; where the purposes and means of such processing are determined by Union or Member State law, the controller or the specific criteria for its nomination may be provided for by Union or Member State law;
- "recipient" means a natural or legal person, public authority, agency or other body to whom personal data are disclosed, whether or not that person is a third party. However, public authorities which may receive personal data in the framework of a particular inquiry in accordance with Union or Member State law shall not be regarded as recipients; the processing of those data by those public authorities shall be in compliance with the applicable data protection rules according to the purposes of the processing;
- "third party" means a natural or legal person, public authority, agency or body other than the data subject, controller, processor and persons who, under the direct authority of the controller or processor, are authorized to process personal data;
- "Consent" of the data subject means any freely given, specific, informed and unambiguous indication of the data subject's wishes by which he or she, by a statement or by a clear affirmative action, signifies agreement to the processing of personal data relating to him or her.
2. name and contact details of the controller
This data protection information applies to data processing by the controller:
HÖRMANN Automotive GmbH, represented by the management: Dr.- IngMichael Radke, and this in turn represented by info@hoermann-gruppe.com or T +49 8091 56 30-0.
3. Contact details of the data protection officer:
Mr. Prof. Dr. Thorsten B. Behling
BUSE Rechtsanwälte Steuerberater
Partnerschaftsgesellschaft mbB
Berliner Allee 41
40212 Düsseldorf
T + 49 (0) 211 388 000
M +49 (0) 179 4922302
behling@buse.de
https://wwww.buse.de
Any data subject can contact the data protection officer directly at any time with any questions or suggestions regarding data protection.
4. Erasure and blocking of personal data
We process and store personal data of the data subject only for the period necessary to achieve the purpose of storage or if this is provided for by the applicable laws to which the controller is subject.
If the storage purpose no longer applies or if a legally prescribed storage period expires, the personal data is routinely blocked or erased in accordance with the statutory provisions.
5. Collection and storage of personal data and the nature and purpose of their use
a) when visiting the website
You can use this website without disclosing your identity. When you access the website, the browser used on your device automatically sends information to the website server. This information is temporarily stored in a so-called log file. The following information is collected without any action on your part and stored until it is automatically deleted:
- IP address of the requesting computer,
- date and time of access,
- name and URL of the file accessed,
- the website from which the access was made (referrer URL),
- the browser used and, if applicable, the operating system of your computer and the name of your access provider.
The company processes the aforementioned data for the following purposes:
- to ensure a smooth connection to the website,
- to ensure convenient use of the website,
- to evaluate system security and stability and
- for other administrative purposes.
The legal basis for data processing is Art. 6 para. 1 sentence 1 lit. f GDPR. The company's legitimate interest follows from the data collection purposes listed above. Under no circumstances do we use the data collected for the purpose of drawing conclusions about your person. The data will be deleted after 14 days at the latest.
We also use cookies and analysis services when you visit the website. You can find more detailed explanations on this in sections 9 and 11 of this privacy policy.
b) When using the contact form or contacting us by email
If you have any questions, we offer you the opportunity to contact the company using a form provided on the website or by email. It is necessary to provide a valid e-mail address so that we know who sent the request and can respond to it. Further information can be provided voluntarily. You are free to decide whether you wish to enter this data in the contact form or in the email.
The data entered will be processed to deal with your inquiry. The data will be deleted immediately after your request has been processed, provided there are no statutory retention periods.
The legal basis for data processing is, if the request is necessary for the performance of a contract or for pre-contractual measures, Art. 6 para. 1 sentence 1 lit. b GDPR and, in the case of statutory retention requirements, Art. 6 para. 1 sentence 1 lit. c GDPR, otherwise the legitimate interests, Art. 6 para. 1 sentence 1 lit. f GDPR. We also have a legitimate interest in processing your inquiries that are not of a pre-contractual or contractual nature in order to offer you the best possible service.
The data will be processed exclusively for the purpose of responding to your inquiry and stored for the duration of the statutory retention obligation (6 years in accordance with Section 257 (1) No. 2, (4) HGB), provided that these are commercial letters. Otherwise, the data will be deleted immediately after your request has been answered.
6. Further information on the legal basis for processing
Art. 6 I lit. a GDPR serves as the legal basis for processing operations for which consent must be obtained for a specific processing purpose. If the processing of personal data is necessary for the performance of a contract to which the data subject is party, the processing is based on Art. 6 I lit. b GDPR. The same applies to processing operations that are necessary for the performance of pre-contractual measures, for example in cases of inquiries about services and products. If we are subject to a legal obligation that requires the processing of personal data, the processing is based on Art. 6 I lit. c GDPR. In rare cases, the processing of personal data may become necessary in order to protect the vital interests of the data subject or another natural person. In this case, the processing is based on Art. 6 I lit. d GDPR. Furthermore, processing operations could be based on Art. 6 I lit. f GDPR. Processing operations that are not covered by any of the aforementioned legal bases are based on this legal basis if the processing is necessary to safeguard a legitimate interest of us or a third party, provided that the interests, fundamental rights and freedoms of the data subject do not prevail. Such processing operations are permitted in particular because they have been specifically mentioned by the European legislator (see recital 47 sentence 2 GDPR).
7. Consideration of legitimate interests
If the processing of personal data is based on Article 6 I lit. f GDPR, our legitimate interest is the performance and fulfillment of our business activities for the benefit of our employees and shareholders.
8. Use of cookies
We use cookies on the website. These are small files that your browser automatically creates and that are stored on your end device (laptop, tablet, smartphone, etc.) when you visit the company's website. Cookies do not cause any damage to your end device and do not contain any viruses, Trojans or other malware.
In the cookie, information is stored that results in each case in connection with the specific end device used. However, this does not mean that the company gains direct knowledge of your identity as a result.
The use of cookies serves on the one hand to make the use of the offer more pleasant for you. For example, we use so-called session cookies, which recognize when you have already visited individual pages of the website. They are automatically deleted after you leave the website.
In addition, we also use temporary cookies to optimize user-friendliness, which are stored on your device for a specified period of time. If you visit our website again to make use of services, it is automatically recognized that you have already been there and which entries and settings you have made so that you do not have to enter them again.
On the other hand, we use cookies to statistically record the use of the website and to evaluate this data for the purpose of optimizing the offer for you (see section 7). These cookies make it possible to automatically recognize that you have already visited the website when you visit it again. These cookies are automatically deleted after a defined period of time, at the latest after 6 months. You can also delete the cookies earlier via your browser. Please refer to the help pages of your browser.
The data processed by cookies is required for the aforementioned purposes to safeguard the legitimate interests of us and third parties in accordance with Art. 6 para. 1 sentence 1 lit. f GDPR.
Most browsers accept cookies automatically. However, you can configure your browser so that no cookies are stored on your computer or a message always appears before a new cookie is created. However, completely deactivating cookies may mean that you cannot use all the functions of the website.
9. Analysis and tracking tools
The tracking measures listed below and used by us are carried out on the basis of Art. 6 para. 1 sentence 1 lit. f GDPR. With the tracking measures used, the company wants to ensure a needs-based design and the continuous optimization of the website. On the other hand, the company uses the tracking measures to statistically record the use of the website and to evaluate it for the purpose of optimizing the offer for you. These interests are to be regarded as legitimate within the meaning of the aforementioned provision.
The respective data processing purposes and data categories can be found in the corresponding tracking tools.
10. Google Analytics
This website uses Google Analytics, a web analytics service provided by Google LLC, 1600 Amphitheatre Parkway, Mountain View, CA 94043, USA ("Google"). Google Analytics uses "cookies", which are text files placed on your computer, to help the website analyze how users use the site. The information generated by the cookie about your use of this website is usually transferred to a Google server in the USA and stored there. Please note that on this website Google Analytics has been extended by the code "anonymizeIp" to ensure an anonymized collection of IP addresses (so-called IP masking). Your IP address is thus shortened within member states of the European Union or in other contracting states of the Agreement on the European Economic Area before being transmitted to the USA. Only in exceptional cases will the full IP address be transmitted to a Google server in the USA and truncated there. Google will use this information on behalf of the operator of this website for the purpose of evaluating your use of the website, compiling reports on website activity and providing other services relating to website activity and internet usage to the website operator. The IP address transmitted by your browser as part of Google Analytics will not be merged with other Google data. You may refuse the use of cookies by selecting the appropriate settings on your browser, however please note that if you do this you may not be able to use the full functionality of this website. You can also prevent the collection of data generated by the cookie and related to your use of the website (including your IP address) to Google and the processing of this data by Google by downloading and installing the browser plugin available at the following link (http://tools.google.com/dlpage/gaoptout?hl=de).
You can prevent Google Analytics from collecting data by clicking on the following link. An opt-out cookie will be set to prevent future collection of your data when you visit this website: Prohibit Google Analytics from tracking me
For more information on terms of use and data protection:
- http://www.google.com/analytics/terms/de.html
- https://www.google.com/intl/de/policies/privacy/partners/<7a>
- https://policies.google.com
The IP address and other personal data are only stored for the minimum period of 14 months stipulated by Google Analytics.
11. social media plug-ins
We use social plug-ins of social networks (e.g. Facebook, Twitter, Google+) on the website on the basis of Art. 6 para. 1 sentence 1 lit. f GDPR in order to make the company better known. The underlying advertising purpose is to be regarded as a legitimate interest within the meaning of the GDPR. Responsibility for data protection-compliant operation must be guaranteed by the respective provider. The integration of these plug-ins by the company is carried out using the so-called two-click method to protect visitors to the website in the best possible way.
a) YouTube
This website uses YouTube videos in the data protection-friendly 2-click version, i.e. personal data is only processed when you activate the plugin by clicking on it. YouTube plugins are plugins from YouTube LLC, 901 Cherry Ave, San Bruno, CA 94066, USA. YouTube LLC is a subsidiary of Google Inc, 1600 Amphitheatre Pkwy, Mountain View, CA 94043-1351, USA.
When the plugins are activated, information is sent to YouTube LLC and possibly Google Inc. in the USA. YouTube and Google are thus able to see that you have visited our site. If you are logged into your YouTube or Google account when the plugins are activated, YouTube and/or Google may be able to identify you directly.
We would like to point out that, as the provider of this website, we have no information about the data transmitted to YouTube and Google, the purposes of data collection or its use by Facebook. Further information about the data collected can be found in Google's privacy policy, which you can access at https://policies.google.com/privacy?hl=de.
We cannot provide any information about the storage period, as this is solely within the sphere of influence and responsibility of YouTube or Google.
b) Google Maps
This website has integrated a map from Google Maps to show you our locations. As soon as you access our website with the Google Maps map, a connection to Google servers is established and personal data may be transferred to Google LLC, 1600 Amphitheatre Parkway, Mountain View, CA 94043, USA. If you are logged into your Google account, Google may be able to identify you directly. If you do not wish this to happen, please log out of your Google account.
You can find Google's privacy policy here: https://policies.google.com/privacy?hl=de.
12. Applications
If you apply to us via our careers page or by email, your personal data will be processed for the purpose of processing your application. The legal basis is § 26 BDSG (data processing for the purpose of the employment relationship) and Art. 6 para. 1 sentence 1 lit. f) GDPR (legitimate interest). Your data will be deleted six months after your application has been rejected. We have a legitimate interest in retaining the data for a period of six months even after your application has been rejected in order to be able to defend against claims under the General Equal Treatment Act (AGG).
13. rights of data subjects
You have the right:
- to request information about your personal data processed by us in accordance with Art. 15 GDPR. In particular, you can request information about the purposes of processing, the category of personal data, the categories of recipients to whom your data has been or will be disclosed, the planned storage period, the existence of a right to rectification, erasure, restriction of processing or objection, the existence of a right to lodge a complaint, the origin of your data if it was not collected by us, as well as the existence of automated decision-making including profiling and, if applicable. in accordance with Art. 16 GDPR, you have the right to obtain from us without undue delay the rectification of inaccurate personal data concerning you or to have incomplete personal data completed,
- in accordance with Art. 17 GDPR, to demand the erasure of your personal data stored by us, unless the processing is necessary for exercising the right of freedom of expression and information, for compliance with a legal obligation, for reasons of public interest or for the establishment, exercise or defense of legal claims,
- in accordance with Art. 18 GDPR, to demand the restriction of the processing of your personal data if the accuracy of the data is contested by you, the processing is unlawful but you oppose the erasure of the data and we no longer need the data, but you require it for the establishment, exercise or defense of legal claims or you have objected to processing pursuant to Art. 21 GDPR,
- in accordance with Art. 20 GDPR, to receive your personal data that you have provided to us in a structured, commonly used and machine-readable format or to request that it be transmitted to another controller,
- in accordance with Art. 7 para. 3 GDPR, to withdraw your consent to us at any time. As a result, we may no longer continue the data processing based on this consent in the future and
- in accordance with Art. 77 GDPR to lodge a complaint with a supervisory authority. As a rule, you can contact the supervisory authority of your usual place of residence or workplace or the registered office of one of our companies. You can find an overview of the supervisory authorities here (https://www.bfdi.bund.de/DE/Infothek/Anschriften_Links/anschriften_link…); the supervisory authority generally responsible for HÖRMANN Automotive GmbH is the
Bayerisches Landesamt für Datenschutzaufsicht
Promenade 27 (Schloss)
91522 Ansbach
T +49 98153 1300
F +49 98153 5300
poststelle@lda.bayern.de
http://www.lda.bayern.de
14. Right to object
If your personal data are processed on the basis of legitimate interests pursuant to Art. 6 para. 1 sentence 1 lit. f GDPR, you have the right to object to the processing of your personal data pursuant to Art. 21 GDPR, provided that there are reasons for this arising from your particular situation or the objection is directed against direct advertising. In the latter case, you have a general right to object, which we will implement without you having to specify a particular situation.
If you wish to exercise your right of revocation or objection, simply send an email to:
datenschutz@hoermann-gruppe.com
15. Data security
We use the widely used SSL (Secure Socket Layer) method in conjunction with the highest level of encryption supported by your browser when you visit our website. As a rule, this is 256-bit encryption. If your browser does not support 256-bit encryption, the company uses 128-bit v3 technology instead. You can tell whether an individual page of our website is transmitted in encrypted form by the closed display of the key or lock symbol in the lower status bar of your browser.
We also use suitable technical and organizational security measures to protect your data against accidental or intentional manipulation, partial or complete loss, destruction or unauthorized access by third parties. These security measures are continuously improved in line with technological developments.
16. Updating and amending this privacy policy
This privacy policy is currently valid and was last updated in April 2025.
It may become necessary to amend this privacy policy as a result of the further development of our website and offers on it or due to changes in legal or official requirements.