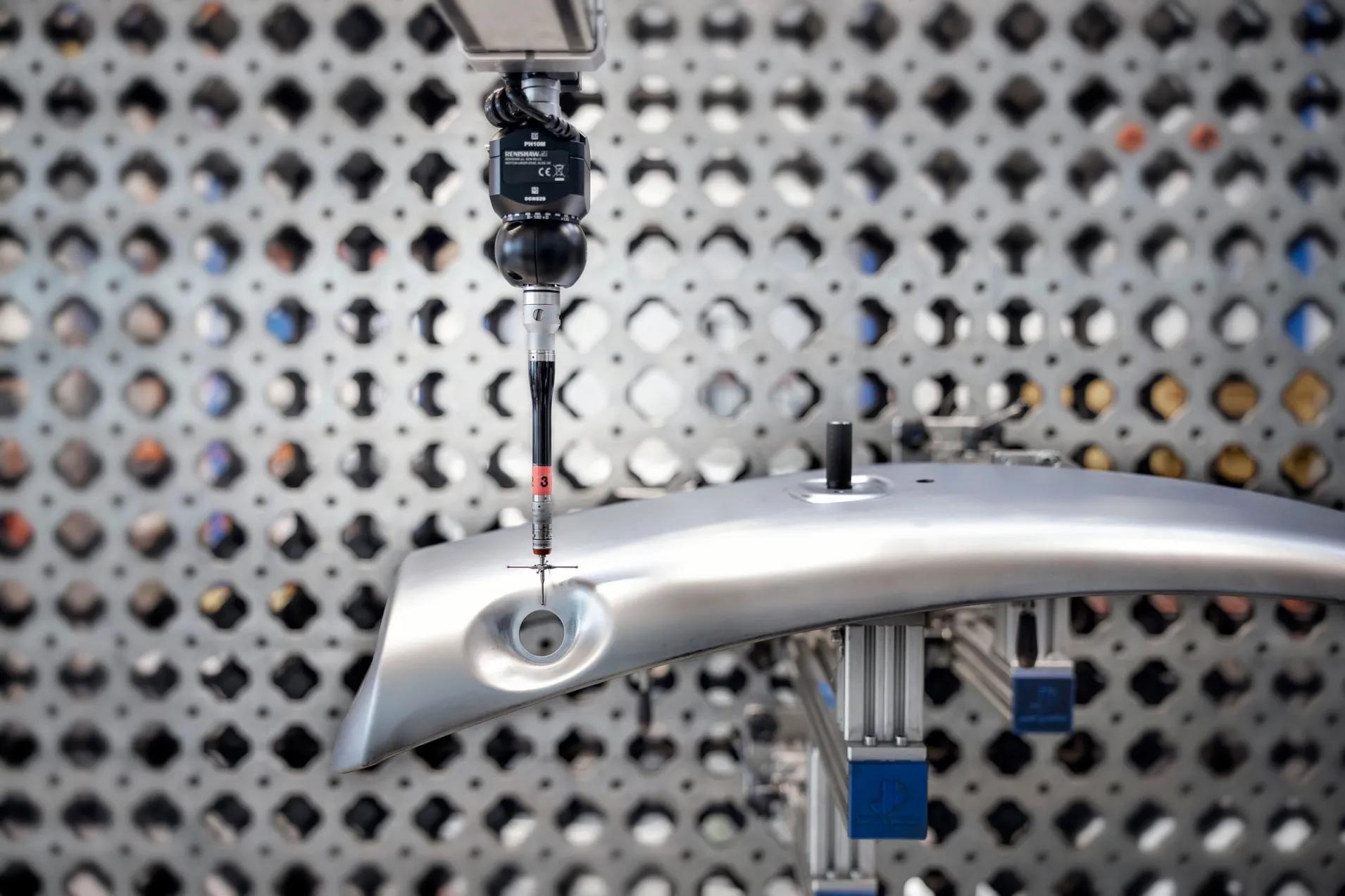
Procurement
Sustainable and responsible action is a central element of our self-image and our corporate strategy at HÖRMANN Automotive GmbH. HÖRMANN Automotive and its affiliated companies have implemented guidelines that are intended to provide employees with binding guidance for all actions.
Our suppliers make a significant contribution to our success. Therefore, it is our aim to work with them to shape the development of our products and services in a sustainable and successful manner in the future. The requirements and principles for working with suppliers are written in our code of conduct.
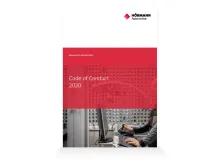
Code of Conduct
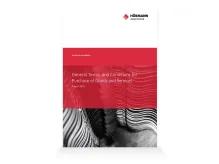
General Purchase Conditions
News reports 2019
2019
News reports 2018
2018
News reports 2020
2020
Partner Product
Ground-breaking auxiliary heater and stationary heater from our partner ReformTech
With the coming into force of the new Euro 6c/7 emission standard, the European automotive market is facing profound changes: To date, solely the emission levels were taken into account in the emission measurement of motor vehicles, without the share of emissions produced by other components. With the new standard, now the entire vehicle will be included in the emission measurement, and thus also the auxiliary heater, a component that compensates for the missing heat output from highly efficient engines. It is required to heat up the vehicle interior more quickly and to heat the exhaust gases so that the catalytic converter can work efficiently. However, conventional auxiliary heaters produce very high emissions and have intensive particulate matter emissions. With the new emission standard, automotive manufacturers must now act and use new, emission-reducing technologies.
ReformTech, a Swedish research and development company, was founded by a group of leading engineers from the automotive industry. They had recognised the potential, developed a suitable technology, invented a product and patented it. This technology is a global game-changer in terms of achieving sustainable combustion processes: The auxiliary heater developed by ReformTech achieves combustion that is up to 90% more efficient than conventional models and creates virtually no emissions. The market launch for the new auxiliary heater took place in 2015.
HÖRMANN as a partner of ReformTech
Together with ReformTech, we are developing this new product technology with the focus on industrialisation and a production- and assembly-compatible design. Furthermore, HÖRMANN Automotive in Wackersdorf will take over the production of the new auxiliary heater generation.
Advantages at a glance:
- Greater efficiency in comparison to previous auxiliary heaters (+ 90%)
- Virtually no emissions: No particulate, ultra-low emissions of CO, NOx and CO2.
- Compatibility with all fossil fuels and renewable fuels
- Controllable direction of thermal radiation
- Competitive product costs
- Extremely resistant and highly reliable
- For the OEMs: Significant installation space advantages
Scopes of application and usage:
- Preheating and auxiliary heating of engines, for the vehicle interior and the exhaust system
- Stationary heating, water heating for camper vans, etc.
- For the preheating of the battery and for thermal management in the case of cold starts and in the case of permanently low temperatures
- Key component for the overall thermal management to fulfil current and future emission regulations
Are you interested in this product?
You can find the contact details for HÖRMANN Automotive in Wackersdorf here.
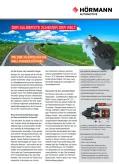
The cleanest auxiliary heater in the world! (in German)
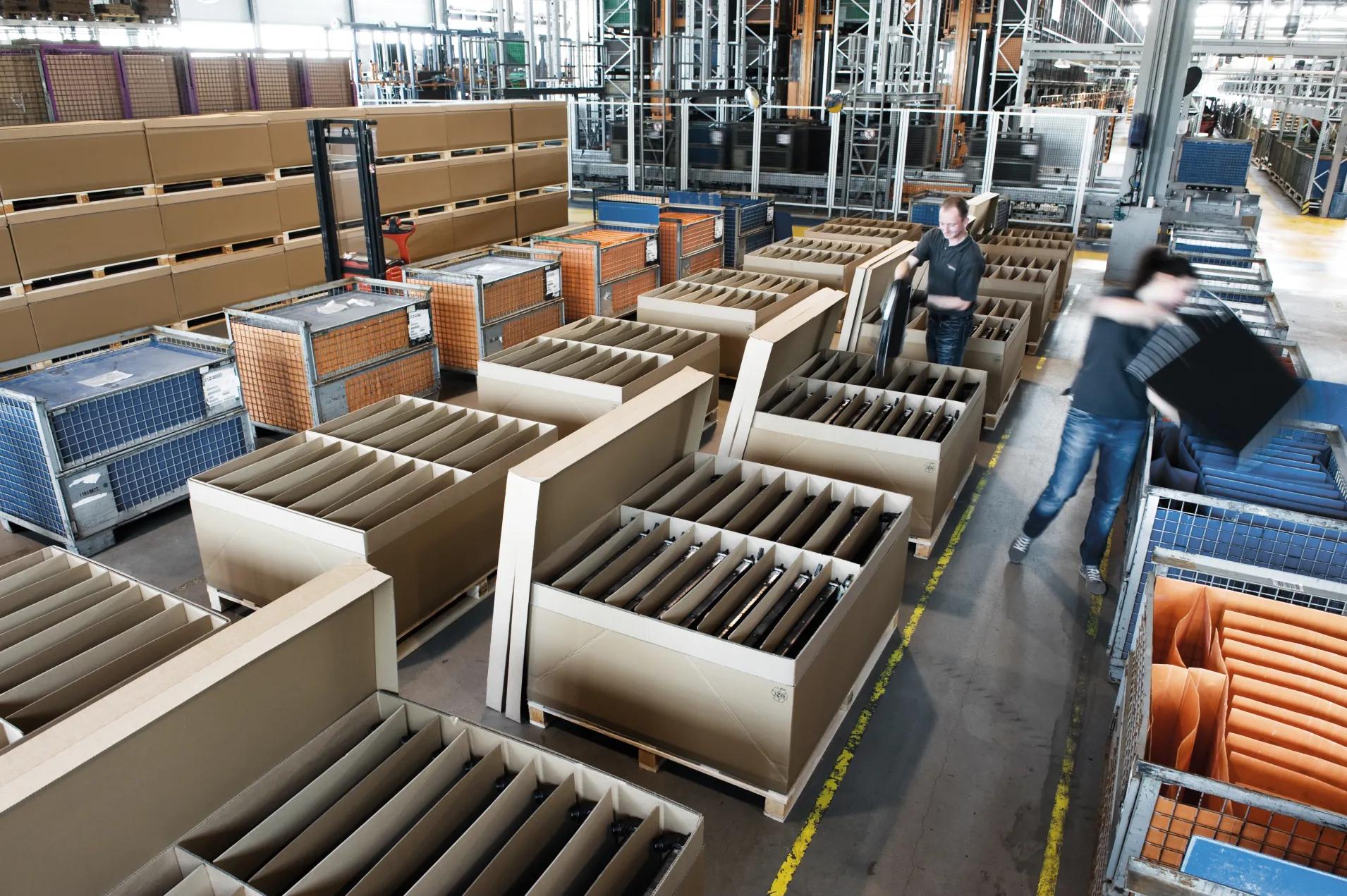
Packaging of Components for the Replacement Part and CKD Markets
We assume overall responsibility for the packaging and delivery of replacement parts, CKD components and kit solutions. This includes the packaging planning, coordination of the supply chain and on-time delivery. Thanks to intelligent packaging design, we create ideal cardboard boxes and containers to guarantee cycle times that are as fast as possible and high transport protection. The packaging of parts takes place in an order-related manner and in accordance with the highest quality standards. If desired, the replacement parts are provided together with operating instructions, add-on parts and small parts for installation at the dealer and delivered as a kit. The CKD parts and pre-assembled units for the foreign markets are packaged in special overseas containers and loaded in containers.
We deliver as per your desired delivery instructions via truck, railway train, maritime freight, air freight or, if desired, also directly to the dealers. We also complete the customs clearing of the goods for you for foreign shipments. Our partners for the local added value abroad are located in the USA, China, South Africa and Egypt.
Thanks to our in-house software, which calculates the optimal container utilisation for each delivery, and our many years of cooperation with our global network of innovative logistics partners, we can offer you this comprehensive complete package at favourable conditions.
Our range of services covers the following:
- Process planning
- Investment for the required systems and tools
- Packaging planning and development
- Procurement of components (alternatively provided by the customer) and packaging materials
- MRP of components and packaging materials
- Transport coordination for all incoming goods
- Calculation of optimal container utilisation
- Packaging of the offer scope in replacement part or CKD packaging
- Monitoring of supply chain, supplier management, supplier development
- Change management for components
- Customs declaration and clearing
- Delivery of goods to suit customer requests, if necessary via partners to increase the local content level
Are you interested in this product?
You can find the contact details for HÖRMANN Automotive in Wackersdorf here.
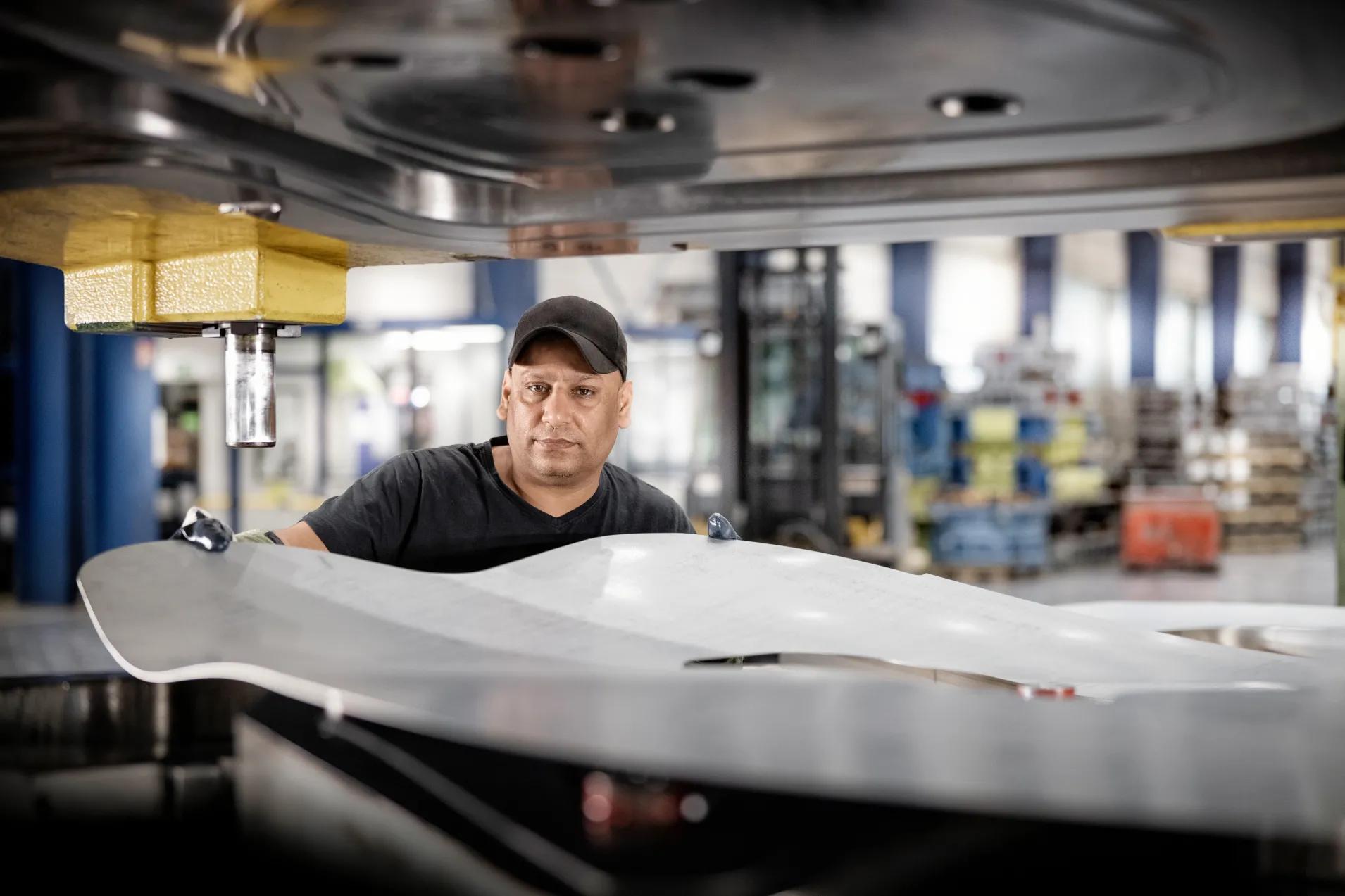
Ready-To-Install Modules
Already today, we supply one of our customers with painted and pre-assembled side trim parts for harvesting machines that are delivered just-in-time to the main assembly line. In the future, this service is to be intensified and optimised. The most important success factors for this are customer proximity, communication and high logistical competence. We have made these characteristics our principles, and our employees stand for professional cooperation with our customers on a partnership basis.
Our range of services covers the following:
- Development and planning
- Prototyping
- Welding, riveting, adhesive bonding, edging, screwdriving
- Coating
- Final assembly
Are you interested in this product?
You can find the contact details for HÖRMANN Automotive in St. Wendel here.