Legal Notice
Information as per section 5 DDG
HÖRMANN Automotive GmbH
Hauptstr. 45-47
85614 Kirchseeon
Deutschland
T +49 8091 5630-0
F +49 8091 5630-195
info@hoermann-automotive.com
Represented by the management: Dr.-Ing. Michael Radke, Christian Petters, Dr. Jürgen Lechler
Sole power of attorney: Johann Schmid-Davis
- Company domicile: Kirchseeon
- Registry court: Munich Local Court
- Registry number: HRB 163 762
- VAT identification number: DE 258 620 710
HÖRMANN Automotive Gustavsburg GmbH
Ginsheimer Str. 2
65462 Ginsheim-Gustavsburg
Germany
T +49 6134 588-0
F +49 6134 588-501
info.gustavsburg@hoermann-automotive.com
Represented by the management: Dr. Jürgen Lechler, Stefan Kuhn, Dr. Wolfram Schmitt, Andreas Regel
Chairman of the Supervisory Board: Dr.-Ing. Michael Radke
- Company domicile: Gustavsburg
- Registry court: Darmstadt Local Court
- Registry number: HRB 860 75
- VAT identification number: DE 254 992 655
HÖRMANN Automotive Saarbrücken GmbH
Am Stahlhammer 65
66121 Saarbrücken
Germany
T +49 681 81908-0
F +49 681 81908-19
info.saarbruecken@hoermann-automotive.com
Represented by the management: Dr.-Ing. Michael Radke, Dr. Roland Dittmann, Dipl-Ing. Martin Klein
Sole power of attorney: Rolf Klein, Jörg Moses
- Company domicile: Saarbrücken
- Registry court: Saarbrücken Local Court
- Registry number: HRB 138 27
- VAT identification number: DE 813 727 861
HÖRMANN Automotive Slovakia s.r.o.
Partizanska. 73
975 01 Banovce nad Bebravou
Slovakia
T +421 38 321 38 00
F +421 38 321 38 99
info.hask@hoermann-automotive.com
Represented by the management: Fabian Selder, Patrick Bräuer
Joint power of attorney: Markus Busch
entered in the commercial register of Trenčín District Court, Dept. Sro.
- IČO/commercial register number: 33553/R
- IČ DPH/VAT no.: SK 212 034 0673
- ID no.: 50 481 151
HÖRMANN Automotive St. Wendel GmbH
Essener Str. 3
66606 St. Wendel
Germany
T +49 6851 8005-300
F +49 6851 8005-370
info.st.wendel@hoermann-automotive.com
Represented by the management: Dr.-Ing. Michael Radke, Dr. Roland Dittmann, Dipl-Ing. Martin Klein
Sole power of attorney: Jörg Straß
- Company domicile: St. Wendel
- Registry court: Saarbrücken Local Court
- Registry number: HRB 156 61
- VAT identification number: DE 137 214 419
HÖRMANN Gruppe; HÖRMANN Automotive; Getty Images (für HÖRMANN Gruppe); John Deere; MAN; DAF; Atlas; Liebherr; Demag; New Holland; RSP; Wirelane; ZF Friedrichshafen
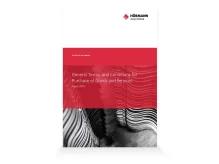
General Purchase Conditions
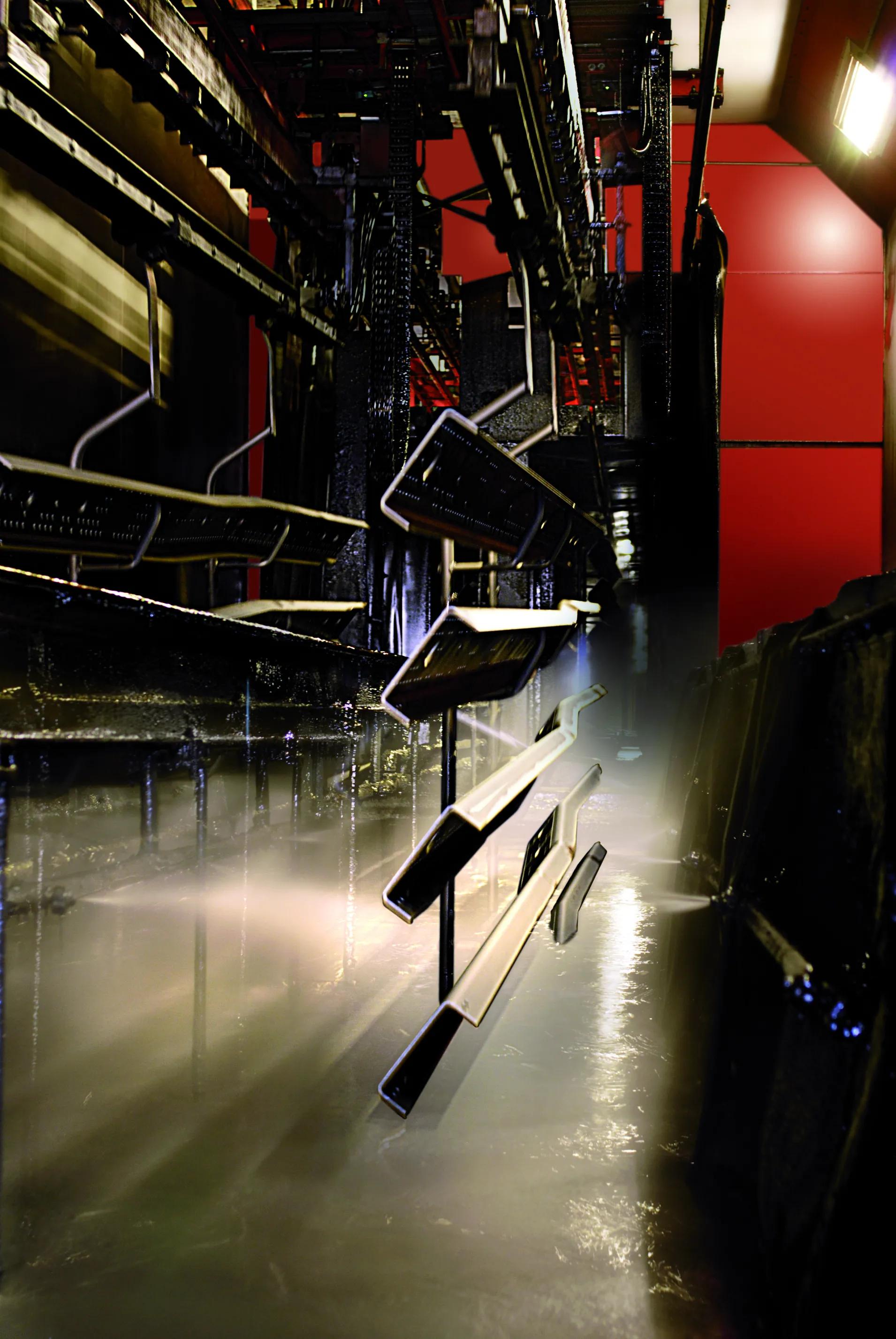
Production and Assembly
The focus of our work is always the product requirements of our customers. We take up the challenge on a daily basis to precisely identify these requirements and create ideal technological solutions.
We make your production processes leaner by means of a production- and assembly-compatible product design. During product development, we support you every step of the way – from samples up to series production maturity of your product. Our strength lies in achieving a production- and assembly-compatible design of customer-specific products and in professionally implementing the corresponding application development.
We can model the production processes in advance in 3D. In this connection, we check and optimise the error-proneness of a process already during the simultaneous product development – we thus create Poka-Yoke system solutions for the products as well as a lean and robust production process. We also have all current interfaces to the digital OEM world.
Together with you, we thus develop a concept step by step with which we continuously improve the products and processes and with which you meet the desired targets in terms of time, quality and cost. You can draw on a broad pool of services with many years of in-depth expertise: We take into account the wide variety of available production methods and realise an optimised value stream. In addition, we always include the following steps in the process chain. You benefit from a consistently lean production process that results in target-oriented resource optimisation.
We are there to lend a helping hand with our production expertise when it comes to the production-related realization of your ideas: This involves the feasibility validation, production-related product optimisation, tool design and implementation, prototyping and transfer to series production. A consistent CAE chain supports simultaneous engineering and ensures close and coordinated project execution.
Our assembly expertise ranges from assuming the overall responsibility to supply chain management to responsibility for quality control. We are happy to take over responsibility for the assembly of complex systems and modules and their demand-based delivery in the desired takt time (e.g. JIT and JIS). We thus accompany you as a partner every step of the way from the idea to production to the finished product.
Forming
Sheet-metal working
We process fine sheets in accordance with EN 10143 and EN 10131 to a max. thickness of 3 mm, as well as thick plates with the material grade of QStE 700 TM to a max. thickness of 15 mm. Delivery takes place via truck or railway wagon, the unit weights of the coils can be up to 30 tonnes.
The systems used at our company for material preparation include the following:
- Uncoiling and cutting-to-length line up to max. 1,550 mm wide with precision straightening system, 12 m guillotine shears, magnetic lifting devices, CNC die-cutting system and roller conveyors for thick plates
- Coil line with max. blank size 2,050 x 3,700 mm for thin sheets
- Blank cutting centre with 2 lasers of 4.4 kW each, combined plasma cutting and CNC die-cutting, brushing/shot-blast systems and slitting shears
Press systems
In the Fine Sheet area, production takes place on two fully automated press lines with max. blank dimensions of 2,400 x 4,000 mm and max. 6 tools. The following are available in the Thick Plate area: Two press lines from 4,000 to 12,000 kN, one multiple-die press with 30,000 kN, a bending machine with 4,000 kN and 4,000 mm long and two presses with 50,000 kN.
Roll forming
The following systems are available in a coordinated production system for the production method known as roll forming:
- Integrated roll former with reel and straightening device
- CNC die-cutting systems
- Flame cutting robots for contour cuts
- Bending systems
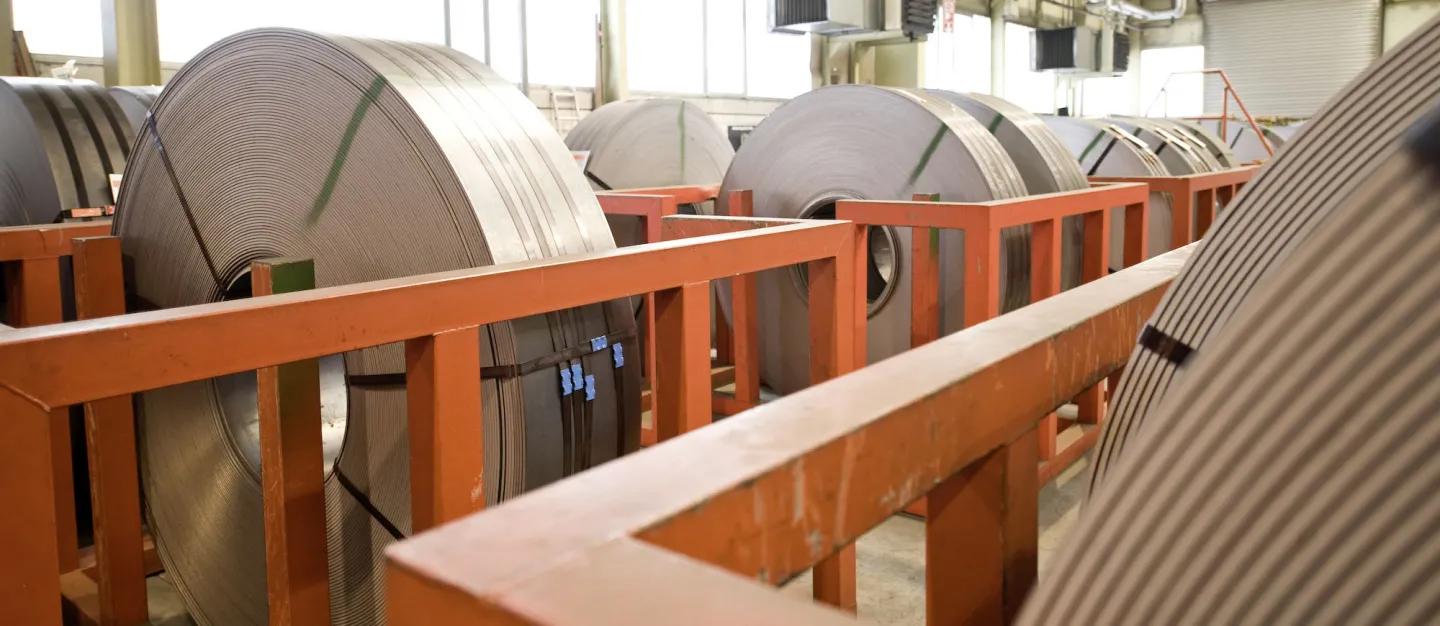
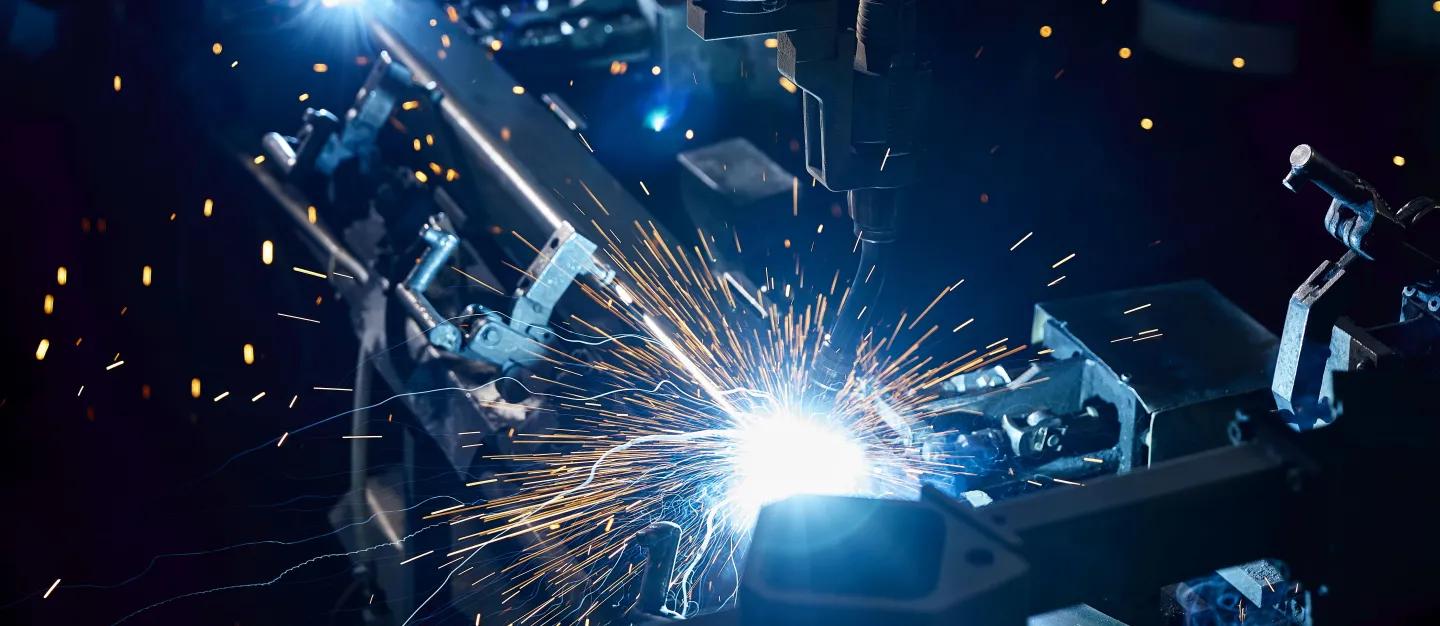
Joining
Welding
Sustainable and economic production as well as state-of-the-art design principles for safer, more comfortable and more environmentally friendly vehicles necessitate continuous innovations in welding technology. For this reason, a total of 15 state-of-the-art welding robots with rotary and tilting tables (MAG welding) are used at our locations in Gustavsburg and Banovce (Slovakia), for example. The robots are programmed in a project-related manner by our specialists. Spot-welding tongs and projection welding units with a nominal output of 400 kVA are available at table-top workstations. Workpieces with a max. length of 3,000 mm, a max. width of 1,600 mm and a max. weight of 500 kg are processed.
Adhesive bonding
The use of adhesives in current and future vehicle manufacturing is indispensable. It is the only way to join state-of-the-art structural elements to form lightweight sandwich constructions. We have the expertise and plant technology to produce sophisticated bonded joints in perfect quality.
Riveting
For positive connections with high- and ultrahigh-strength steels, we use hydraulic riveting systems for cold riveting using rivets with a diameter of 10 to 14 mm.
Welded Assemblies
The trend in recent years has shown that our customers are increasingly interested in purchasing pre-welded assemblies instead of just single parts. As a result, we deliver both manually and robot-welded assemblies, such as outer skin panels for harvesting machines or steel bumpers for trucks. Today we also already deliver the basic pressed parts for the production of cabs for harvesting machines and tractors.
Our range of services covers the following:
- Planning and industrialisation
- Prototyping
- Welding, riveting, adhesive bonding, edging
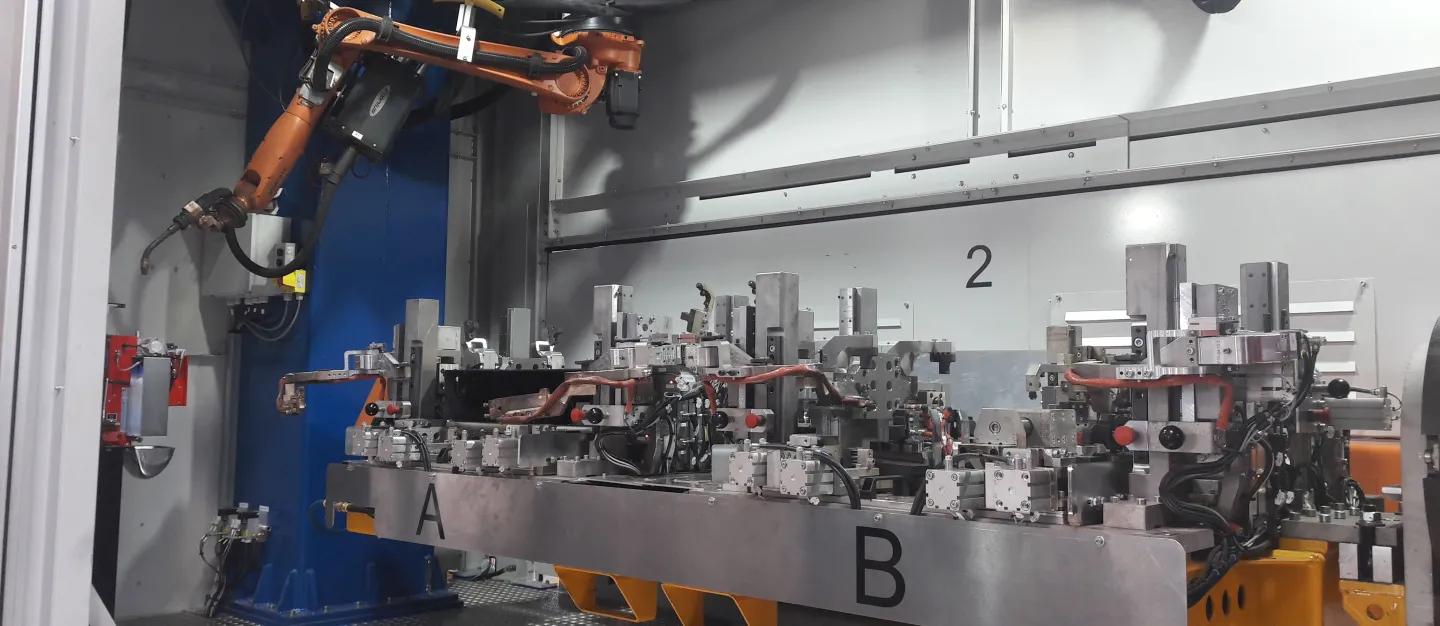

Assembly Production
In the Assembly Production area, we cover the entire value-added chain for mechanical and mechatronic assemblies: Our services comprise all joining and machining production processes, final assembly, packaging and delivery. This also includes all upstream and downstream steps in the process chain and their control, such as procurement, MRP, control of the value chain and transport. Production is realized on largely automated and material-flow-controlled systems. Our expertise comprises all joining methods and machining such as welding, pressing, adhesive bonding, lathing, milling, screwdriving, riveting, bracketing, clipping, clinching etc. Thanks to this comprehensive technology portfolio with all established processing methods, we also meet complex requirements, such as assemblies with mechanical, electronic, pneumatic or hydraulic component parts.
3D measuring machines and optical measuring systems allow us to make high-precision measurements. In addition, we can carry out microsection investigations and microscopical analyses in our laboratory. Together with certified production processes, we thus guarantee you optimal quality results. All relevant component parts can be traced in a data-based manner. Complete documentation of the individual process steps is thus guaranteed. We take on medium to large order volumes with a series-production character and also serve niche markets with these order sizes. Each production and assembly process is set up and designed in a customised manner. Processes can be tested and modelled in advance as a 3D model. Furthermore, we have in-depth development expertise and can support you in optimising your cost structure by means of a production- and assembly-compatible product design.
Our range of services covers the following:
- Supplier selection and sourcing
- Product realisation process and project management
- Production, assembly, packaging and transport
- MRP and procurement
- Sampling
- Change management
- Complaint processing
- Supplier management and development
- Transport coordination for inbound and outbound
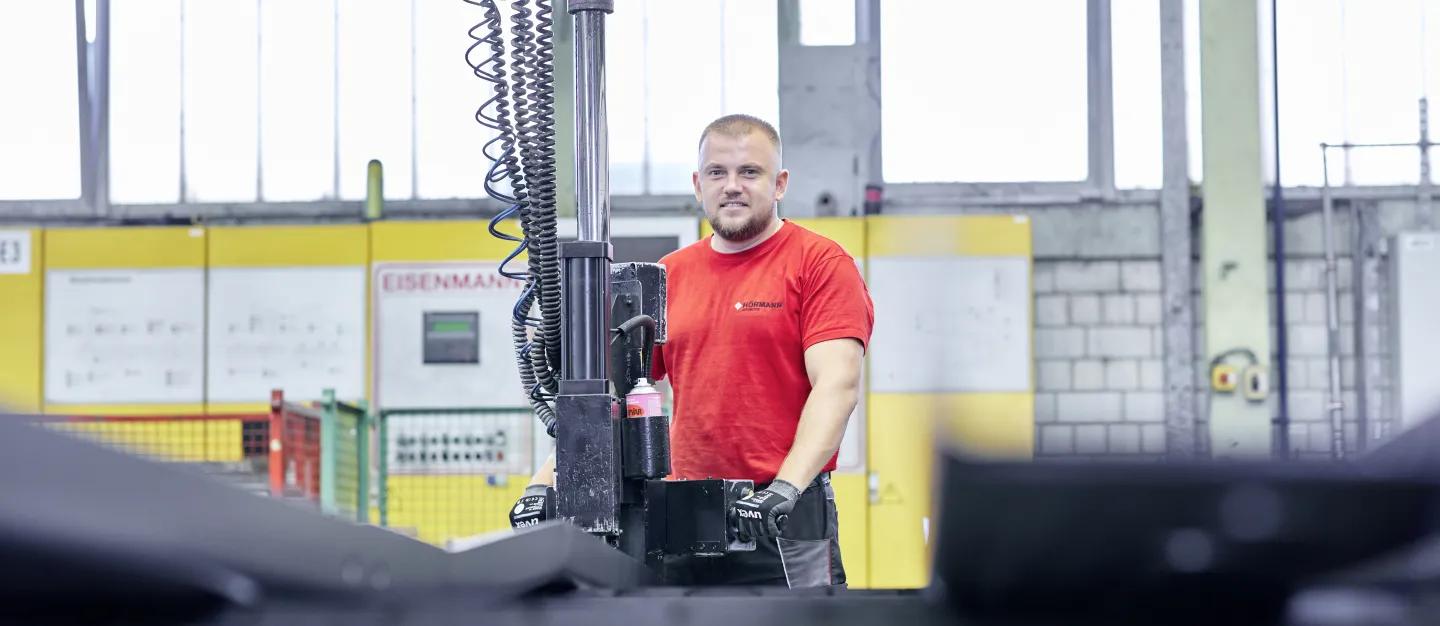
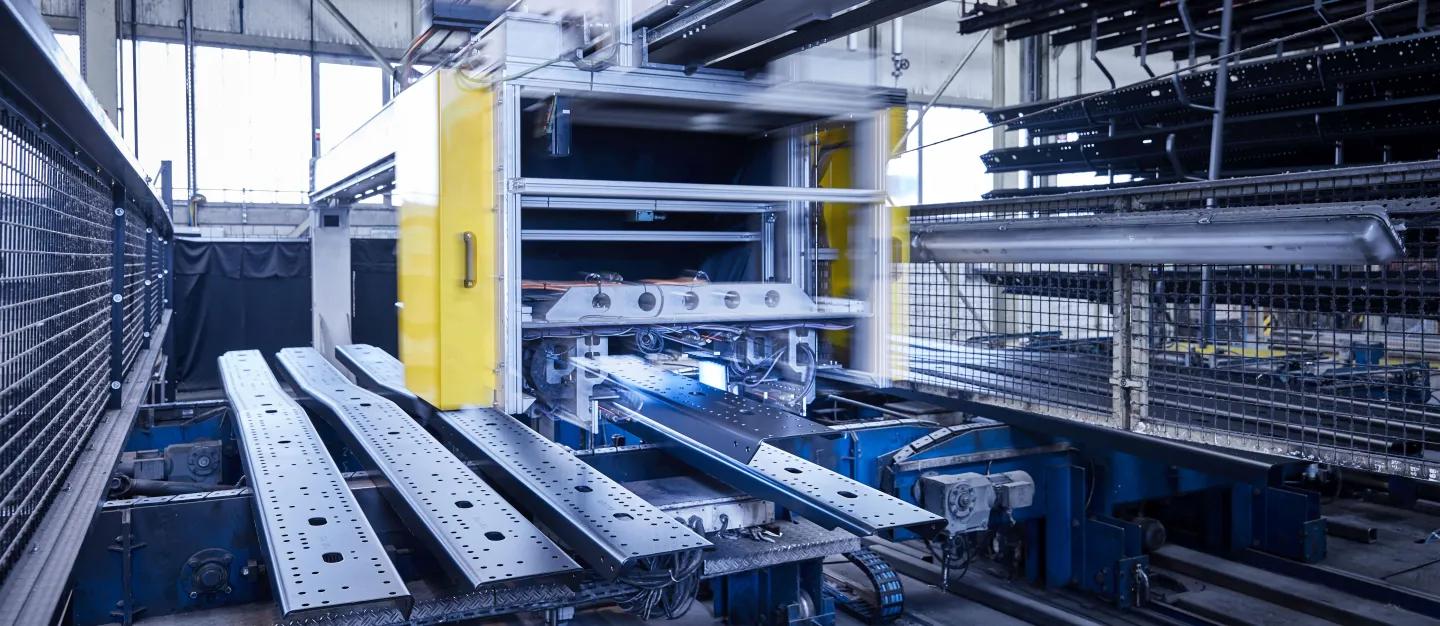
Coating
Cathodic dip painting
To ensure the quality and durability of our products, we have implemented customized surface technologies such as cathodic dip painting. Our systems are designed for coating complex workpieces with different layer thicknesses.
Topcoat
The topcoat film of a chassis is what gives it its colour; this coating also has weather- and chemical-resistant properties. At HÖRMANN Automotive, topcoats with liquid paint material are applied in automated application zones.
|
Small parts |
Long parts |
Max. usable size of workpiece carrier: |
W = 1,000 mm D = 1,200 mm |
L = 11,800 mm W = 400 mm D = 2,400 mm |
Suspension load |
Max. 400 kg per suspension |
Max. 1,600 kg per suspension |
Powder coating
As an alternative to wet painting, the more cost-effective powder coating process can also fully meet the quality requirements of our customers in many applications. Our systems preserve complex parts made of steel or aluminum automatically or manually. Whether single or multi-layer, but also in the Dublex process, customers receive first-class quality, even as contract coaters.
Max. usable size of the product carrier: L = 2,700mm x H = 2,000mm x W = 1,300mm
Max. Towing load: 500kg per trolley
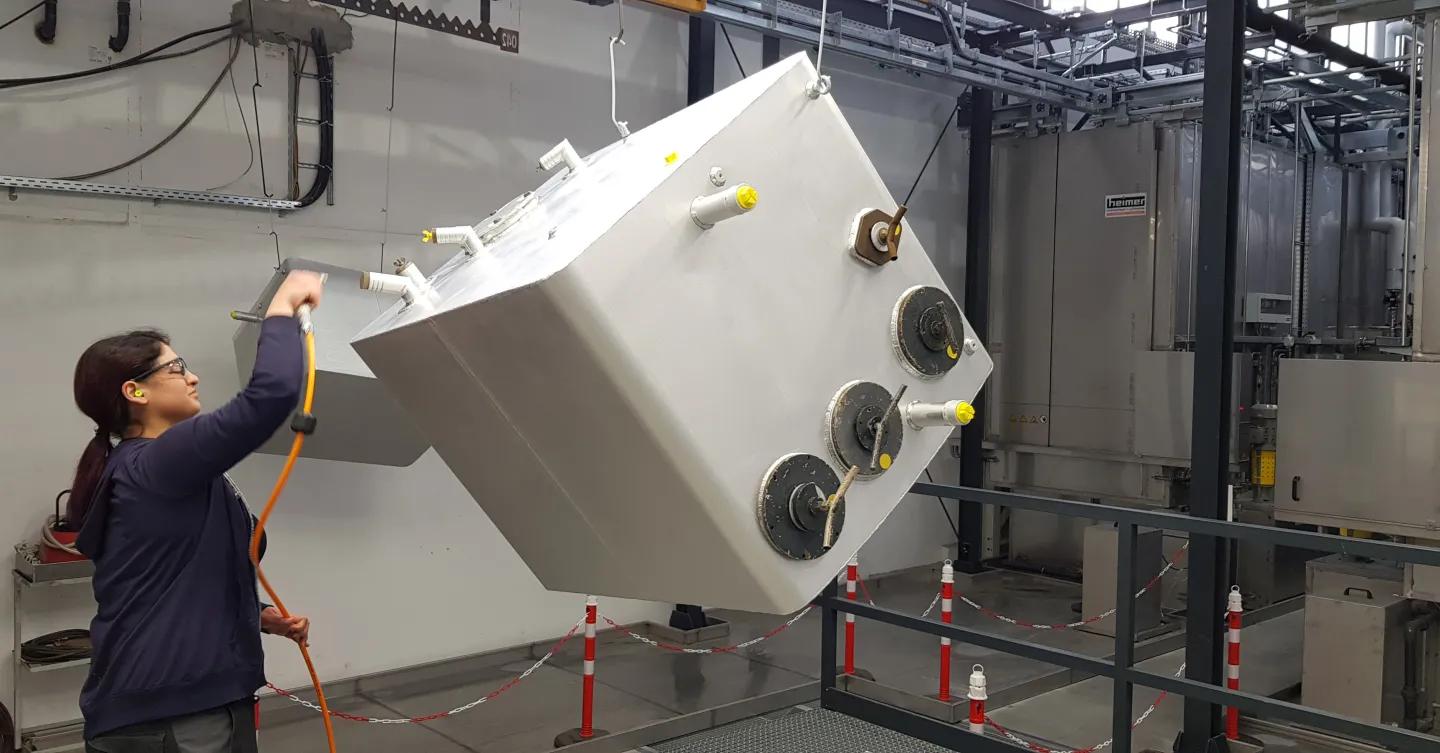
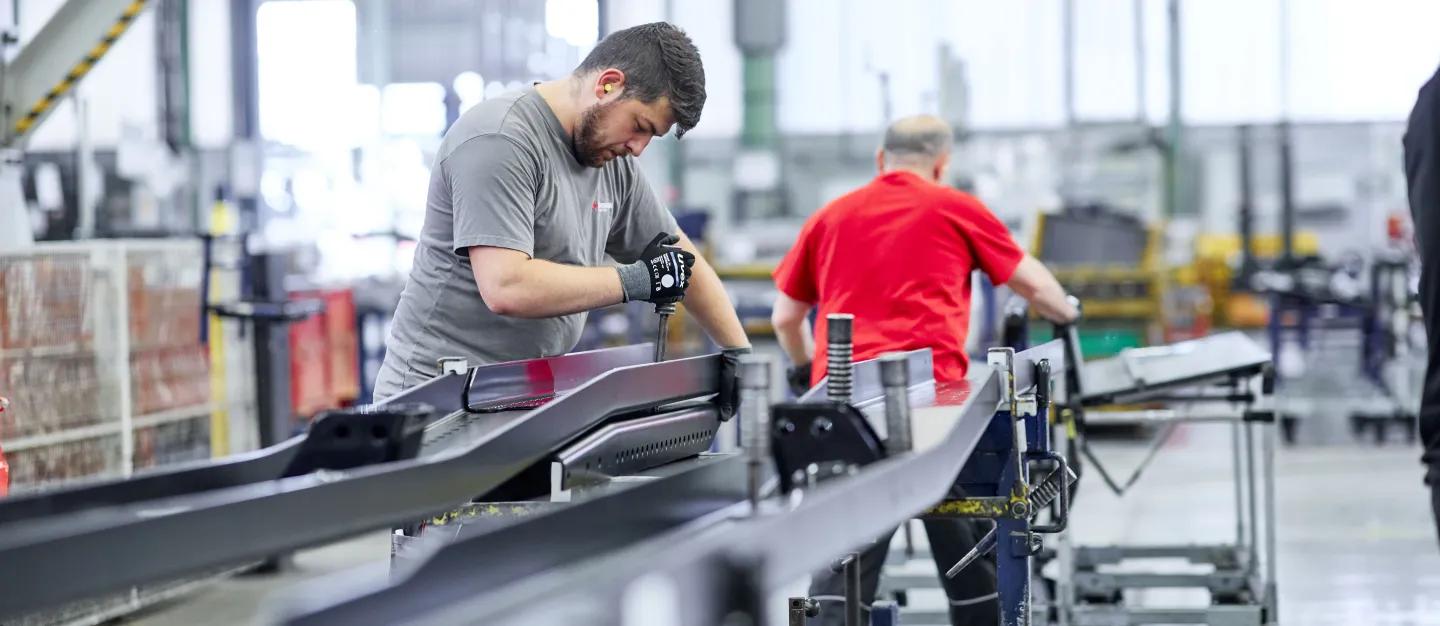
Pre-Assembly
We support the continually increasing focus of our customers on their core competencies at the end of our process chain via the realisation of pre-assemblies both of individual components or modules and of complete systems, such as chassis frames for heavy-duty trucks. In this connection, we also offer consulting services and the performance of intelligent logistical processes as well as packaging and transport management in addition to pure assembly competence.
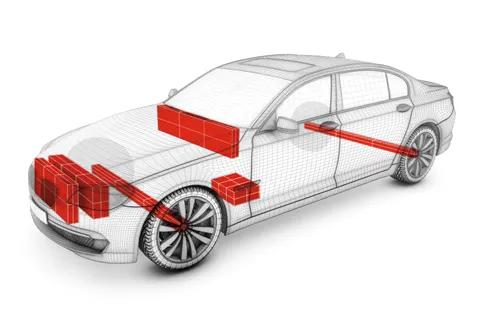
Assembly and Sequencing
Thanks to our many years of experience in the assembly and sequencing of modules and systems in the automotive sector, we are able to offer every customer a concept tailored to meet their requirements. In addition to customer-oriented process planning and the overall schedule coordination, this also includes the planning, realisation and ongoing monitoring of the entire supply chain. Our concepts range from large-volume assembly scopes with a corresponding degree of complexity and a large number of variants that we produce in a highly efficient manner with a corresponding degree of automation, to projects with low volumes that we produce in a demand-based manner in production cells with low investment requirements. Pure sequencing of component parts as what it known as a “carset” is of course also possible. Our ppm figures are the benchmark in the sector. The wide range of modules extends from pedals and pedal assemblies to cooling modules, centre consoles, roll bars to system carriers and other module scopes.
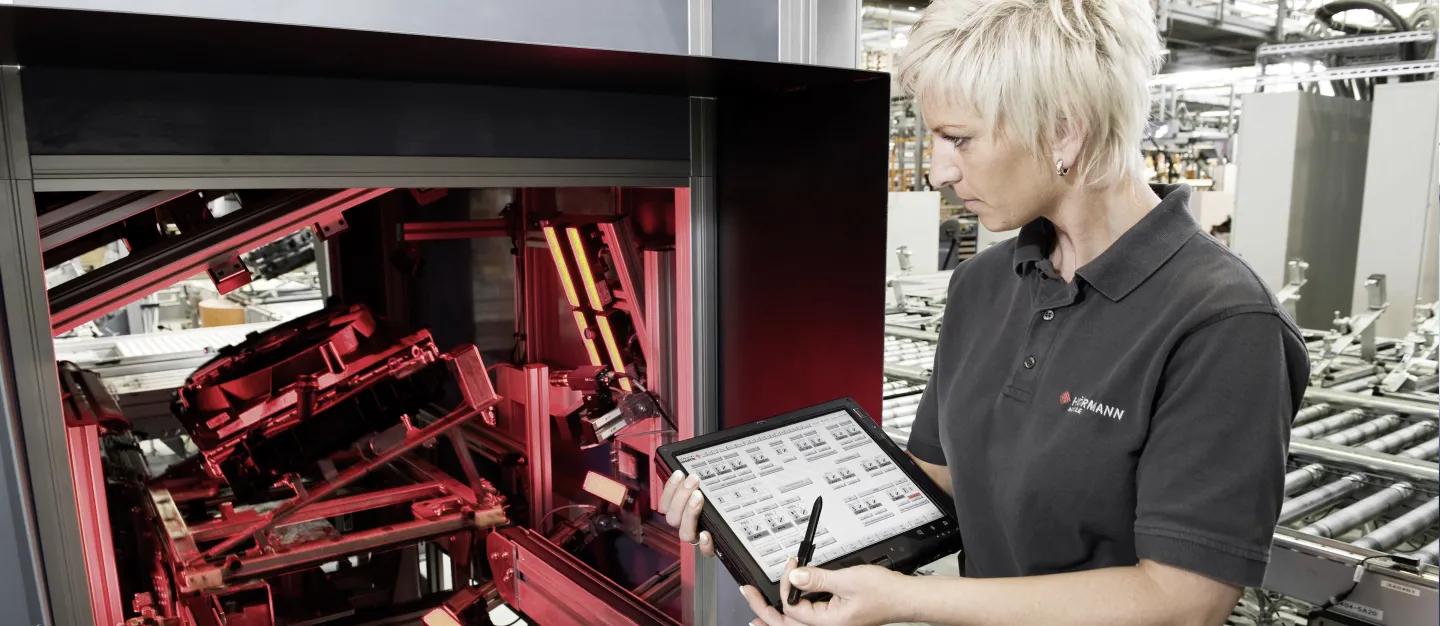
Our range of services covers the following:
- Process planning
- Investment for the required systems and tools
- Realisation in accordance with APQP and PPAP/PPF incl. sample processing
- Procurement of components (alternatively provided by customer)
- MRP for purchased parts
- Transport coordination for all incoming goods
- Assembly of offer scope
- Monitoring of supply chain, supplier management, supplier development
- Change management for components and systems
- Delivery of goods in accordance with delivery release order(s), JIS, JIT

Development Support
From the idea to series production: As a supplier to the commercial vehicle, agricultural machinery and construction machinery industries, HÖRMANN Automotive faces the daily challenge of industrialising new tools and processes for the production of its components. Efficient and targeted project management helps us to meet cost and time targets and provide our customers with the best possible support throughout the product development process. We focus on digitising the product development process as far as possible, particularly with regard to the safeguarding and optimisation of series processes. By working closely with our customers, we can use our technological expertise to help them optimise the design of components in terms of costs and technological feasibility. In doing so, we build on a broad network consisting of internal Group expertise, external service providers and universities.
We support our customers in large parts of the product development process as part of their development projects:
- Method Development
- Project Management
- Implementation of optimised technological approaches
This early involvement in the product development process offers decisive advantages: Based on our extensive technological and methodological expertise, we help our customers to optimise their component design in line with existing production restrictions. This leads to cost-optimised solutions for a given component design and reduces valuable time in the subsequent industrialisation process.
1. Method Development
Based on our technological expertise, we are able to take over the component design and development for you to meet your specific requirements. To do this, we also draw on the group-internal synergies of HÖRMANN Vehicle Engineering, which provides consistent CAE chains and expertise in the area of component design and analysis.
As part of development, we take into account production-related restrictions and potential savings or improvements in order to optimise your product and the underlying process both with regard to costs and feasibility. We can thus plan the quality you request.
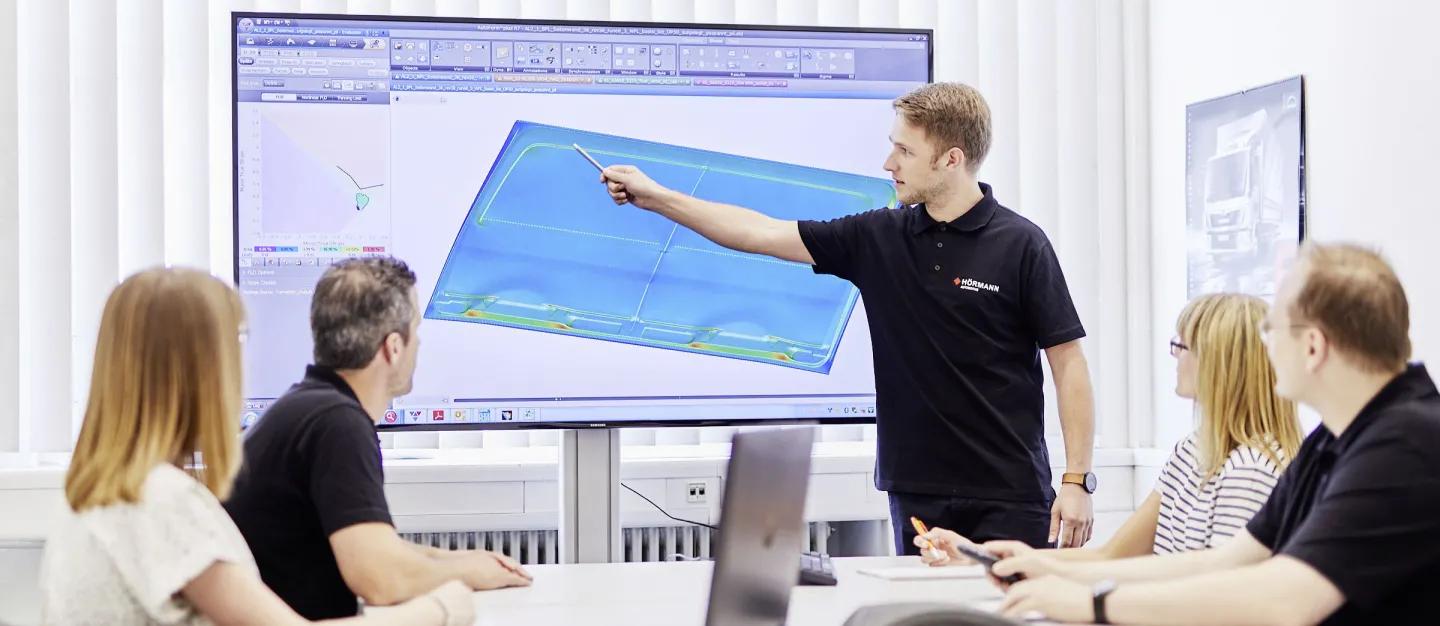
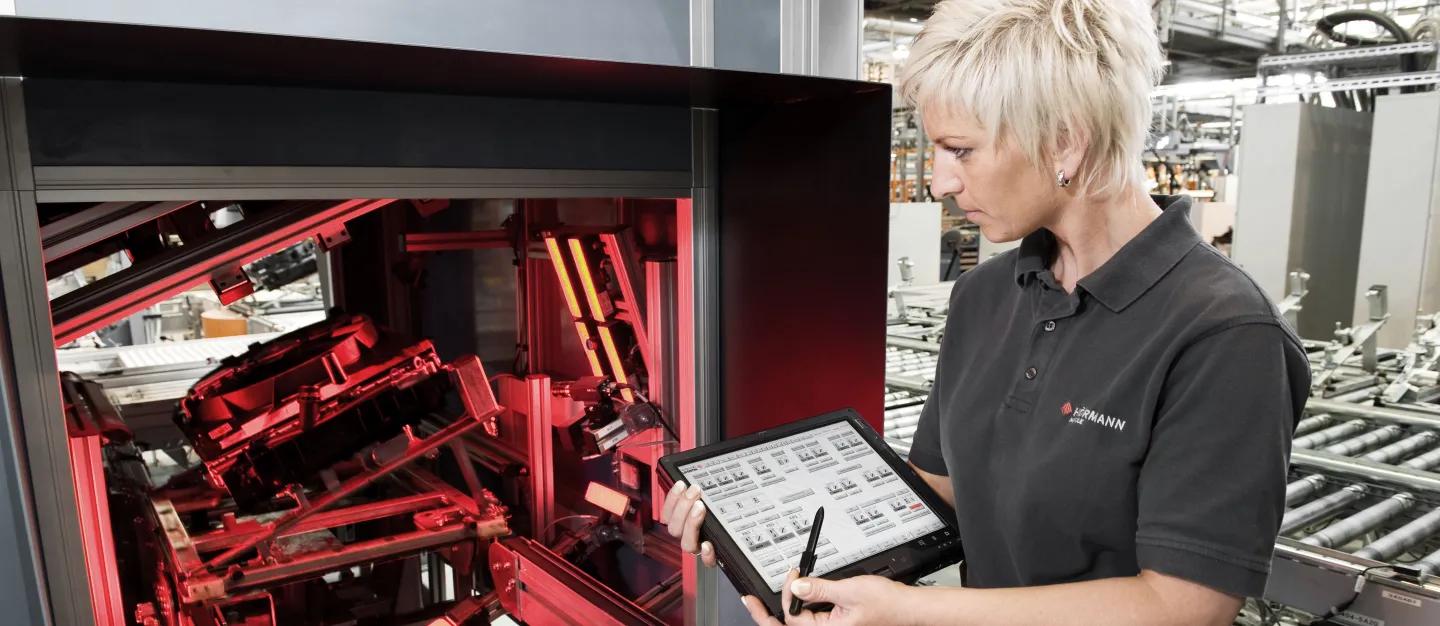
2. Project Management
Based on the desired component design and the technological process design, we take over component realisation and the associated project management for you up to and including series production.
To do this, we draw on our own resources for tool design and our own toolmaker’s shops as well as on an extensive international network of service providers and toolmakers. Based on our technological and methodological expertise, we guarantee the originally planned quality.
3. Implementation of optimised technological approaches
We support you in the realisation of your products via targeted enhancement of our technologies. For this purpose, we rely on the broad range of technologies covered by our locations and on technological innovations from our advanced product development. Decisive drivers here are the processing of lightweight materials, process integration and cost effectiveness. We achieve this by working in an ecosystem consisting of suppliers and universities by means of which our technologies undergo permanent enhancement.
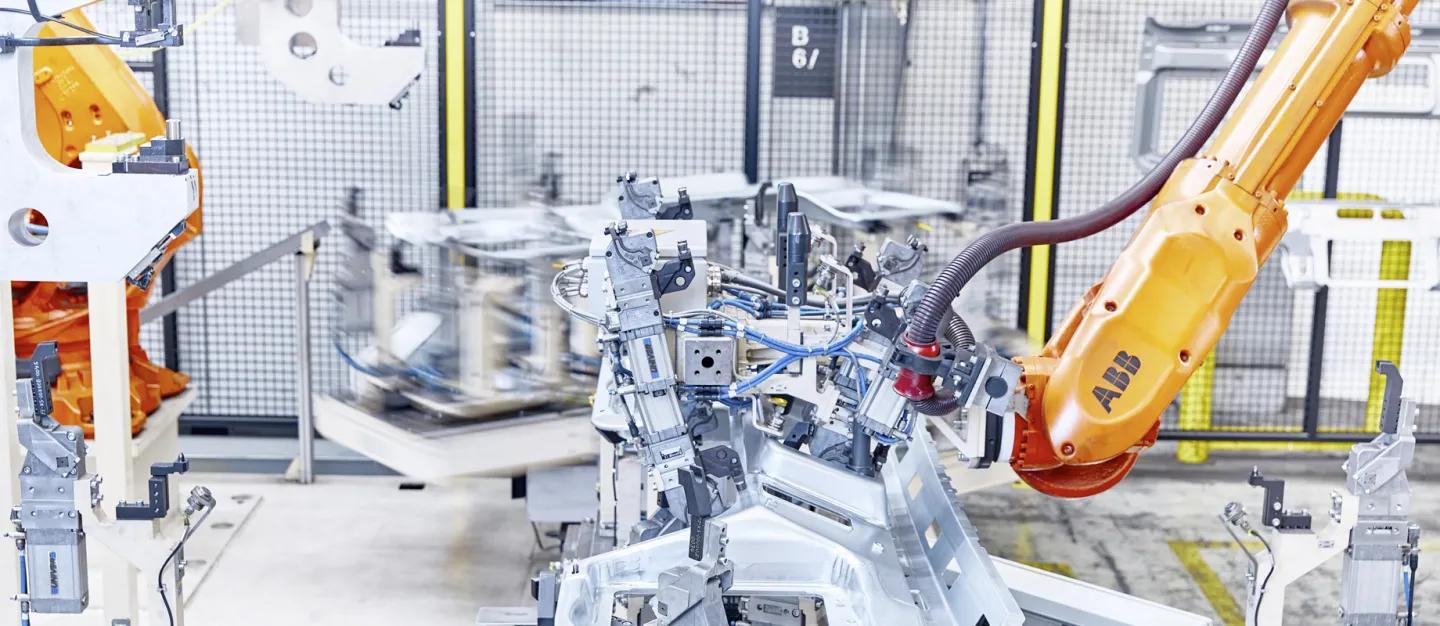
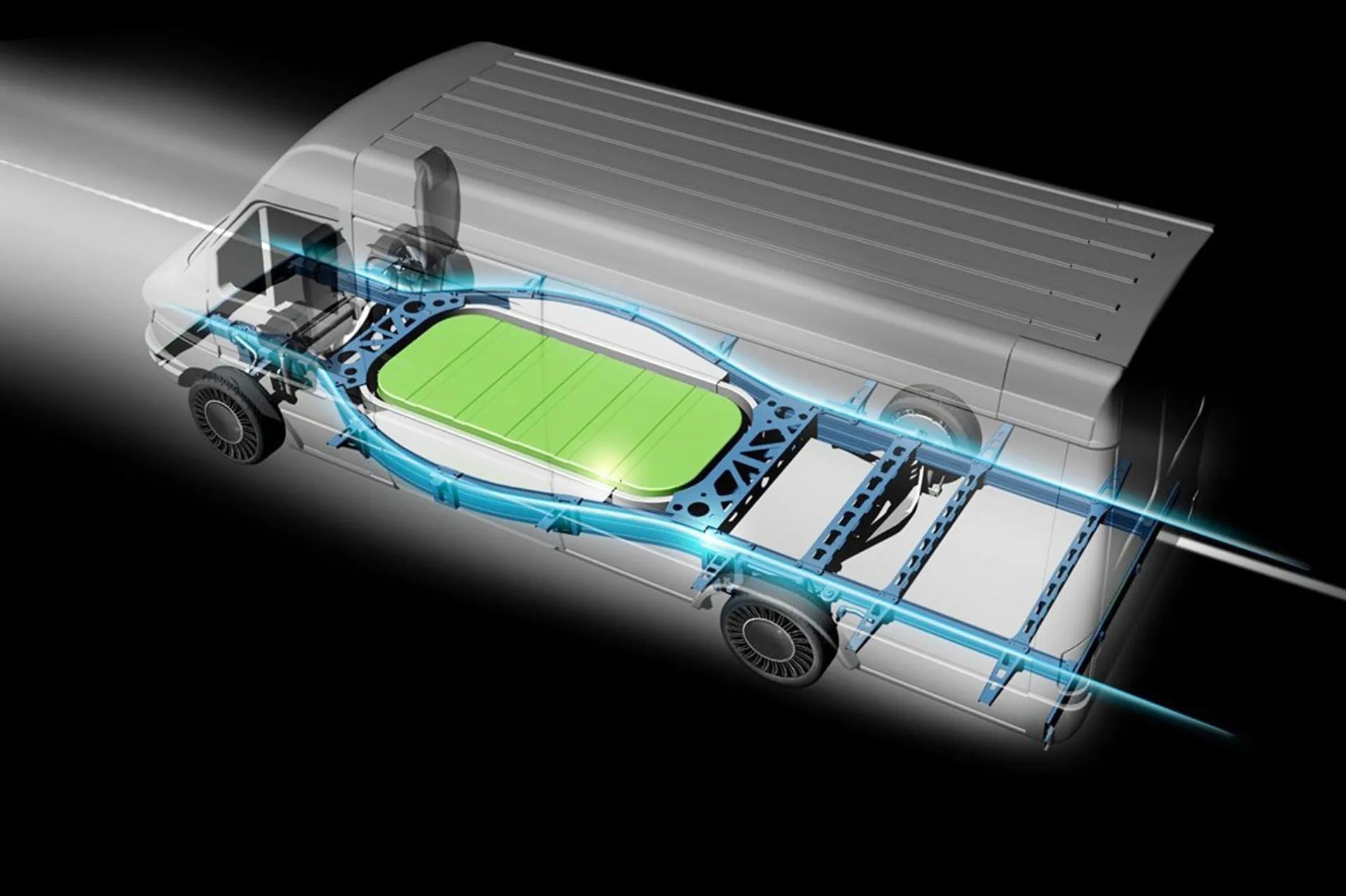
Innovation
Innovation goes hand in hand with customer benefit. We achieve this through close dialogue with our customers and close integration in our network of competence centres, universities and technology partners.
Our current technological focus is on the realisation of cost-efficient lightweight solutions, which are indispensable for our customers, particularly in light of the current trend towards electromobility. We are focussing on both structural and lightweight material solutions. We see both approaches as crucial in the commercial vehicle sector and are therefore intensively involved in the industrialisation of new lightweight steel construction technologies and strategies for processing promising lightweight materials.
Our claim is clear: we want to shape the mobility of the future together in a network of customers, universities and competence centres.
1. New, innovative product approaches
As an established system supplier to the commercial vehicle industry, HÖRMANN Automotive is committed to making a contribution to CO2-neutral logistics together with our customers through new ideas and approaches.
The associated challenges for the commercial vehicle industry in this context are immense and spur us on to overcome them together with our partners and customers.
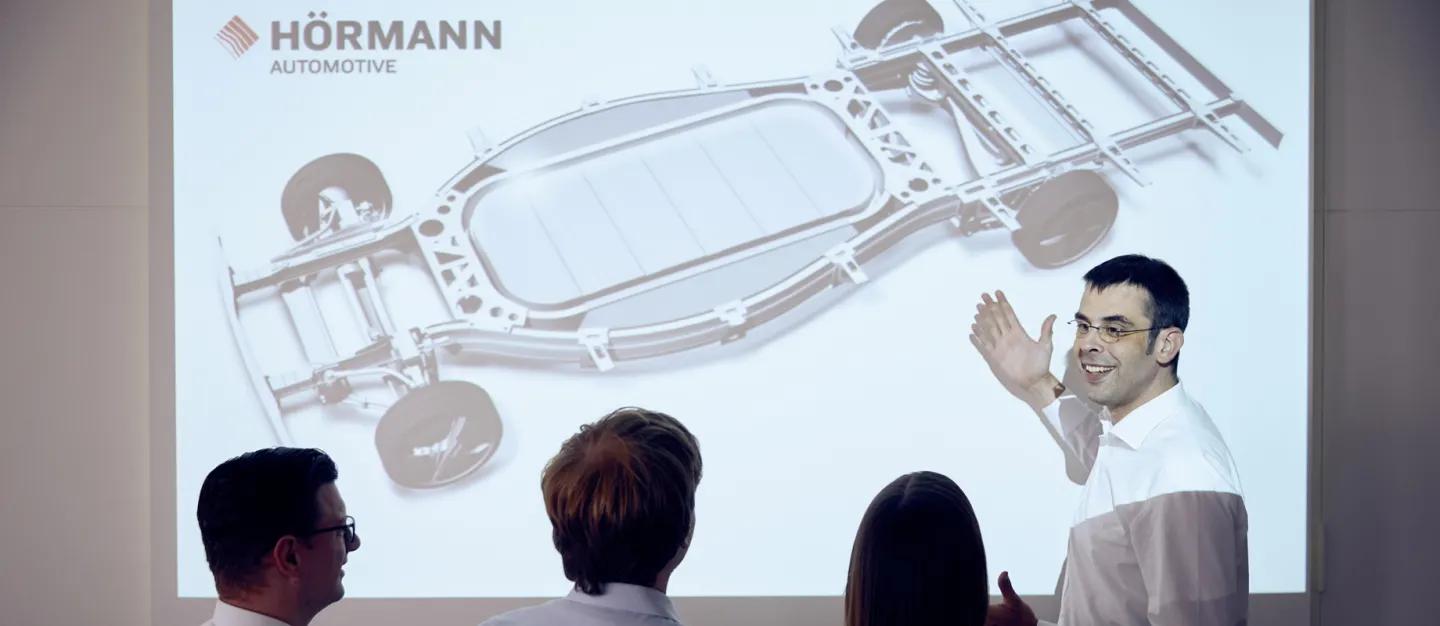

Innovation for heavy-duty commercial vehicles
For HÖRMANN Automotive, the levers for innovation in heavy commercial vehicles range from economical lightweight construction approaches to functional and component integration and new topological vehicle structures.
We are also thinking in terms of completely new vehicle systems in conjunction with the semi-trailer in order to equip ourselves technologically in the best possible way for future requirements in heavy commercial vehicles.
Here, synchronous technology development in the areas of forming and joining technology provides us with significant input for the realisation of new structures and systems that differ fundamentally from today's ladder frames in terms of weight, cost, functionality and the integration of alternative energy sources.
We are guided here by customer concerns, which we see not only in terms of weight, variance and costs, but also in particular against the background of emissions legislation for the years 2025 and 2030. New solutions are needed - which is why we are already thinking them through today.
Innovation for light-duty commercial vehicles
Solutions for future inner-city mobility and logistics require new, customised systems for alternative drive sources. To this end, we have developed a chassis concept for lightweight, electrified commercial vehicles.
It is characterised by a bionic lightweight construction approach, which is reflected in both the topology and the component design. The non-linear chassis topology enables systemic protection of the energy storage in the chassis and thus reduces the weight and costs of accommodating and protecting the batteries. The non-linear longitudinal members, in turn, are designed as steel multi-chamber profiles, which are specifically designed to absorb the impact energy in the event of a side crash.
> The HÖRMANN Group with innovative chassis concept at the IAA
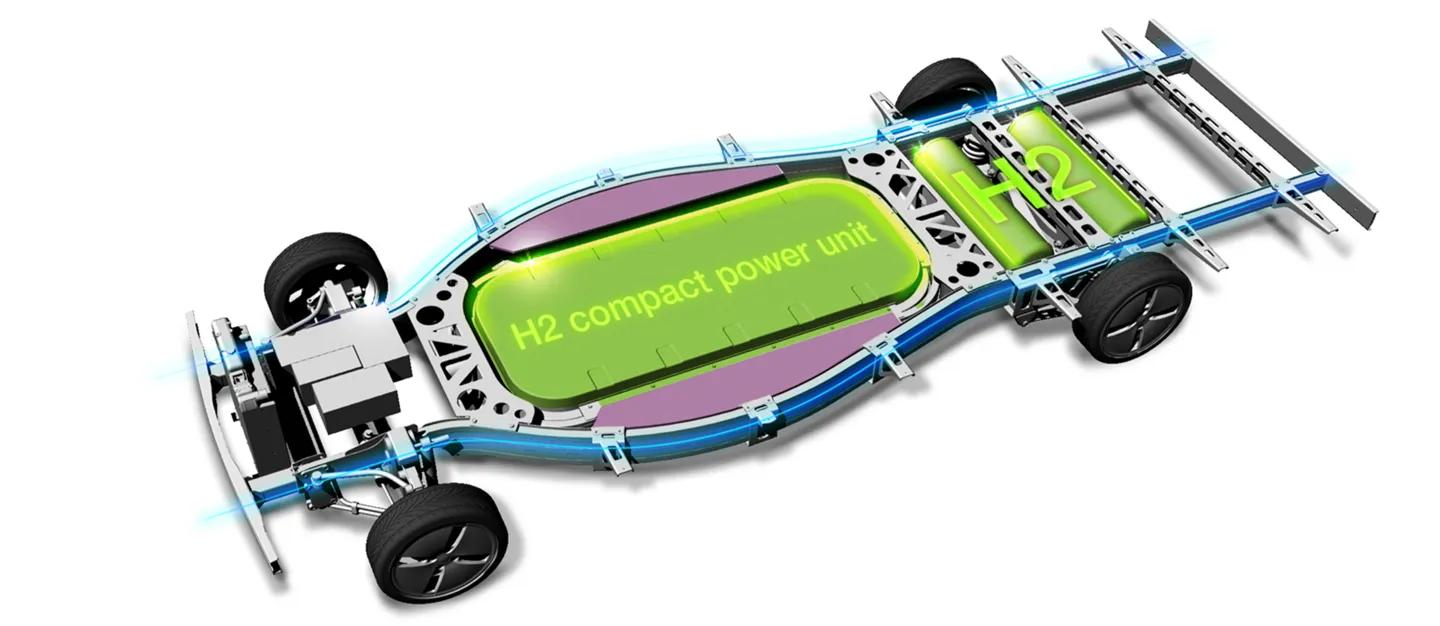
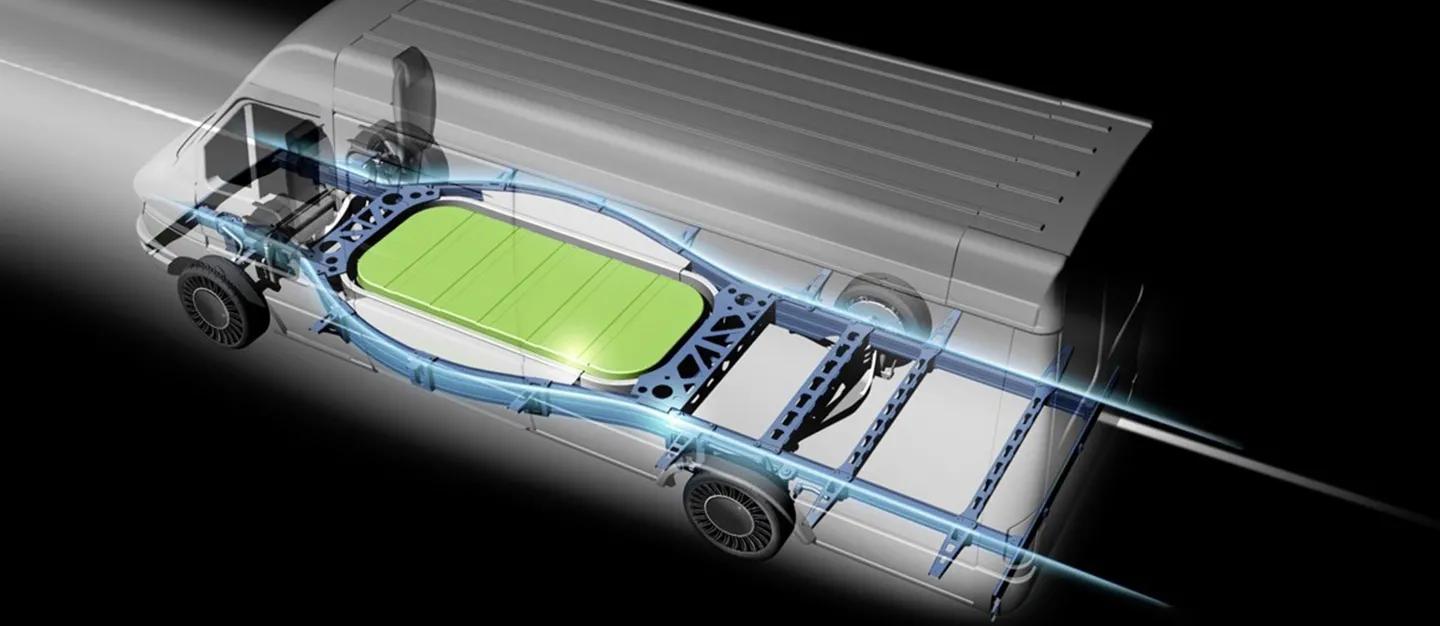
The underlying, innovative production technology enables a high degree of variance in the profile without additional mould costs and is therefore able to cover a high degree of vehicle variance in terms of wheelbase and battery dimensions.
The vehicle study is equipped with direct wheel hub drives, which reduces the entry height and maximises the potential load volume of the body at the same time.
Innovation for railway traffic
Together with HÖRMANN Vehicle Engineering, HÖRMANN Automotive is also breaking new ground in rail transport. The development of a new type of carrier wagon for rail freight transport is moving away from conventional welded assemblies and is instead based on a mechanically joined lightweight truss structure.
The carrier wagon concept addresses several customer benefits: By using highly efficient production technologies, the standardised truss elements can be manufactured cost-effectively and in short cycles. The subsequent use of mechanical joining processes reduces production costs and component distortion and also speeds up the assembly time.
At the same time, the trolley structure can be customised to different lengths and container loads - both in terms of the required lengths and the underlying loads. The result of this is a significant reduction in material usage and total weight as well as manufacturing costs.
The associated new standardised concept of the headers enables not only a reduction in weight but also the use of different coupling systems and bogies. At the same time, the end pieces can be combined with different centre segments, which increases flexibility and reduces overall costs.
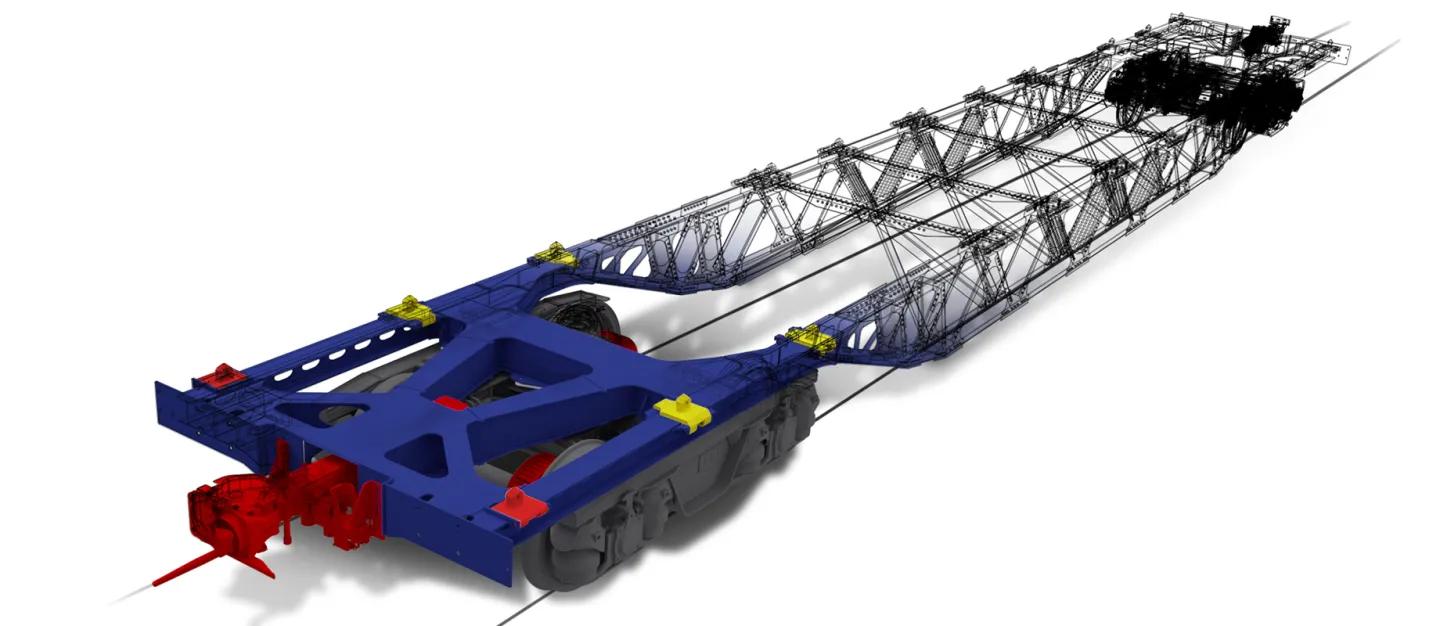
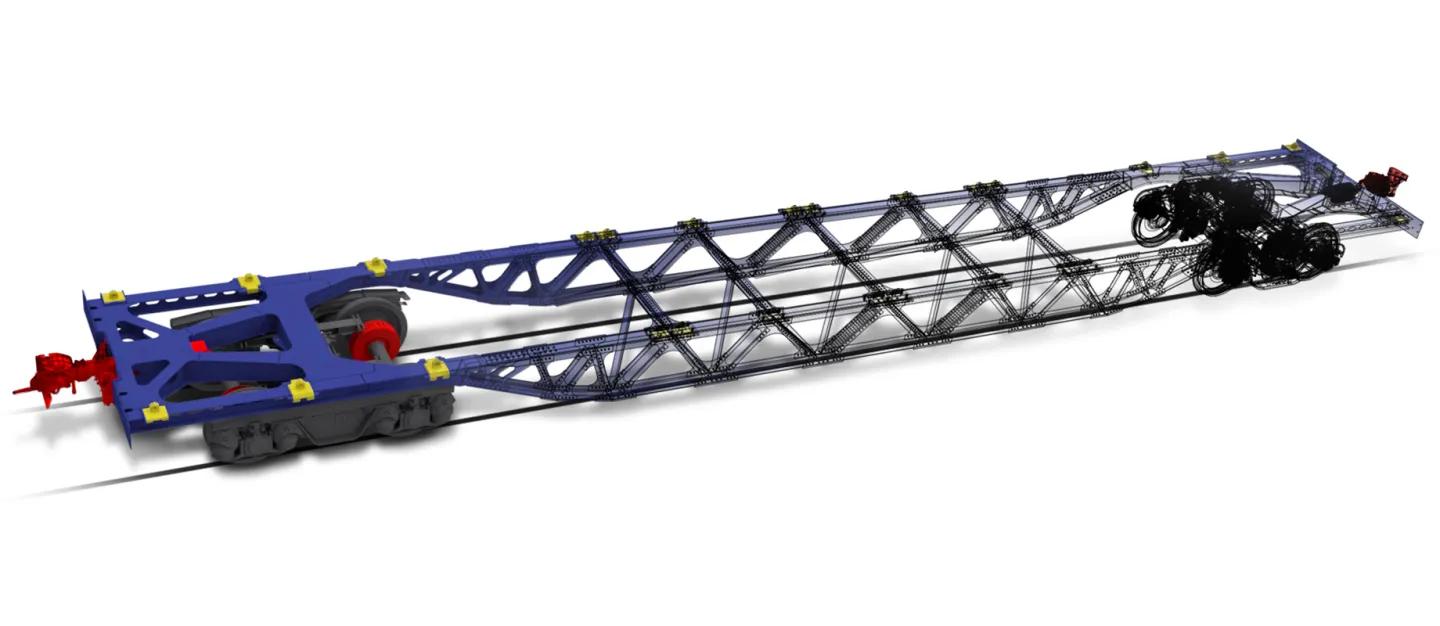
Innovation for semi-trailers
Lightweight construction in semi-trailers enables increased payloads and thus increased transport efficiency. The key prerequisite for this in a highly cost-sensitive market is economical lightweight construction strategies. HÖRMANN Automotive has developed lightweight construction concepts that can make a sustainable contribution to reducing the weight of semi-trailers and form the basis for the ongoing development of an ultra-lightweight trailer concept.
The vision is to turn the semi-trailer as the actual ‘goods carrier’ into a digitalised core element of future, climate-neutral heavy goods transport.
2. Innovation in Technology Development
We support you in realising your ideas with new technological approaches. To this end, we work consistently to further develop our technologies and processes in line with the latest trends, which are currently impacting us in the form of alternative drive systems and digitalisation.
Development of lightweight technologies
The discipline of lightweight construction is experiencing a completely new relevance against the backdrop of alternative drive systems: The aim is to reduce moving masses in order to gain range and compensate for additional loads due to energy storage. We are doing this by developing new process chains for processing high-performance steel and non-ferrous materials. At the same time, we see great potential in the technological ability to create load-adaptive structures in lightweight structural engineering. Conventional forming processes often only offer the necessary degrees of freedom at considerable additional cost. With increasing flexibility of the forming process in terms of the degrees of freedom that can be achieved, we see ourselves in a position to produce load-optimised structures and to be able to realise these in high variance at attractive cost. We are currently pursuing this goal in particular with our endeavours in relation to free-form bending and gap profiling.
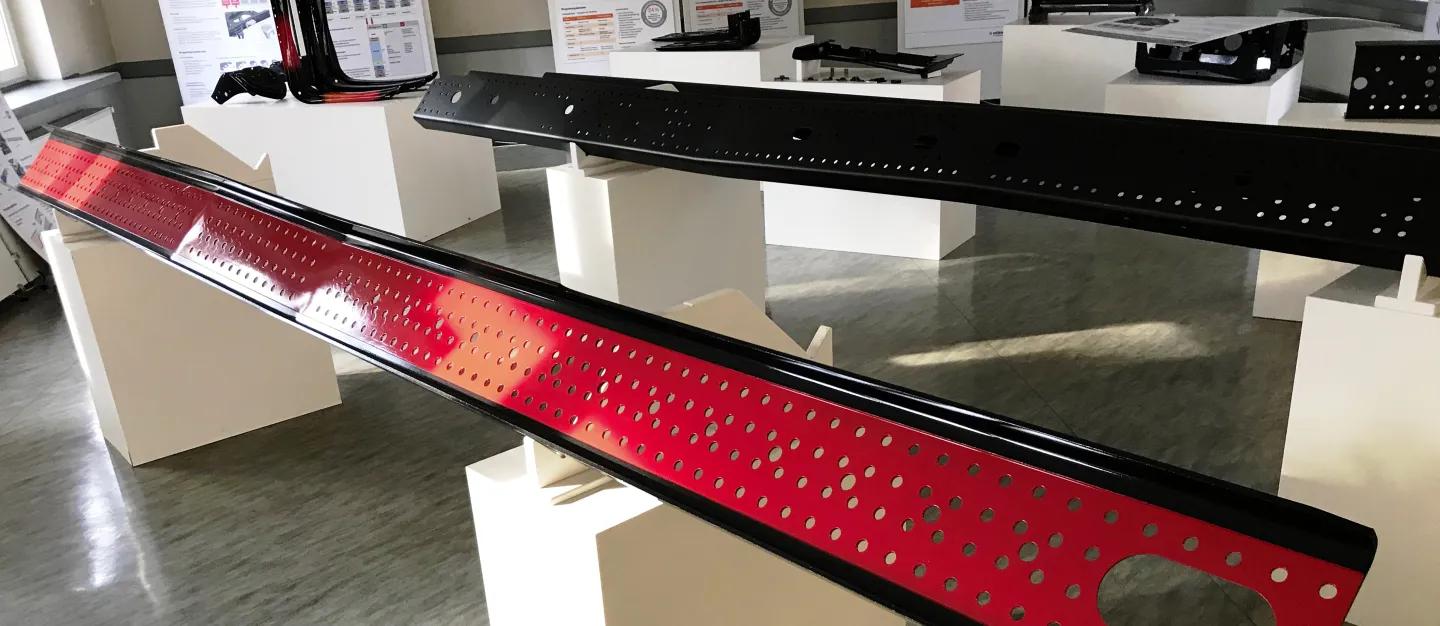
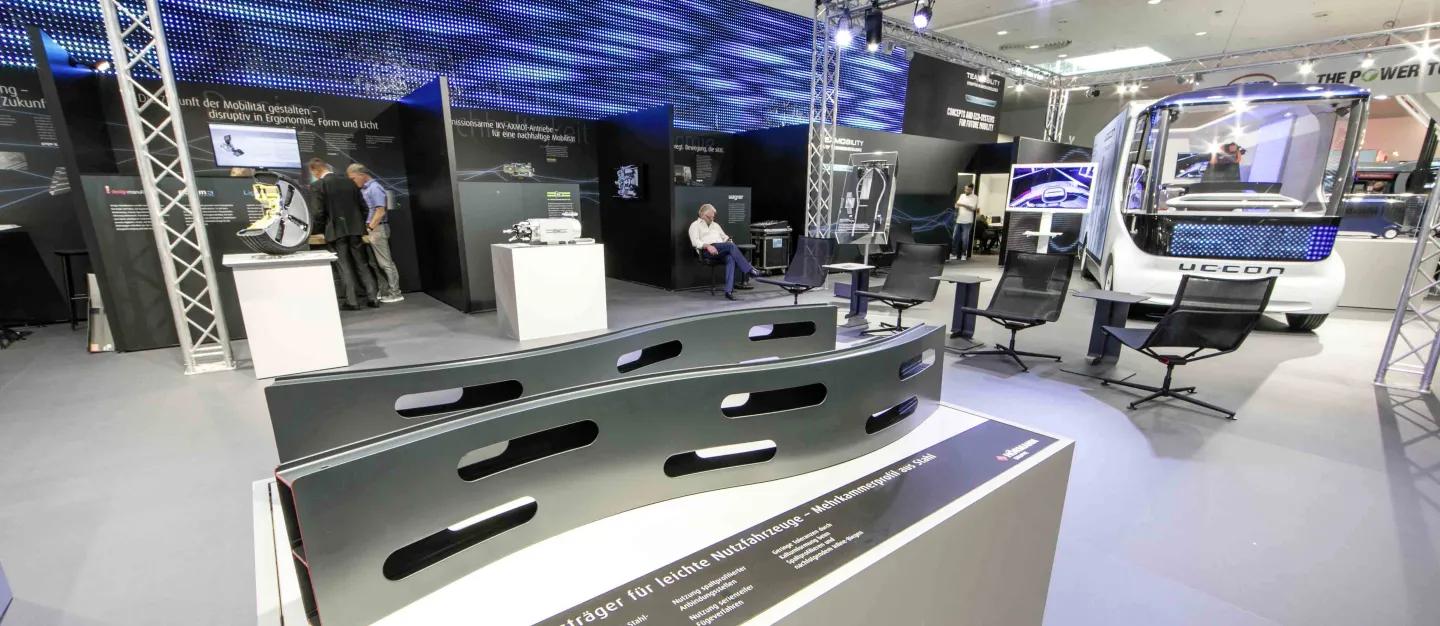
Integrally branched structures due to linear flow splitting
The production of integrally branched profiles offers innovative solutions in terms of component connection and the utilisation of integrally branched multi-chamber profiles. In this process, a flat sheet is formed into a double-T profile as part of a continuous rolling process by moulding rollers on both strip edges, which offers new design options in terms of lightweight construction and functional integration. At the same time, it is possible to produce non-linear profiles by integrating a bending process into the production line. This means that the ‘gap profiling’ mass production process can also offer significant added value in applications with high variance. This has been proven in the context of the bionically orientated vehicle topology of the Hörmann integral chassis, which can be produced with minimal tool investment thanks to the process chain described, even with high variance - particularly in terms of wheelbase and chassis dimensions.
Free-form bending
The stringent continuation of the technological focus of tube bending at HÖRMANN Automotive is free-form bending. Extensive geometric design freedom in the profile without additional tool costs enables the cost-attractive production of innovative, topographically optimised structures. We work closely with system manufacturers and universities in the ECO system to further develop free-form bending against the background of batch- and geometry-related component tolerances through adapted control and regulation mechanisms.
Development of process chains for the production of hybrid composites
In many cases, multi-material systems offer added value, particularly in the area of large-scale component applications in the agricultural machinery sector, which are both weight and wear-sensitive and also have to fulfil additional functions due to the attachment of a wide variety of add-on parts. We take this trend into account and are involved in the development of metal-plastic composites with a focus on optimising the use of materials and intelligent options for process integration while maintaining component performance.
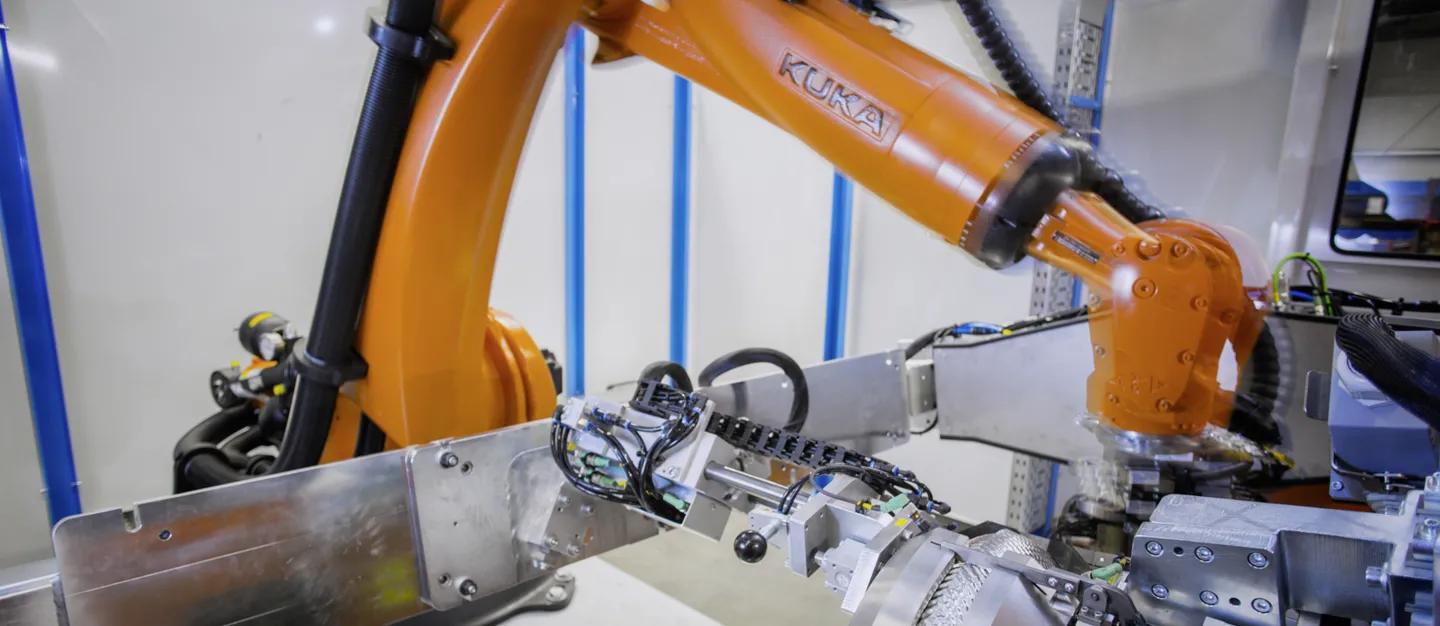
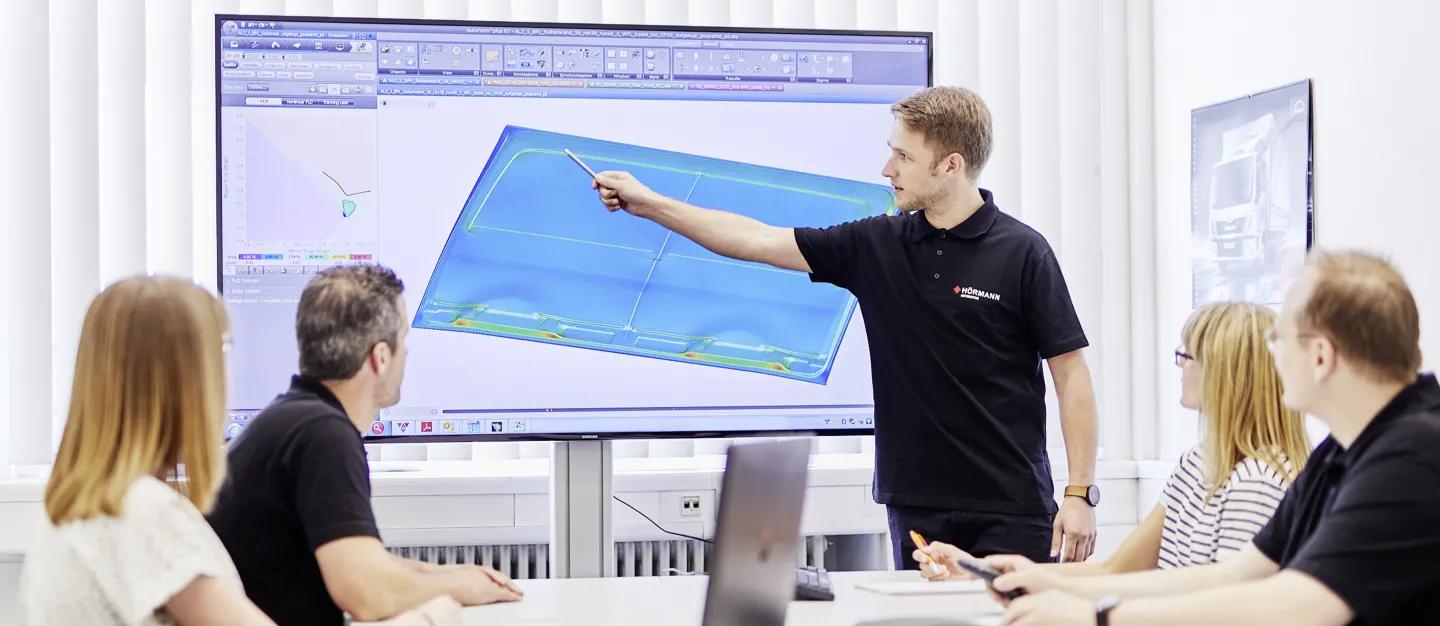
Digitalisation in forming Technology
Smart tools
New approaches to tool digitalisation allow us to track component quality where it is created: in the tool. The integration of sensory elements in tool systems allows us to have a transparent view of the forming process for the first time and thus enables us to develop technological processes based on cause-and-effect chains within the tool.
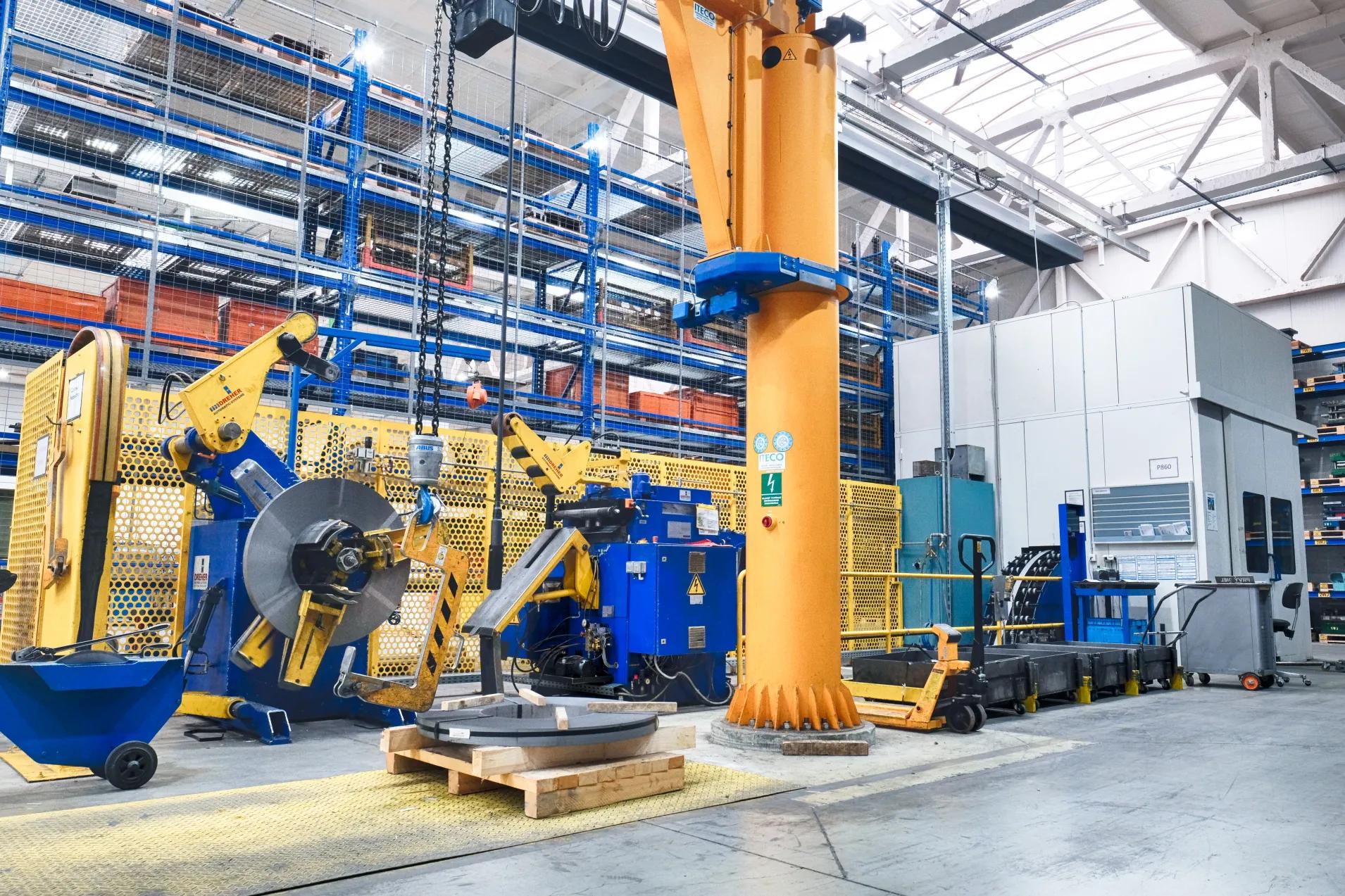
HÖRMANN Automotive Slovakia s.r.o
HÖRMANN Automotive Slovakia GmbH is your ideal partner for the production of high-quality, cost-optimised components and systems made from metal.
Components and systems made from metal
We currently produce approximately 1,300 different products and deliver on a daily basis around 30,000 components to our customers. In three-shift operation, we process approximately 40 tonnes of single rolled and coil sheets in different thicknesses, formats and widths every day.
State-of-the art technology in laser systems, folding presses, robot welding systems and above all our approximately 300 employees have made us a sought-after partner for the vehicle industry.
Every day, we utilise all our experience and expertise to fulfil the requirements of our customers with regard to flexibility, quality, reliability and economic efficiency without compromise.
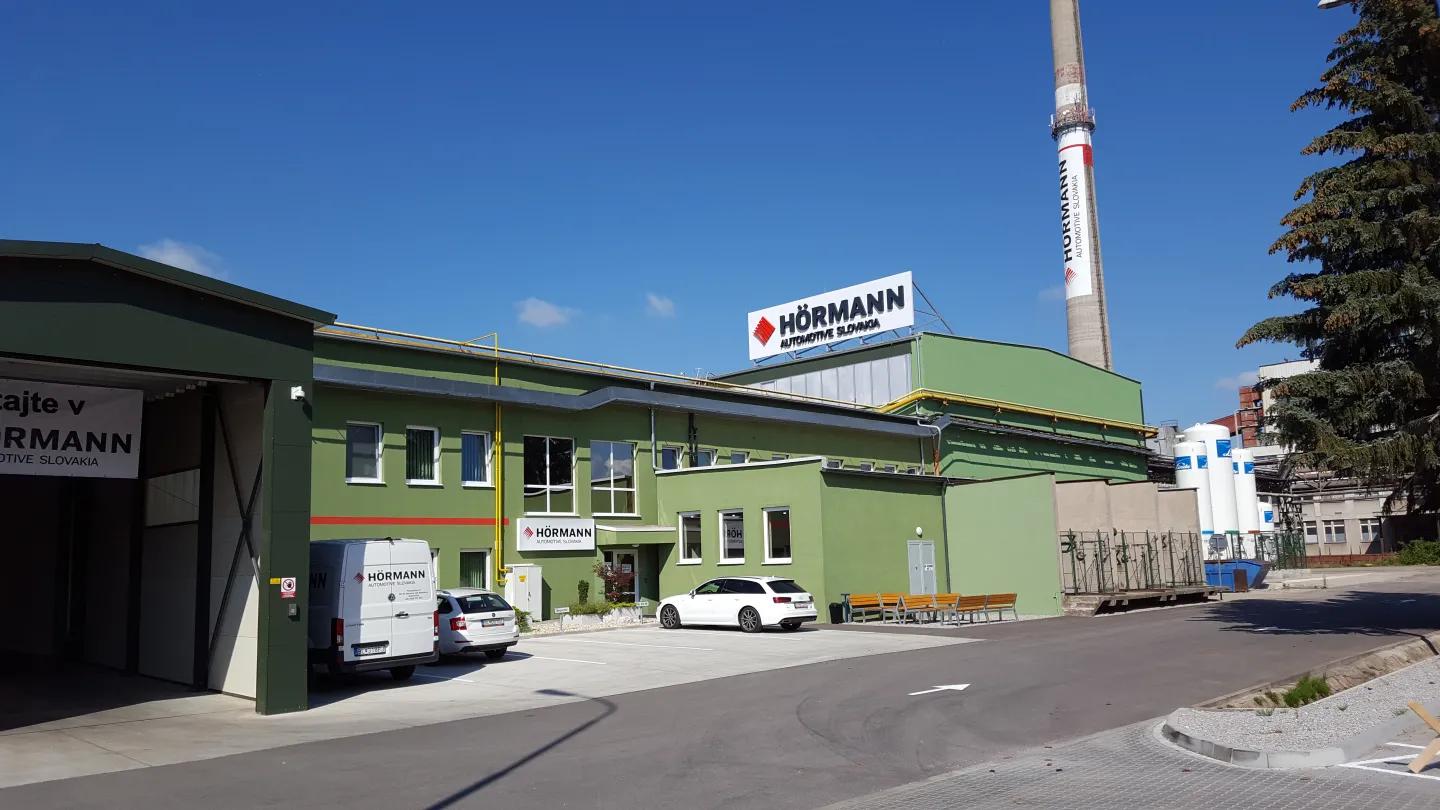
HÖRMANN Automotive Slovakia s.r.o
Partizanska. 73
95701 Banovce nad Bebravou
Slowakei
Your Contact
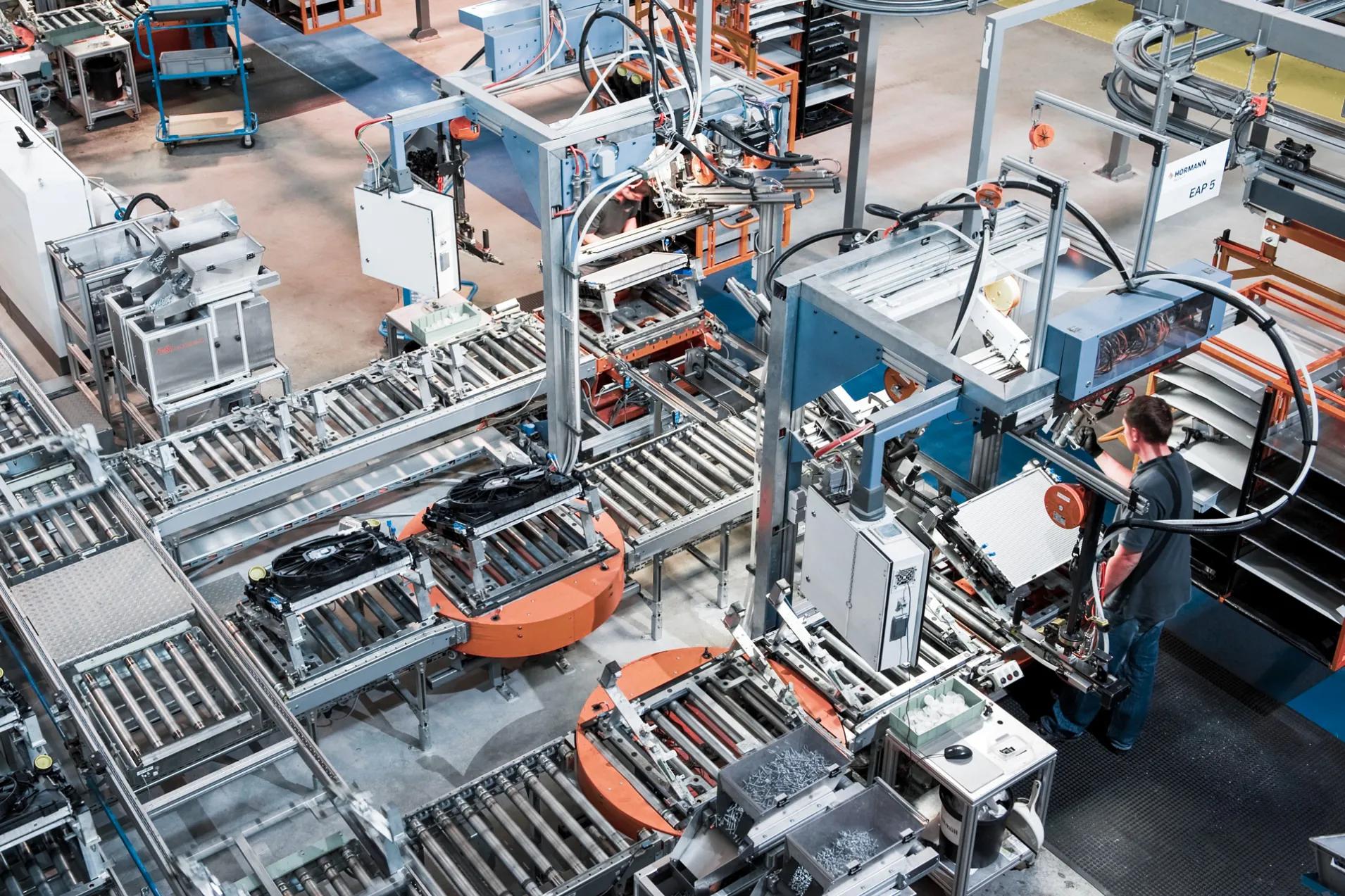
HÖRMANN Automotive Wackersdorf GmbH
HÖRMANN Automotive Wackersdorf becomes HÖRMANN Systems Assembly
HÖRMANN Automotive Wackersdorf GmbH has changed its name to HÖRMANN Systems Assembly GmbH due to a strategic reorientation and will be integrated into the HÖRMANN "Communication" division. With this step, the company is strengthening its commitment in the areas of charging infrastructure, robotics, digital signage and other future markets.
To this end, HÖRMANN Systems Assembly will continuously expand its range of services, particularly in the area of industrialisation. The aim is to develop into an "all-in-one" partner for customers in order to provide them with the best possible support in all areas.
"With the new alignment as HÖRMANN Systems Assembly GmbH, we are ready for the future," emphasises Managing Director Marcus Schaffranka. "We have developed steadily in recent years and can now focus on innovative markets. We are therefore looking forward to this new era and are convinced that we will be successful together as a team."
Click here for the new website: https://www.hoermann-systems-assembly.com/en >>
HÖRMANN Systems Assembly GmbH
Arthur-B.-Modine Straße 2
D-92442 Wackersdorf
T +49 9431 7493-0 • F +49 9431 7493-901
info.wackersdorf@hoermann-gruppe.com
Your Contact
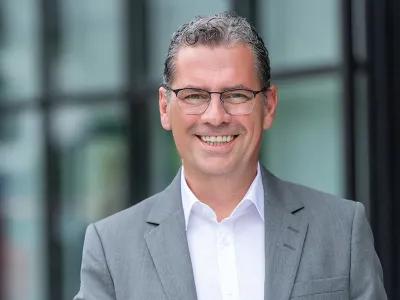
Managing Director in Wackersdorf
Marcus Schaffranka
Thank you for your Message
We will contact you shortly.
Contact
We are always here for you – give us a call or send us a message. We are happy to call back!
HÖRMANN Automotive GmbH
Hauptstraße 45-47
D-85614 Kirchseeon
T +49 8091 5630-0
F +49 8091 5630-195
Your Direct Contact at HÖRMANN Automotive
HÖRMANN Automotive consists of six subsidiaries. Why not get in touch with us directly – we look forward to hearing from you!
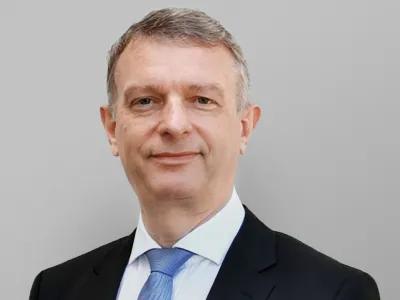
Managing Director in Gustavsburg
Andreas Müller
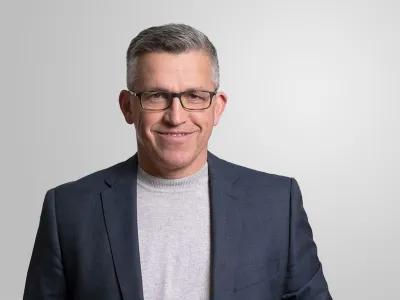
Managing Director in St. Wendel & Saarbrücken
Christian Jacob
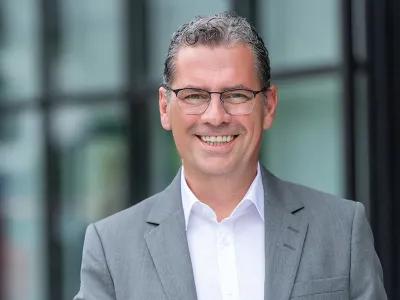
Managing Director in Wackersdorf
Marcus Schaffranka
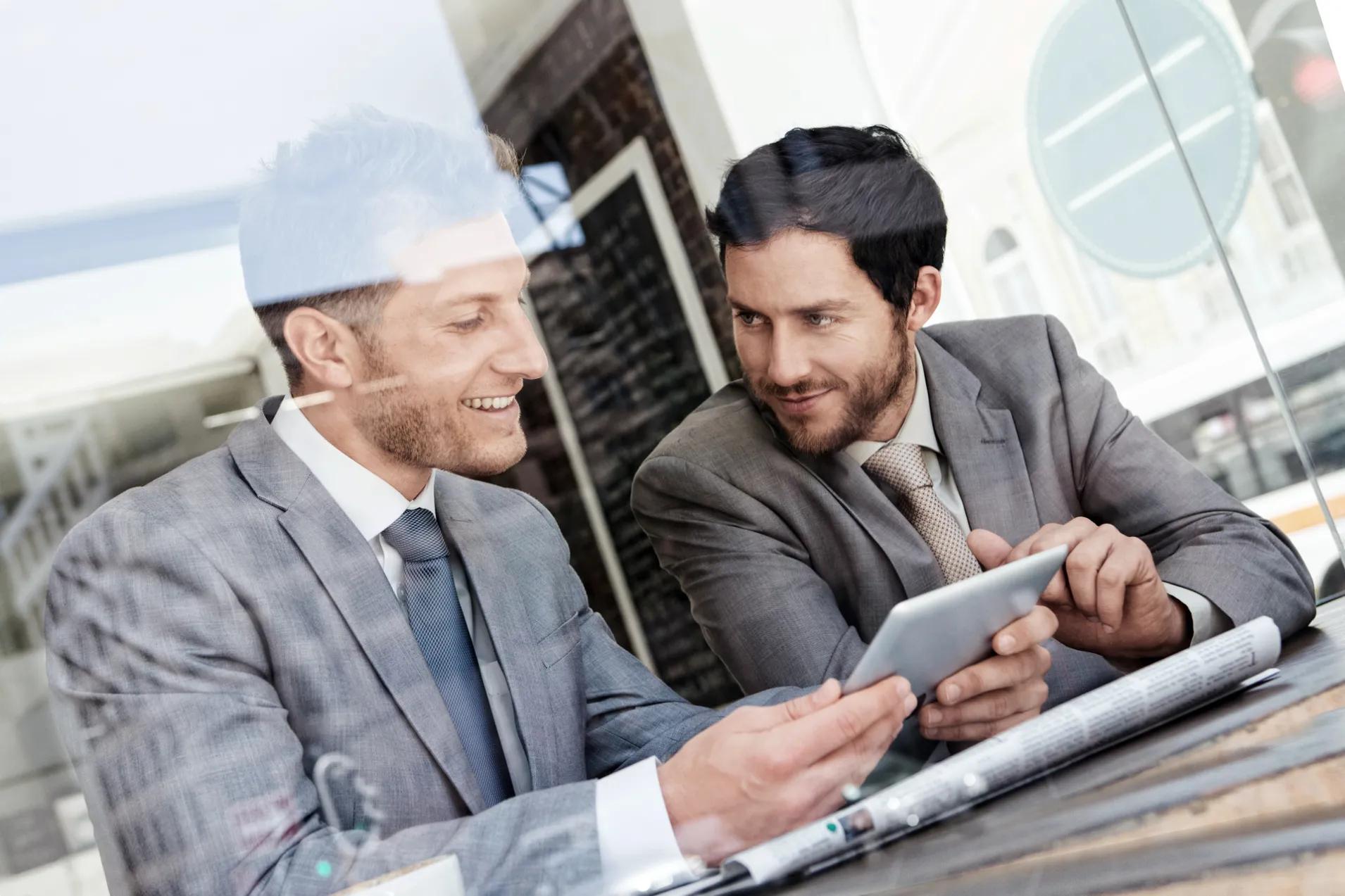
News from HÖRMANN Automotive
2024
2023
2022
2021
2020
2019
2018
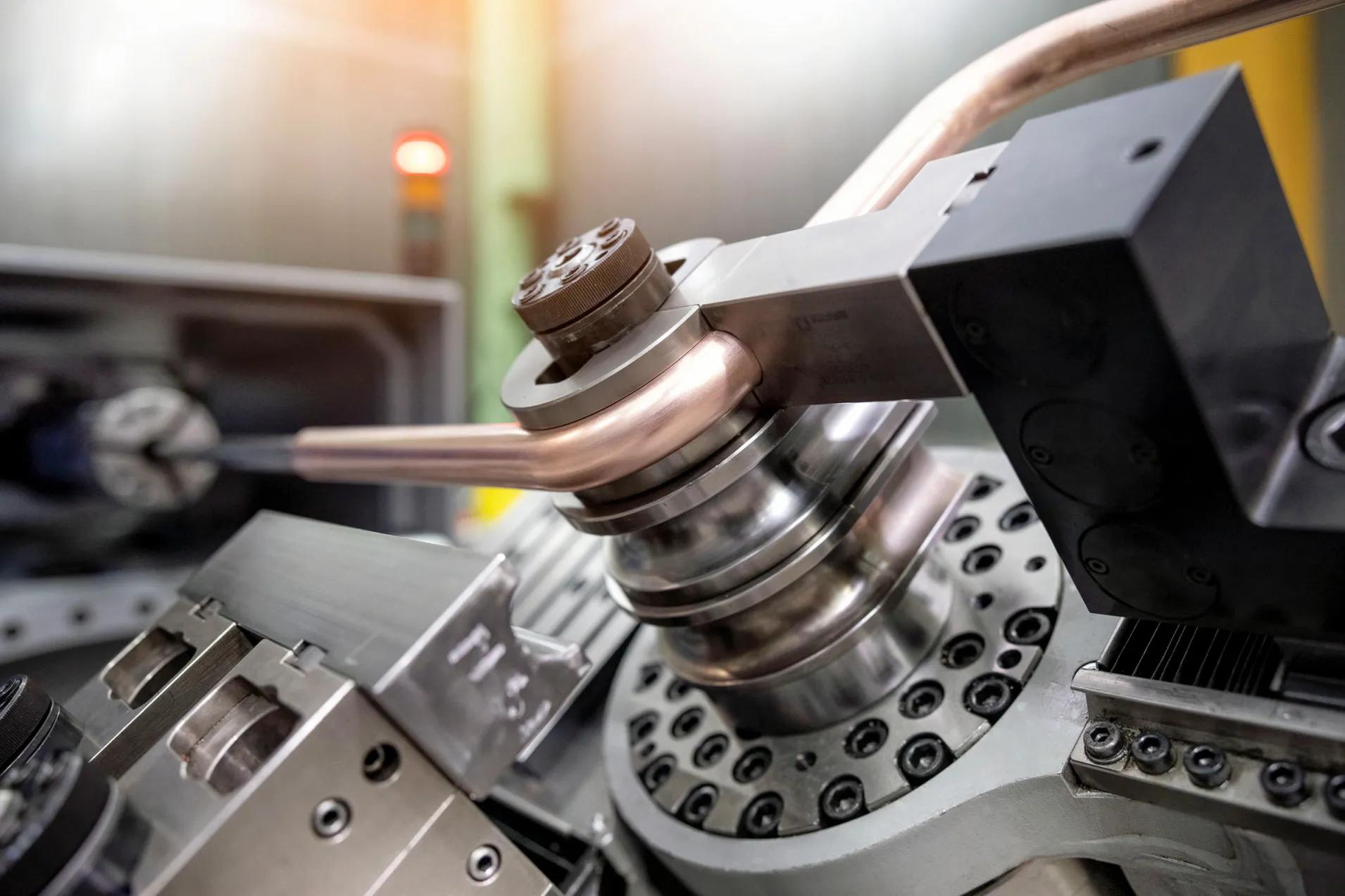
HÖRMANN Automotive Saarbrücken GmbH
HÖRMANN Automotive Saarbrücken GmbH develops and produces welded assemblies as well as pipes for the agricultural machinery and commercial vehicle industries and is specialised in the assembly of interior systems for the bus industry. Since 1933, we have been a system partner to the industry when it comes to innovative and economic solutions for the design and production of components and jigs & fixtures. From component design to prototyping to series production – with our state-of-the-art facilities we guarantee economic and quality assured processing of metals of all kinds.
Production of pipes, welded components and vehicle interior ceilings
At our company site in Saarbrücken, we mainly produce low- and medium-volume series in accordance with special customer requirements on a production area of approximately 7,000 square metres. Be it internal ceiling systems for coaches, refrigerant and fuel lines for city buses and trucks or welded systems – we deliver top-quality products in a vehicle-related manner to the assembly line.
The company's range of services is focused on the order- and customer-related construction of components in small- and medium-volume batch sizes as well as in series production with up to several thousand product variants, primarily pipes for fuel, refrigerant, hydraulics, oil and water, welded systems, welded components and vehicle interior ceilings. In the welding shop, chassis and axle-supporting chassis parts with differing degrees of complexity are mainly produced that are assembled to form welded assemblies and components and delivered directly to the assembly line at the customer via the just-in-time or just-in-sequence method.
Ceiling systems in city buses and coaches
Furthermore, the plant is specialised in the production and ready-to-install assembly of interior equipment systems for commercial vehicles, in particular of ceiling systems. The ceiling systems in city buses and coaches are much more than decorative panels. These now conceal a complex structure of subsystems in a confined installation space that ensure greater safety and comfort for passengers: Assemblies for cooling/air conditioning, audio and lighting must be optimally integrated in the confined installation space available. The objective here is functional reliability as well as weight reduction and ease of maintenance.
State-of-the-art technology such as laser and folding technology, welding robots or CNC machining centres and above all our approximately 130 highly specialised employees have made us a long-term and sought-after system partner for many renowned commercial vehicle manufacturers. We deliver the components from which a whole can be formed.
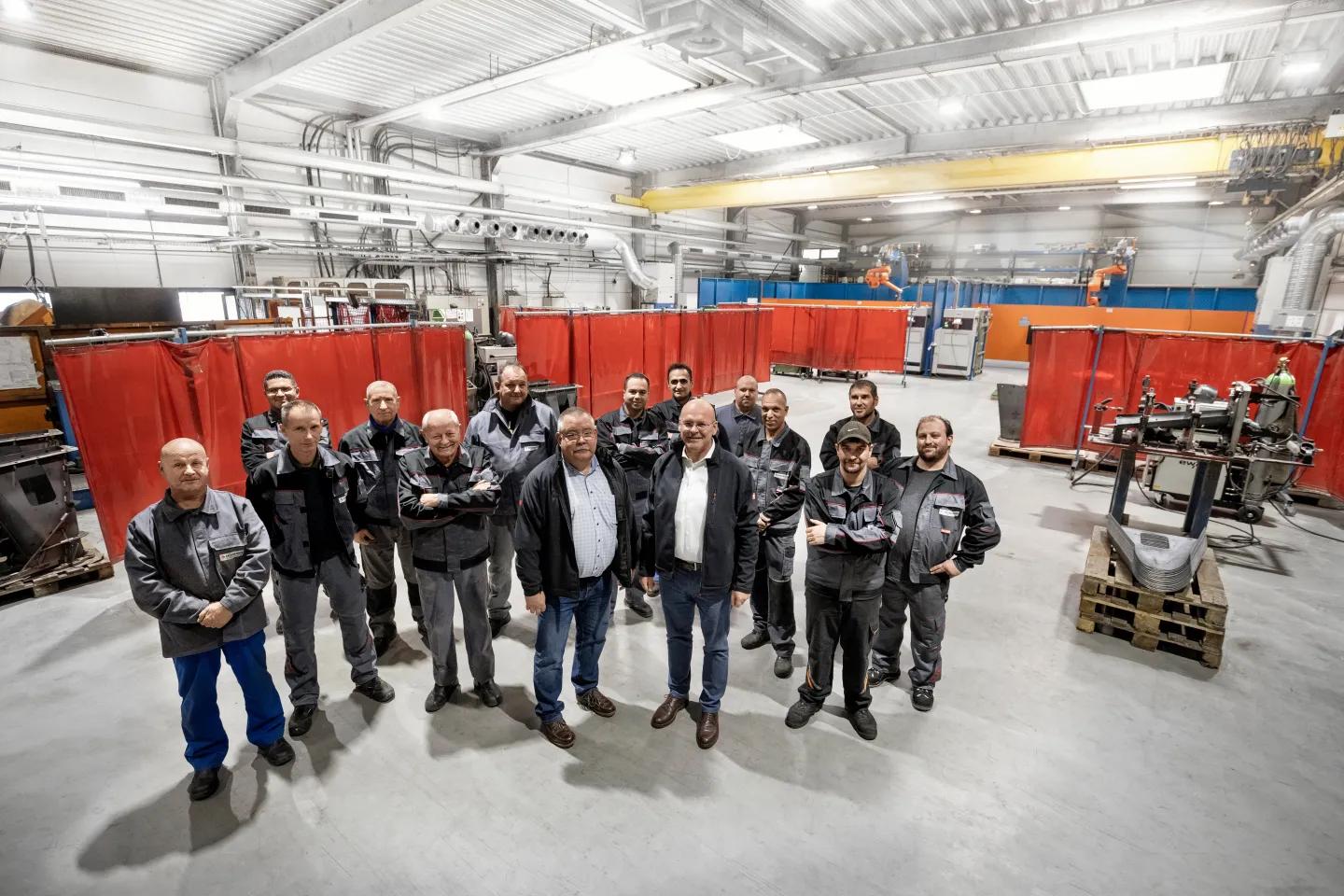
HÖRMANN Automotive Saarbrücken GmbH
Am Stahlhammer 65
D-66121 Saarbrücken
T +49 681 81908-0 • F +49 681 81908-19
info.saarbruecken@hoermann-automotive.com
Your Contact
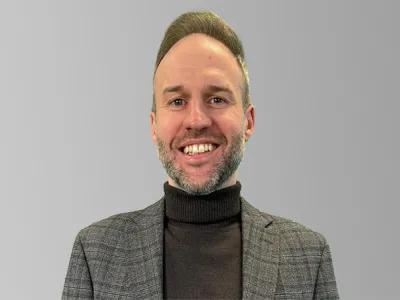